The Laying Tarmacadam page looks at the methods used in constructing a tarmacadam footpath and an examination of the main layers within a pavement can be found on the Tarmacadam Construction page.
Uses and Applications
Tarmacadam, properly referred to as bituminous macadam or " Bitmac " for brevity, is often thought to be the cheapest method of surfacing a driveway or forecourt, but for smaller areas it can work out quite expensive, and the red tarmacadam can be more expensive than block paving. Tarmacadam has become a popular, although technically incorrect, term for both bitmac and for asphalt used to surface pavements, highways and even internal floors.
Surfacing contractors normally charge by the weight or area of material laid, but for smaller areas, they may charge on a daywork basis that will include transporting the requisite equipment to the site. A typical surfacing gang of 4 men (1 x Rake-hand , 1 x Roller Driver and 2 x Labourers) will cost around £100-200 per hour + VAT.
Bitmac is suitable for areas to be trafficked by vehicles, such as drives and forecourts, and can be used for paths, although we are not overly keen on using bitmac for garden paths. The wearing/surface course (the uppermost surface) can be 'coloured' by using a coloured binder, often with coloured aggregates, or by incorporating coloured, coated chippings into a HRA wearing course.
In general, all bitmac should be machine-laid by an paver machine except where it would be impossible/impractical to use a paver. Such exceptions include small areas (such as some private driveways), confined spaces and footpaths. On private works, the contractor will ascertain which is the most appropriate laying method to use. In most cases, the finish achieved with machine-laid bitmac is far superior to hand-laid material.
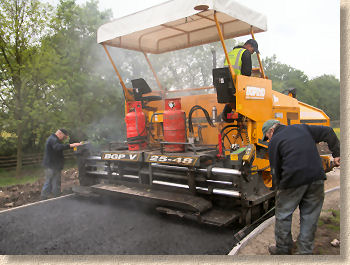
All bitmac should be laid by a professional company as the tools and techniques are beyond the reach of most DIY enthusiasts. Accordingly, the methods outlined on this site are intended to give the casual reader a guide to good practice, rather than a step-by-step guide to laying bitmac.
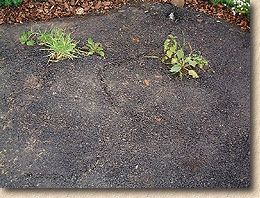
Armed with an understanding of how a bitmac pavement or highway should be constructed, you can check that the work being undertaken on your behalf is being done correctly. This is especially important given the large number of 'tinkers' offering to lay bitmac at a discount price - they usually just throw down a thin layer of wearing/surface course, safe in the knowledge that they will be long gone in a couple of weeks when your new drive starts to fall apart!
Beware of anyone knocking at the door offering bitmac 'left over from a big job down the road' - reputable contractors do not cold call to rustle up work!
Definitions
To try and clear up the confusion and get the terminology correct, here's a brief explanation....
- Bitumen is a product of the oil-refining and petro-chemical industries. Very basically, it is the thick, sticky, residual goo that's left over when all the useful fuel oils, such as kerosene, petrol, diesel, etc., have been extracted by fractional distillation of a crude oil.
- Macadam is a process of binding together smaller aggregates, as pioneered by the legendary John MacAdam in the 19th century (although there are tales of the Chinese having used a form of "macadam" as far back as 3000BC). His work resulted in the development of tar-based macadams, which became abbreviated to Tar-mac. Nowadays, we use bitumen from the oil industry rather than naturally occurring tar, and therefore we now have bitumen macadam or, as we call it in the trade, bitmac.
- Asphalt, according to British and European (CEN) definitions, is a mixture of bitumen and minerals. However, in the US, they use the term 'asphalt' for what we in Britain and the rest of Europe refer to as a Bitumen. This is the source of much of the confusion amongst non-trade professionals as to what's what and what's not.
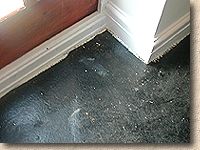
So, when Americans talk of asphalt roads they do not mean roads surfaced with the hard, shiny, black floor covering found beneath the carpets in many newer houses, and, for American readers, when you hear about British and Irish homes having asphalt floors, this is not the same stuff as used to surface your roads and sidewalks. Confused? Good!
