Introduction:
This page gives an overviews of concrete block paving while the following, linked pages consider various types of blocks and pavers, alternative construction methods, how to select the most appropriate block for any project, edge courses, kerbs and pattern establishment.
Use the links provided to learn more about the various aspects of this fantastically versatile paving material.
Uses and Applications
Block paving has been a major growth area in the British and Irish Paving Industry over the last 40 years or so. Mass production techniques have reduced the prices of manufactured blocks to a reasonable level, and made this type of paving affordable to most projects. In fact, concrete block paving costs only £3-6 per m² more than plain flags/slabs, when laid to a domestic driveway.
Brick or Block paving can be used anywhere. They look great on drives and will provide many years of service. They can be used to great effect as paths, or patios, or mixed with other paving types to create a unique feature. They are a viable alternative to the more traditional asphalt or macadam surfacing for estate roads, and let's face it, they look a lot better than tarmacadam or plain concrete . They are even being used in areas of exceptional loads, such as airport taxi-ways, docks and freight yards.
The design possibilities enabled by the use of these relatively small paving units are limited only by your imagination. If you can "see it in your mind's eye", then it can probably be constructed from block or brick paving.
Pavement Categories
Obviously, not all pavements or paving projects are the same. The loadings and pressures imposed upon, say, a freight yard with thundering HGVs and nimble stacker trucks, can't realistically be compared with those experienced by a back yard patio.
Consequently, pavements are constructed to different standards and this often requires different materials or different thicknesses (or depths) of the build-up layers. There's no sense in constructing, say, a 300mm thick reinforced concrete base beneath a typical block paved driveway, nor would it make sense to use, say, 50mm thick pavers on an airport taxiway.
Pavements are divided into Categories, with each category grouping together pavements likely to be subjected to similar loadings and stresses. In essence, there are four Categories (although Category I is split into two, just to confuse things), and the higher a Category number, the lower the loading it can support.
In practically all instances, patios, driveways, paths around the home and garden, and similar applications are a Category 4 pavement.
The full listing is given below:
Types of blocks and bricks
There two basic types of block paving; the moulded concrete block (CBP - Concrete Block Pavers), and the kiln-fired clay brick, hence the interchangeability of the terms block and brick paving. In the following notes, concrete types are referred to as blocks, and clays as bricks.
However, both may also be known as pavers, paviors, or paviours, as well as some more obscure terms, not all of which are repeatable in polite company!
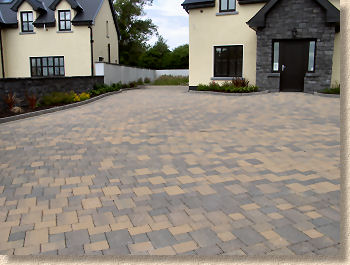
The bricks and blocks are available in a range of thicknesses, from 40mm to 100mm. There are even 120mm units for exceptional applications, but they are not likely to be found in stock at your local supplier! For domestic use, the 50mm or 60mm units are most suitable. 80mm thick units are used for road construction or where there will be regular vehicle overrun, while the 100mm thick units are for heavy-duty pavements such as those in Freight Yards, Ports and Airports. We find that the 40mm thick blocks are now (thankfully) difficult to obtain and offer no significant cost saving over a 50mm thick unit. They are/were also particularly prone to breakage during the compaction phase of construction.
Given the wide range of products on the market, choosing a block or brick paver for any given project can be a long, complex and fraught decision. Fuller consideration of the possible choices is covered on the Choosing a Block/Brick Paver page. What follows on this page is a brief summary of the main points.
Concrete Blocks
Amongst the concrete blocks there is an enormous variety of shapes, sizes, colours, and textures now available, with all the major concrete paving manufacturers producing their own versions of the standard rectangular block, and also special shapes, "olde-worlde" looking tumbled or antiqued units, and an ever increasing array of textured blocks.
