Types of Pipes
Drainage and sewer pipes are made from a range of different materials including vitrified clay, uPVC, concrete, iron and asbestos. This page deals only with solid pipes; perforated pipes for land drainage schemes are dealt with on the land drainage page . Most domestic drainage used in Britain and Ireland is either clayware or plastic, with the plastic uPVC drainage systems becoming more popular in modern, post-1980's properties, consequently, only clayware and plastic drainage will be considered here.
Other materials used for drainage pipes includes ductile and cast iron (CI), glassfibre reinforced plastics (GRP), high density polyethylene (HDPE), concrete, asbestos and pitch fibre.
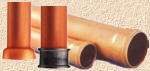
Socketed clayware
Plain-end clay c/w coupling
Plastic 100/150mm
Most new domestic drainage applications utilising clayware will use plain-ended pipes, rather than the socketed pipes. Plain ended pipes are those that have identical ends and are joined by means of a coupling. Socketed pipes have identifiable 'male' and 'female' ends, and must be laid with the 'female' end pointing upstream. Many older properties will have socketed clayware drains, typically of imperial dimensions. Builders' merchants usually stock a range of adaptors that enable modern, metric plain-ended clayware or plastic pipes to be connected onto the older socketed clayware types.
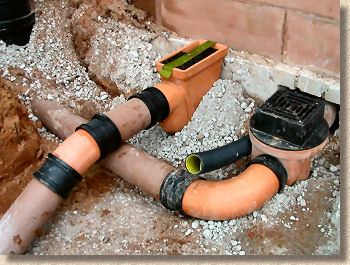
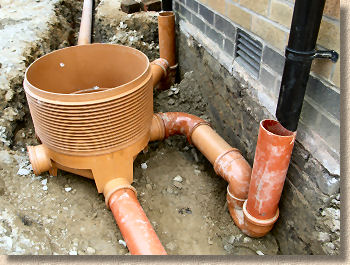
Both materials offer excellent hydraulic properties, and so it would seem that price should be the determining factor when it comes to choosing which type of drainage to use for your project. However, there are other factors that ought to be considered, not least of which is the relative inherent strength of each type, and the effect that has on laying techniques.
Vitrified clayware is much stronger than the plastic equivalents, and is less susceptible to deformation when buried; therefore, clayware relies less on the competence of the granular bedding material to withstand external loading. Clay pipes can often be laid directly into a trimmed and formed trench (known as Class D bedding), whereas plasticware MUST be surrounded by a selected small gravel or pea-shingle. This essential bedding material can often cost as much as, or even more than, the pipes and fittings needed for the job.
Which is better?
The range of fittings, bends, junctions, gullies etc., available for clayware is claimed to be greater than for plastic, and the flexible couplings of clayware offer more 'play' than the rigid plastic couplings. There are adaptor couplings available that will connect plastic to clayware and vice-versa.
Plastic pipes are much lighter and therefore easier to handle than clayware, and can be easily cut with a hacksaw, whereas clayware is heavy and needs to be cut with special pipecutters or a power-saw. Clayware is relatively fragile, and care must be taken during handling to avoid accidental breakages.
Although clayware dominated the drainage market 25 years ago, its market has been dramatically eaten into by plasticware over recent years. Now, however, clayware is fighting back and making great play of its claims to be a more environmentally friendly material in that it has lower energy costs during manufacture and requires less aggegates for bedding/backfilling. Further, the Clay Pipe Development Association is promoting the selling points that clayware is completely resistant to gnawing by the ever increasing rat/rodent population and is less likely to be damaged by high-pressure jetting techniques, which are becoming the most popular method of drain and sewer cleaning. Some clayware is now guaranteed to be capable of withstanding jetting pressures of 7,500psi.
Final choice of material lies with the specifier or the contractor. When extending an existing drainage system, we prefer to match the existing type, ie, extend a clayware system with clayware, and a plastic system with plasticware, unless the client or the specifier insists differently. For new work, we find that clayware is usually a little cheaper and offers better flexibility than plastic.
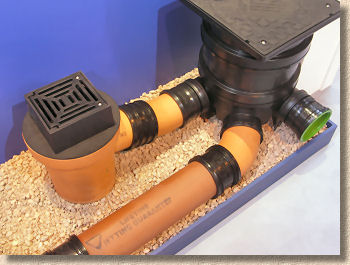
Most domestic drainage will consist of 100mm diameter clayware pipes, or 110mm plastic, although there may be some 150mm diameter pipes if the system is shared with other properties or is subjected to heavier-than-normal loads.