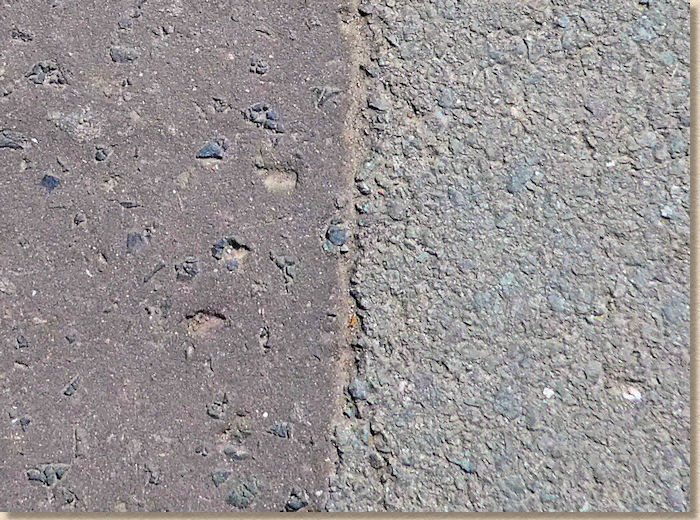
Two key properties....
Penetration Grades
Bitumen, the binder used in Bitmac, comes in a range of "penetration grades". There are specific tests that determine just what is the "penetration grade" of a given bitumen, but, rather than go into a lot of very technical and insomnia-curing detail, it is best to think of 'pen' as being a measure of "bitumen softness", of how far a point load will sink into a block of pure bitumen at normal temperatures.
The pen grade of the bitumen binder has a direct bearing on the 'hardness' of the bitmac produced using that bitumen, and so we have a range of penetration grades, from 15pen, which is pretty damned hard, to 450pen, which is relatively soft. A 'softer', more pliable binder produces a softer, more pliable bitmac. Imagine trying to push the blade of a Phillips screwdriver into a bitmac surface; some bitmacs will offer far more resistance than others, and a lot of that difference is dependent on the 'pen grade' of the bitumen binder. So, some bitmacs are harder, or softer, than others, and the degree of pliability can be tailored to suit the requirements of the job in hand.
As a sweeping generalisation, the harder grades (70pen or less), are used as 'asphalts', while the softer grades (100 pen or more, are used as binders for bitumen macadams (bitmac). Bitumens of different pen grades can be blended to create binders with a specific pen grade.
Cutback
Under normal circumstances, a bitumen would need to be heated to relatively high temperatures (150°-180°C) to make it 'workable' on site. However, there are all sorts of reasons why such high temperatures may not be achievable or even desirable, the most common of which is that the mixed material will lose heat as it is transported from the batch plant to the site. And so, the bitumen technologists have developed what is known as "Cutback", a technique that renders the bitmac workable at lower temperatures for longer periods. This effect is achieved by 'doping' the bitumen binder with a lighter oil (often kerosene, creosote or similar), which acts as a solvent, retarding the setting process until it has evaporated.
There are different grades of cutback (you knew there would be, didn't you!) ranging from slow-curing, through medium-curing to fast-curing. Medium-curing cutback is a popular choice for hand-laid work, as it gives a good degree of workability for a reasonable amount of time, but still gives a trafficable surface in a matter of hours.
Slow curing bitmac (aka Deferred Set Bitmac) is most often used by Local Authorities and the Utility Companies to effect minor or temporary repairs to roads and footpaths, because it can be stored in their depot or on the back of a normal wagon for several days, and then used as and when required. Once it has been compacted, it will achieve a degree of stability and be firm enough to carry traffic. This type of bitmac is the sort of stuff found in the 25kg packs of DIY/repair macadams sold in many Builder's Merchants.
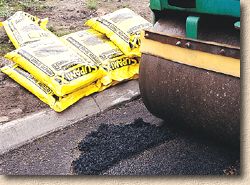
Fast-cure cutback bitmacs would normally be used in machine-laid projects, where a blast of additional heat from the Paver Machine will render the bitmac that bit more workable and easier to level accurately with the screed bar at the rear of the Paver.