Amongst contractors, specifiers and manufacturers, the blocks are often referred to as "CBP" - Concrete Block Paving
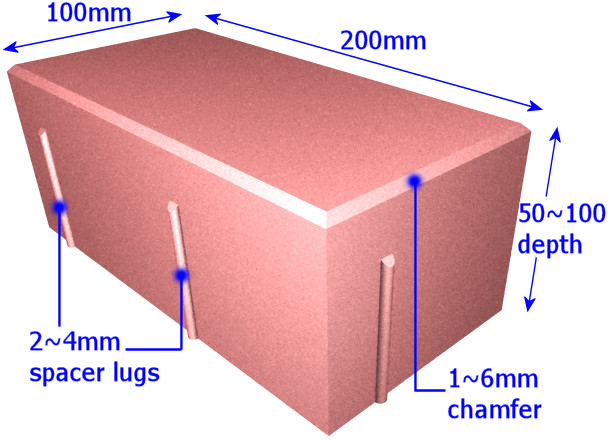
Most rectangular blocks are moulded to a specific size, 100mm x 200mm x 50-100mm, with exactly 50 blocks per square metre, and, because of this standard size, blocks from different manufacturers may be interchangeable, depending on tolerances and position of any spacer lugs. The typical rectangular blocks tend to have one presentable face, although some blocks are reversible, which makes easy work of replacing stained paving.
The colour of concrete blocks is achieved by the use of concrete dyes, usually some form of metallic oxide. Even the best dyes are prone to some fading in natural daylight and the quality of the dyes is a significant factor in block price; cheaper blocks are usually coloured by cheaper, inferior dyes. The manufacturers rarely entertain any complaints of fading, so choose carefully. Make your selection by looking at blocks that have been in place for at least a couple of years, rather than from glossy publicity photos or newly-laid paving.
Through-colour and face-mix
There are two manufacturing processes used to produce colour (and, to a lesser extent, texture) in a concrete block.
The first process, known as 'through colour', relies on placing all of the concrete (even though it may be three or more different colours of concrete) into the mould in one operation, and then pressing and compacting to create a unit that has the colour running right through the block, even though it's most likely that only the top surface will ever be seen once the paving is laid.
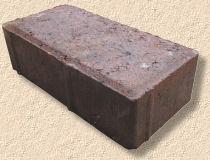
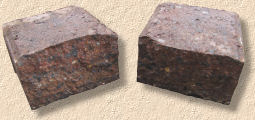
While this use of expensively-coloured concrete throughout the block may be considered wasteful, there are manufacturing cost savings, that have to be considered.
The alternative is to use a technique known as "Face Mix", in which a no-frill, un-coloured 'backing mix' or 'base mix' is first placed into the mould, partially pressed and then topped with a high-quality, coloured 'face mix' concrete. The whole is then pressed and compacted before being de-moulded and passed into the curing chamber.
There is a delay of only a very few seconds between placing the base and the face, so there is no day joint or construction joint, no plane of weakness, and absolutely no risk of delamination between the two. The block cures as one, single, monolithic mass of concrete.
Face Mix allows the money to be spent only on that part of the block that will actually be seen once the paving is laid.
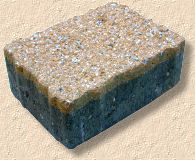
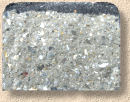
Face Mix technology enables the manufacturer to use cheaper, possibly recycled aggregates and alternative cements such as PFA and GGBFS for the backing mix, and to use amuch smaller quality of very high quality fine aggregates, cements and colours in the face mix.
While there may be cost savings, the production cycle-time for face mix manufacturing is greater than that for the through-colour process, and so less block per hour can be manufactured. There are also other costs involved in creating separate bins for face mix aggregates and separate hoppers for the face mix concrete once mixed.
It's not possible to say that one production technique is better than the other. Both have their advantages and disadvantages, and some special products, such as tumbled blocks, need to be through-coloured otherwise they would have just the one serviceable face. However, most production in Ireland, in continental Europe, and in North America use face-mix technology far more wideley than has been the case in Britain to date.
Read more about Face-Mix Manufacturing
Clay Pavers
Many of the "house brick" manufacturers produce their own ranges of clay paving bricks. These are generally available as typical, rectangular bricks, although there are now a good choice of size variations, from 60x60mm 'cobbles', 150x150mm 'setts' and 300x300mm squares. Custom shapes can be made for specific projects by some of the more co-operative manufacturers.