Bedding Types
Two typical bedding methods, one for each type of pipe, are illustrated opposite. There are numerous 'classes' of bedding for drainage, designed to suit all sorts of ground conditions, pipe types and anticipated loadings. Each class is identified by a different letter. For further detail, consult Approved Document H of Building Regs.
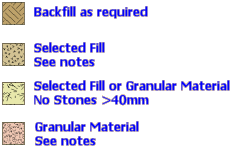
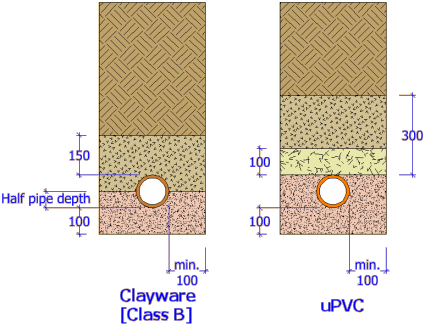
Bedding, sidefill and backfill
Selected Fill should be free from stones larger than 40mm, lumps of clay greater than 100mm, pieces of timber, organic matter or any frozen material.
Granular Material used for pipe bedding and sidefill must conform to BS EN 1610 - Annex B Table B15
Pipe dia.
(mm)
Max Particle
Size (mm)
Recommended bedding
100mm
10mm
5-10mm graded or 10mm single size
100-150mm
15mm
10mm single size or14mm single size or14-5mm graded
150-300mm
20mm
10/14/20mm single sizeor14-5mm gradedor20-5mm graded
Laying pipes
Safety First!
Pipes are typically laid within trenches and extreme caution must be exercised when working in trenches. Collapse of trenches is a very, very frightening experience (don't ask!), and has resulted in moderate to severe injuries, loss of limbs and, in far too many cases, loss of life.
Remember: all trenches are potential death traps and each must be assessed on its merits to determine whether shoring is required. As a rough-and-ready guide, any trenches deeper than 1.2m SHOULD be shored. Trenches are inherently unstable and unpredictable - don't take chances!

Busy Builder Fact Sheet from Britain's HSE
https://www.hse.gov.uk/pubns/cis64.pdf
- Do not have trenches open for any longer than absolutely necessary
- Use barrier fencing and/or security barriers to keep children and members of the public out of excavations
- Try not to have trenches open in inclement weather
- Try not to have trenches open too far in advance of pipe-laying
- Keep trench width to a minimum (generally pipe diameter plus 300mm)
- Always stand at least 600mm back from the edge of open trenches
- Never work alone in a trench - always have a 'buddy' or preferably a banksman
Pipe-laying basics
Typical laying methods for the 3 most common types of pipes are considered below. Handling, cutting and jointing will vary for each type of pipe and its associated range of fittings, but the general principles remain the same.
Pipes should be laid in straight lines to a steady gradient. A taut string line, sight rails or, more commonly nowadays, a laser line is used to ensure accuracy in alignment and level. The bedding is prepared in advance, with a recess scooped out to accommodate sockets, if necessary.
Pipes should be laid on a full bed of granular material and NOT propped up on bricks, bits of stone, broken flagstones, etc. The pipe should be settled into the bedding or have the bedding packed beneath it until it is at the correct alignment and level as indicated by the guide line (string or laser).
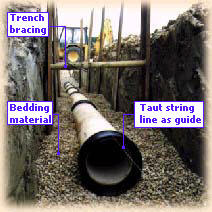
Laying Plain-ended Pipes (clayware or plastic)
As noted above, many drainage systems are termed 'Plain-ended'. This refers to the pipes, which have no integral socket and rely on couplings to join together pipes and fittings. This type of system has some advantages over socket and spigot types, in that the separate couplings offer greater flexibility and off-cuts from pipes can utilised by simply adding a coupling to each end.
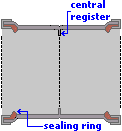
The ends of the pipes, whether they are plasticware or clayware, are chamfered when new. Pipes and fittings that have been cut may need to have the cut end chamfered on-site; cut ends to plasticware can be easily chamfered by means of a file, whereas clayware requires skilled use of a light hammer to 'fettle' the cut end, or the use of a special pipe-trimming tool.
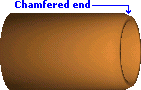
With all plain-ended systems, the basic laying procedure is the same...
- - lubricate end of pipe/fitting and coupling*
- - slide coupling onto pipe/fitting
- - lubricate receiving end of coupling and end of next pipe/fitting
- - slide next pipe/fitting into coupling
- - repeat as required
* using soap- or oil-based lubricant available from Builders' Merchants
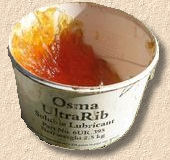
The actual process of laying plain-ended pipes and fittings is illustrated below.....