Types of Materials
There are literally dozens of different types of 'tarmacadam'. Different aggregates, different aggregate sizes, different binders, different binder colours, the list goes on and on and there is a whole branch of the construction industry devoted to the specification of the various materials and the development of new products.
There are generic names for the multitude of surfacing materials, eg: a 6mm dense hardstone wearing course, and there are Proprietary Brands, eg: "ProDrive", a wearing course product manufactured exclusively by Bardon - Aggregate Industries . While "ProDrive" may be a 6mm wearing course material, not all 6mm wearing course materials will be "ProDrive".
Macadams are all based on the principle of an aggregate coated with a binder, usually bitumen, hence "bituminous macadam". Asphalts are a mixture of asphaltic cement or mortar (often a bitumen with fine aggregates such as sands and grits) and some coarser aggregate, such as gravel or crushed rock.
The major difference between macadams, other than aggregate size and pen grade, is whether they are classed as Open Graded or Close Graded (aka Dense). Open graded macadam is composed of aggregate with very little fines and may be permeable. It is a popular choice for hand-laid basecourses as it remains workable for longer at lower temperatures. Dense macadam contains a significant proportion of fines (material of 3mm or less). This means it is often classed as an impermeable material, and the tighter-looking finish make it a popular choice for wearing/surface courses.
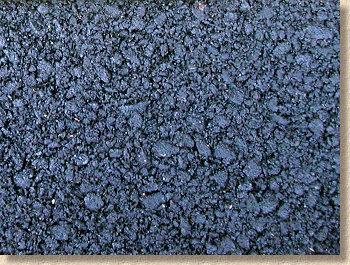
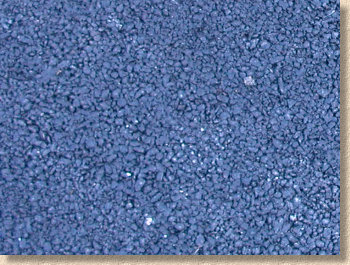
The choice of aggregate will affect the appearance of the surfacing in the medium-to-long term. All macadam (unless intentionally tinted) tends to look jet black when first laid, which is largely because the bitumen binder coats all of the aggregate, making it appear black.
As the surface is trafficked, the bitumen on the surface is abraded and weathered, exposing more and more of the bare aggregate content, revealing what may be a new colour.
Where a darker appearance is required over the longer term, a dark aggregate is required. This is often a basalt but other 'hardstones' are used, depending on what is available locally. In some parts of Britain, a granite aggregate, just as hard as basalt, may be used, but its lighter colour will result in a much paler, light grey appearance once the surface has been trafficked. In much or Ireland and parts of northern England, a limestone aggregate is a popular choice, and while not considered a 'hardstone' it is perfectly adequate for residential driveways, footpaths, car parks and other areas with minimal and/or slow vehicular traffic, but it will often wear to a very pale grey, almost white colour over time.
The thing to bear in mind is that the colour of macadam when first laid may well not be the colour it will be in 12 months' time.
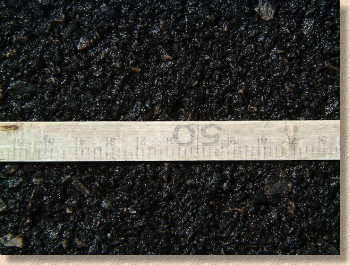
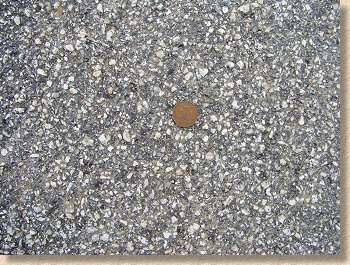
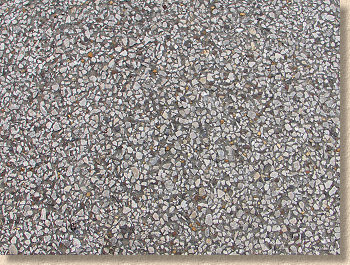
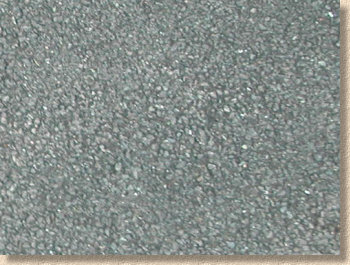
The Layers
...of a Bitmac Pavement
See also the Tarmacadam Construction Layers page.