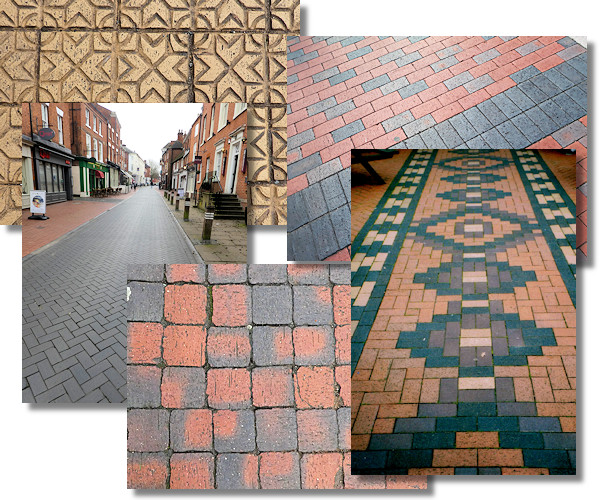
The most usual size is 100-105 x 200-215 x 60mm; this means that, with some bricks, there are less than 50 bricks per square metre, and that not all clays are interchangeable. Unlike the concrete blocks, most clays are manufactured with 2 presentable faces, allowing them to be inverted to replace stained paving.
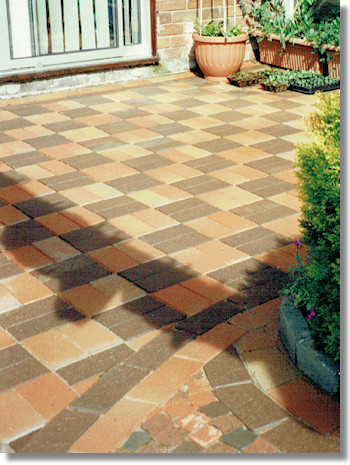
The colour of clay bricks is completely natural, not a chemical dye, and so these bricks are not subject to fading as are the concrete types. This use of natural colour also means that the range of colours available is almost limitless; reds, browns, buffs, greys, blues and a mass of multi-colour blends. If colour is an important factor in your project, clay bricks are probably the solution.
From a contractor's point of view, clay bricks are much harder to cut with a conventional block splitter than are concrete blocks, and it's worth hiring-in a diamond-bladed bench-saw if there are a lot of cuts to be made.
Unlike concrete blocks, all clay pavers are Through Colour, that is, they are homogenous throughout, solid clay which, while it may vary in colour due to the firing process and blending, is all the same material.
This becomes apparent when a paver is split open, as shown opposite.
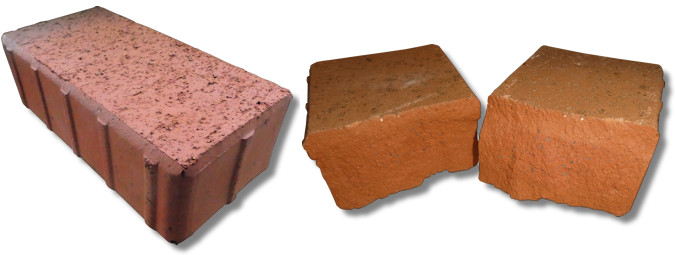
Note that 'house' bricks, 'facing' bricks or 'commons' ARE NOT SUITABLE for paving. They were never designed for that purpose, and often fail when wrongly used as a pavior, by flaking or cracking or just disintegrating in damp conditions. Conversely, paving bricks are not designed to build walls or pillars. Horses for courses, as they say.
More on Clay Pavers
Coverage Rates
Coverage rates are very straightforward, as block or brick paving is bought by area. It is wise to allow 5% wastage to allow for cuts and accidents. We 'round-up' to the nearest full pack of blocks or bricks, to ensure we have plenty. Surplus pavings can sometimes be returned to your supplier for partial rebate (a "re-stocking charge" of 10-20% is common)
Laying methods
There are two laying methods commonly used: flexible and rigid construction.
The most popular is termed 'flexible construction', indicating that the blocks or bricks are laid on an unbound (cement-free) bed and the joints filled with a fine silica sand. A detailed description of the methods used in laying a flexible pavement is given on the flexible construction page. There is also a step-by-step illustrated guide to a typical block paving project and a design guide for Highway and Commercial projects.
In Britain and Ireland, the overwhelming majority of flexible construction block paving is laid by hand, but some larger projects are Machine Laid , using specialist lifting equipment to place clusters of blocks in rapid succession. This technique is much more widely used on the continent and in North America and really ought to be more common on these damp islands.