Laying plain-ended pipes

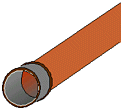

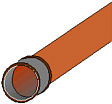
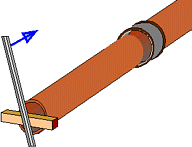
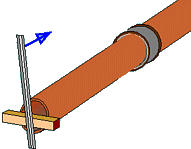
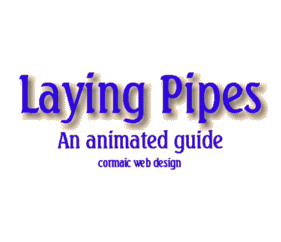
Laying Plasticware
Plasticware drainage is available with 2 types of jointing:
- Ring-seal
- Solvent-weld
Ring-seal is by far the most commonly used, with solvent weld used most often on installations subject to higher-than-normal pressures, such as pumped sewage.
The ring-seal pipes are similar to the plain-ended clayware discussed above. They rely on an elastomeric 'O' ring built into the coupling or the socket that is compressed against the outer wall of the upstream pipe or fitting when jointed, giving a completely watertight joint. Ring-seal jointing may be found as separate couplings or the pipes and fittings might have in-built couplings with identifiable 'female' and 'male' ends, known as sockets (f) and spigots (m).
As in the Laying Plain-ended Pipes example given above , the spigot or coupling is lubricated and the pipes brought together with gentle force.
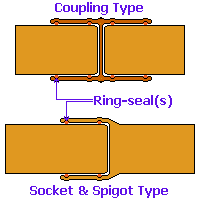
Solvent-weld systems rely on the pipes, couplings and fittings being 'glued' together by means of a special solvent. Individual manufacturers provide jointing instructions, and the correct solvents/adhesives for their individual ranges.
Again there may be separate or in-built couplings, depending on the particular system chosen. It is essential that the manufacturers' jointing instructions are followed to the letter, and that solvent cements are not mixed between different products/manufacturers.
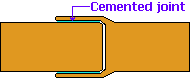
Laying Socketed Clayware
Socketed clayware pipes were once the most common type of pipe used for 100 and 150mm diameter domestic drainage, but developments in technology led to them being superseded in the late 1960's and nowadays, their main uses is primarily 150mm diameter or larger sewer systems beneath public highways. The older pipes are still in service on many older properties up and down the country, and may be known as 'salt-glaze', referring to their distinctive colouring, or 'stoneware'. It is usual for them to be replaced when exposed or excavated, rather than salvaged and re-laid, mainly because it is difficult to achieve a fully watertight joint with them, unless a labour- and material-expensive rigid mortar joint is constructed (see below).
Most modern socketed pipes use a nitrile or elastomeric 'O' ring to seal the joint between socket and spigot. The 'O' ring is stretched into the pre-formed groove on the spigot of the incoming pipe, the end of the spigot and the 'O' ring is lubricated, and gently forced into the socket in the same manner as shown above for plain-ended pipes.
This is a quick and efficient jointing system, but it is essential that the socket is kept clean and free from dust, dirt, grit, etc, before the spigot is inserted, otherwise the integrity of the joint may be compromised.
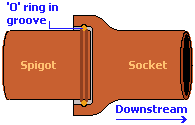
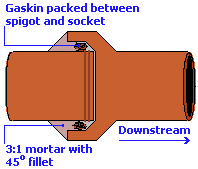
Mortar or 'rigid' joints on socketed clayware were once common with the old salt-glaze pipes (see above), but have limited uses nowadays. They are used for certain 'saddle' connections, on bends or other fittings, and for connecting to an existing socketed system. The gap between the spigot and socket is packed with gaskin, a type of tarred rope, and the joint is then pointed all the way around with a 3:1 mortar, filleted to make an angle of 45° with the barrel of the spigot.
Cutting Pipes
Although there is a massive range of fittings and accessories for the various drainage systems, it is inevitable that, at some point, a length of pipe or a fitting will need to be cut down to enable it to be fitted.
Plasticware is simply cut to size using a handsaw, full-size hacksaw or angle grinder, and then using a file to chamfer the newly-cut end.
Clayware (along with other harder materials) requires special cutting tools. The two most common methods are to use either a power cut-off saw or a pipe-cutting tool, which wraps around the pipe, placing a series of hardened-steel discs in direct contact with the barrel of the pipe, and then relies on pressure being exerted via the lever-handles to 'snap' the pipe at the required point.