The basic premise of a bitmac or asphalt surface is that the material is laid while hot and viscous, levelled and compacted as quickly as possible, and then allowed to cool so that it 'sets' and each particle is bound to its neighbours.
Bitmacs with large aggregates (up to around 70mm) are used as road bases or base/binder courses, and the smaller aggregates are used for the surface layer, more commonly known as the surface or wearing course. The general principle is that progressively smaller aggregates are used from the bottom of the pavement up towards the top, as this helps to spread the loads imposed upon the finished pavement by vehicles or other road users.
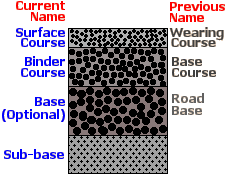
Euro-names:
During the recent review of British Standard 4987:Coated macadam for roads and other paved areas: Parts 1 and 2, the "Powers That Be", who wouldn't know which end of a tarmac rake to hold, decided that the terminology used for the layers of a tarmac surface are to be replaced as part of the ongoing 'harmonisation' with Europe. Road base is to become Base , while the base course becomes the Binder Course and the Wearing course is due to be renamed as Surface Course . In the long tradition of the UK and Irish Building Trade, we are totally confident that the older terminology will persist for many years to come.
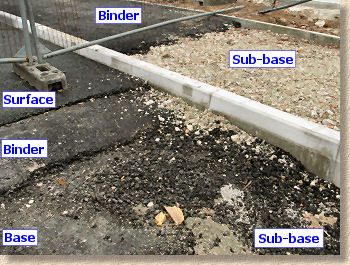
The photo opposite shows the various layers of typical bitmac surfacing.
On the left, the carriageway comprises a barely visible Sub-Base , overlain by a Base , then a Binder Course and finally a Surface Course which brings the level up to that of the watermark on the kerbline.
On the right, the footway is incomplete, and comprises (at this stage) only the Sub-Base and the Binder Course . The Surface Course was laid at a later date.
Surface (wearing) courses
There are three main types of 'bituminous' surface;
- Hand Laid Bitmac, for domestic driveways, footpaths and other small areas
- Machine Laid Bitmac for larger drives, forecourts and roads
- Asphalt (SMA/HRA) machine-laid as a wearing course on public roads. [1]
[1] - HRA on high speed roads is increasingly being replaced with SMA (Oh how we love these acronyms!) which is Stone Mastic Asphalt. This is a denser, tougher, more durable asphaltic material reinforced with fibres and has been shown to produce less traffic noise, much to the delight of the Highways Agency (HA). As with HRA, it must be machine-laid.
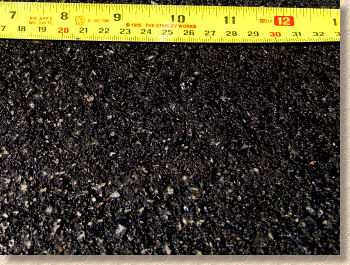
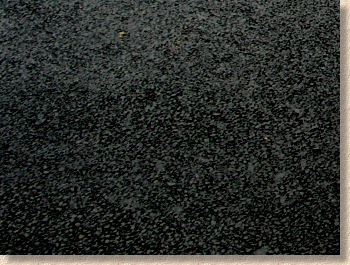
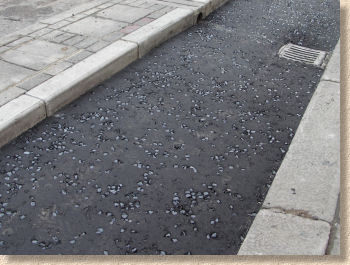
Mostly used on roadways
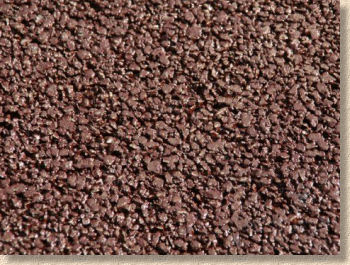
Photo by Dave L at RW Gale in Somerset
Construction
Construction of a bitmac pavement is dealt with on other pages. The various layers of a bitmac pavement are examined in the Tarmacadam Construction page while the working methods used in laying bitmac are described and illustrated on the Laying Bitmac Paths page.