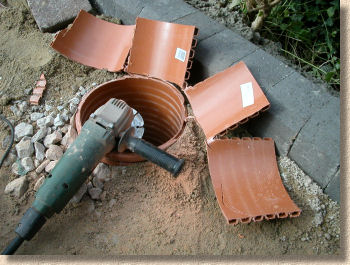
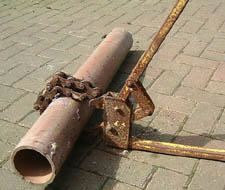
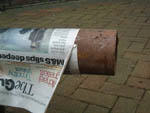
It is important that any cut is 'square' to the rest of the pipe or fitting. One simple way of acheiving this with straight pipes is to use a sheet of newspaper wrapped around the pipe. As long as the paper is 'snug' to the pipe, its edge will give a fairly accurate guide to 'square' and a line can be marked with chalk, slate or similar. With non-straight pipes and fittings, it is more usual to acheive a square-ish cut by eye.
Gradients and cover
Minimum Gradient
Minimum gradient for surface water drainage = 1:100
Minimum gradient for foul water drainage = 1:40 (1:80 if wc connected)
Minimum cover over plastic drainage
(Building Regs Part H 2015)- 600mm in fields/gardens
- 900mm beneath light roads/drives
Minimum cover over clayware drainage
(Building Regs Part H 2015)- 600mm in fields/gardens
- 1200mm beneath roads/drives
Encasing in concrete:
Note: If minimum cover cannot be acheived, the pipework will need to be encased in concrete. Any pipeline beneath a road that has less than 1000mm of cover, must also be encased - see diagram opposite.
A full width/height movement joint consisting of 13mm compressible board is typically included at every joint, although this may be changed to every alternate joint in some cases.
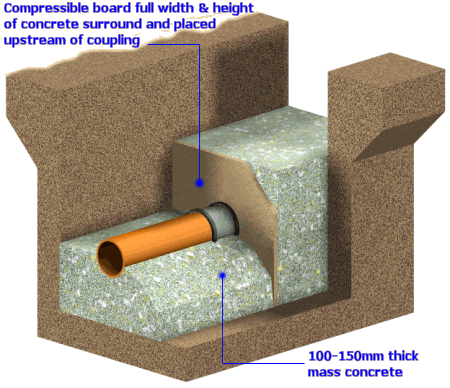
In many applications a so-called 'lean-mix' (something like a GEN1 ) concrete will be used for this work, but when there is concern about loading on the pipework, then a higher-strength C20 equivalent ( FND2 ), or even stronger, concrete would be used.
Fittings and Access Points
There is a huge range of fittings available for all types of drainage systems. These include gullies, hoppers, traps, bends, and junctions as standard items, as well as access chambers, rodding eyes and inspection chambers which are designed to grant access for inspection and/or maintenance.
Manholes tend to be larger chambers (at least 600mm width), with half-pipes known as 'channels' set into the base (see other drainage pages).
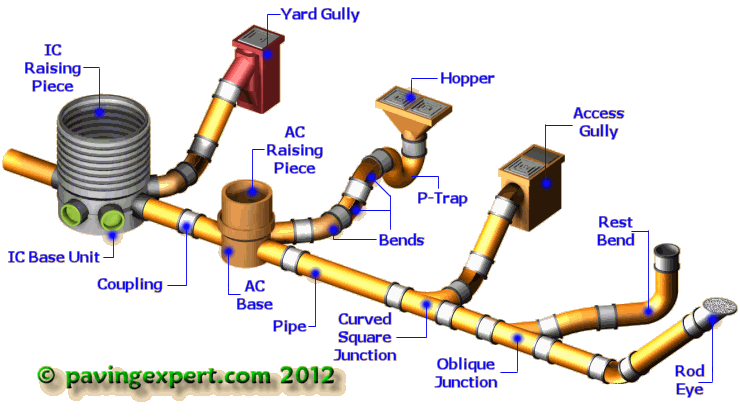
Access points:
(Rodding eyes, Access Fittings, Inspection chambers and Manholes)
These fittings provide essentialm access for inspection maintenance and repair, They must be installed at
- head of run
- bend or change of direction
- change in pipe diameter
- junction, unless all runs connected to junction can be rodded from another access point.
Further references:
- Building Regs England and Wales especially Part H
- Building Regs (Northern Ireland)
- Various British Standards - see list
- Sewers for Adoption - 7th ed. Design and construction guide for developers
SUDS Pages