Overlays
As mentioned elsewhere, a wearing/surface course may be laid over an existing bitmac or concrete surface. This is known as an "Overlay". The overlay surfacing should be a minimum 25mm thick and MUST be bonded to the existing surface with a cationic or anionic bonding emulsion, commonly referred to as a 'Tack Coat'.
Tack Coats
Tack coat is a browny-black emulsion of bitumen that is applied to the prepared, existing surface before laying the new surface/wearing course. The emulsion bonds to the existing surface, and then the new wearing course will bond to the emulsion, ensuring full adhesion. It also helps ensure that water does not find its way between the new and existing surfaces where it can freeze and lift off the new surface. The tack coat is absolutely essential in almost all instances of overlay work, the only notable exception being where a wearing course is laid over a recently laid (ie, within the preceding 7-14 days) base course.
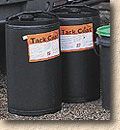
Tack coat is typically spray-applied to the existing surface at the rate of 0.4 to 0.6 litres per m². Some tack coats need to be heated prior to application; some are cold applied. On smaller jobs where a spray unit isn't feasible, the tack coat may be applied by a brush. The keys points are that the coverage should be complete, ie, no 'bald' spots, and there should be no pools of liquid on the treated surface. Tack coat 'breaks' (dries/sets/cures) in 10-15 minutes and is incredibly sticky when it does, so precautions may need to be taken to prevent operatives or vehicles crossing treated areas and picking up the bitumen emulsion as they pass.
Laying
The surface to be overlain must be clean and sound and free of organic material or other detritus. If the new material is laid over a badly cracked concrete base, old flagstones, or any other unsound base, any joints or cracks will soon be transmitted to the surface of the new bitmac, and the surfacing will fail.
This phenomenon is known as "Reflective Cracking" and is a well-documented problem for all overlay surfacing, not just with bitmac, but with all other surfacing materials, such as concrete and resin-bound aggregates . Any 'contractor' recommending an overlay of badly cracked concrete or old flagstones should be told to get back on his horse!
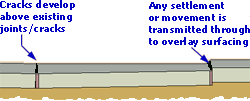
It is important that any proposed overlay to a residential driveway will not raise the level of the surface to an impractical height, such as at garage door thresholds, and that it the new surface is at least 150mm below any damp-proof courses in the brickwork of the house or garage. It may be necessary to cut-out 'keys' at the thresholds to accommodate the new surfacing.
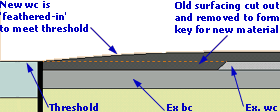
Also, the level of any utility covers within the pavement being overlaid will need to be adjusted. These include water Stop Tap boxes, manhole and inspection chamber covers, cable tv boxes, etc. Unless there is a significant "lift" in level of 50mm or more, gullies, linear drains and the like are best left at their original level and keys cut around them, much as illustrated opposite for a threshold, and then the new surfacing is feathered-in to meet the original level.
Pros and Cons
As mentioned earlier, bitmac can be a cheap, reliable surface over larger areas. Small areas can often prove quite costly as the 'set-up costs' of transporting a roller and other plant, an insulated bitmac wagon, and a laying gang account for a larger proportion of the overall cost. For residential driveways, it is often advisable to encourage a few neighbours to have their surfacing work done at the same time, thereby reducing the impact of the fixed, set-up costs.
All bituminous materials will slowly degrade in UV light, which results in the binder becoming 'brittle'. This is the primary reason why older bitmac drives often have a crumbly appearance and the aggregate tends to be scuffed free of the surface quite easily. While there are some products that can 'rejuvenate' old, tired bituminous surfacing, (See Bitmac Cover-Ups ) they may not work too well on badly deteriorated surfacing.
Modern binders are much more light-stable than those of just a few years ago and we estimate that a newly-laid bitmac driveway or pathway should give at least 10 years trouble-free service. We know of bitmac driveways that have survived in excess of 30 years, and while they may be deemed adequate for a private householder who requires only a firm surface on which to park the car, their condition is generally poor and, in the public domain, they would be deemed unsafe and warrant immediate replacement.
As bitmac is an oil-based product, spillages of light oils, petrol, diesel, paraffin etc. will dissolve the binder, and this dissolution can penetrate to a significant depth if left unchecked. The only remedy is to cut out the contaminated material and patch-in with new.
See FAQ covering the replacement of fuel-contaminated bitmac on a residential driveway
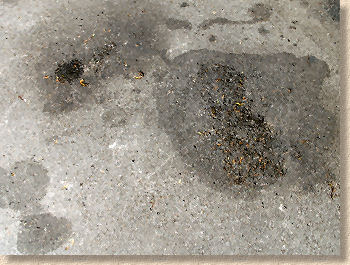
Bitmac, like concrete and other non-elemental surfacings, cannot be 'invisibly' repaired. Patching is the only solution, but will be obvious to the eye. If a sizable area is to be 'patched', it may be better to resurface the entire area, to maintain the pleasing appearance of a uniform surface.
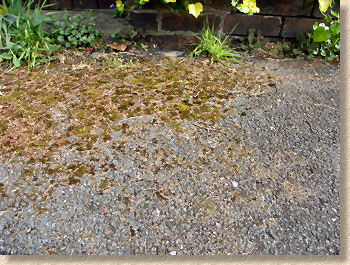
Untrafficked areas, paths and drives in shady and/or damp locations, and older bitmac surfaces are prone to moss and algae, which can become dangerously slippy. This is the main reason why we NEVER recommend bitmac as a surface for garden paths.
Surface vegetation is best removed by scrubbing with water, a general weedkiller and a stiff brush. Power washers can dislodge individual stones within the aggregate of an older bitmac surface and so should be used with care. Test out on a discreet corner before attempting to power-wash a larger area.
Bitmac must be properly levelled and laid to adequate falls that will drain the surface water to a gully or other suitable drainage point. Whereas a machine-laid bitmac surface can be laid to falls as tight as 1:80, hand-laid surfacing is particularly prone to small low-spots, and, in order to avoid the puddles that seem to afflict so many bitmac drives, a fall of not less than 1:50 is recommended.
Prices
The price of bitmac or asphalt surfacing is somewhat volatile, to say the least. As the key materials are all oil-based, their price is largely determined by the price of oil, which has a habit of rising and falling in an unpredictable manner.
Previously, guide prices for various "typical" installations have been given, but in the wake of the roller-coaster oil price white-knuckle-ride of recent years, it has been decided to withdraw price information as it became impossible to ensure accurate pricing from one day to the next. However, surfacing contractors are usually happy to provide prices for any work and so it is recommended that you enquire locally.
Construction Diagram
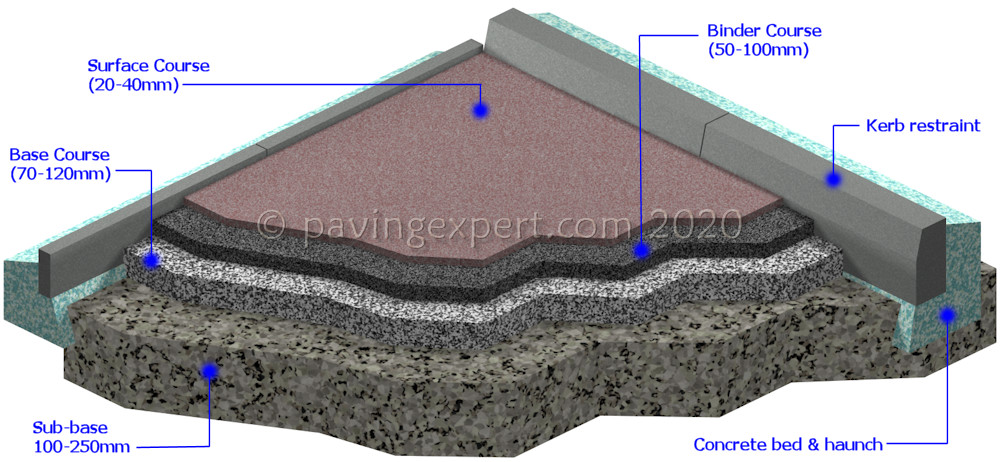