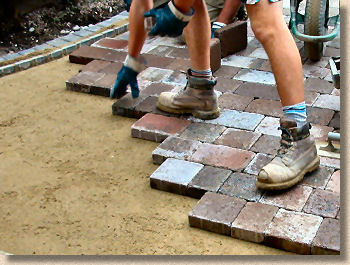
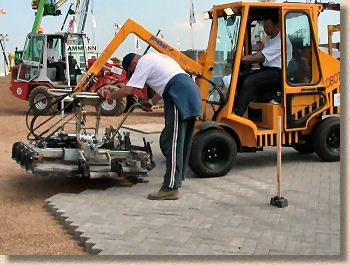
Rigid Construction refers to, usually, clay bricks laid on a concrete or mortar bed with mortar joints, much as a wall, although on the horizontal plane, rather than vertical. This type of brick paving uses completely different construction methods and is covered on the rigid brick paving page.
Maintenance
Medium level maintenance is required once laid. Sweep occasionally to remove dust and detritus. If you find green algae building up on them, it can be safely removed by cleaning or, we are told, by swilling the area with Jeyes Fluid to kill the algae, which can then be swept away after a couple of days. Use of a pressure washer should be limited to very dirty pavements and no more than once a year, as the high-power water jet loosens jointing and can damage some pavings.
We recommend that block or brick paving be treated twice a year with a general weedkiller such as Glyphosate, to deter mosses and weeds from setting up residence in the sand joints.
The clay pavers can prone to algal build-up on the surface, more than the concrete blocks. Should this occur, it should be removed regularly (Spring and Autumn) by cleaning, as it can become quite slippery. This phenomenon can be turned to your adavantage in a garden setting, where the clay bricks can 'age' dramatically with the appearance of mosses over a single season. There is significantly less algae/moss build-up on regularly trafficked areas.
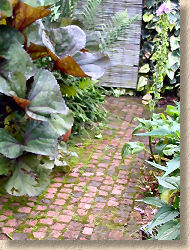
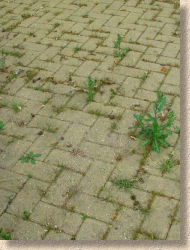
It's worth noting that, generally speaking, weeds grow INTO paving, not through it, unless it has been really badly laid. The claims made regarding the necessity or value of "weed barriers" beneath block paving are spurious and should be treated with caution. Read more about the use of membranes and geo-textiles beneath paving here .
There is a wide range of sealants available to protect the completed paving from colour degradation and oil spillage. The best sealants will repel oils, weak acids, dirt and weeds; the cheap ones are little more than glorified varnish.
Refer to Sealants page for more information.
Popular patterns
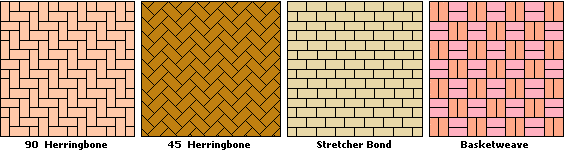
Pros and Cons
- Vast range of prices, from quite cheap to quite expensive. Large D-I-Y chains often sell rectangular concrete blocks for around £8-10 per m² including VAT, tumbled, 'olde-worlde' or shaped concrete blocks in the £12-£20 price range while clay bricks can cost up to £25 per m² or more.
- Make sure your chosen block meets the requirements of BS EN 1338 for concrete blocks, or BS EN 1344 for clay paving bricks.
- Very easy to obtain as they are carried by most Builders' Merchants. Most manufacturers publish free brochures detailing the range they supply. Ask your local builders merchant for a copy, or check out the concrete and clay paving links page for details on the larger manufacturers and how to contact them.
- If you see a block or brick pavement that you think would be ideal for your project, ask the contractor, or the resident for the name of the product and its manufacturer. Seeing a completed pavement is a far better way of choosing which type you want, than choosing from photographs.
- Must be properly drained to gullies or other suitable drainage points. Despite the dry sand joints, once a conventional block or brick pavement has established itself, it is virtually impermeable and all precipitation should be regarded as run-off water to be drained away from the paving. Alternatively, consider using Permeable Paving
Prices:
There is huge range of regional variation in pricing for block paving, from the sky-high costs of working in London to the highly-competitive rates charged in the conurbations of northern England, and then the problems of obtaining materials in The Highlands and Islands or Scotland, or parts of Western Ireland, and therefore the reliability of any price guide is called into question.
Consequently, the price guide that used to be provided has had to be withdrawn. We recommend you obtain at least three quotes from suitably experienced and established local paving specialists (rather than jobbing builders or all-rounder landscapers) to acquire a good idea of what the local rates should be.
Construction Diagrams
These drawings represent a flexible construction. Click here for rigid construction.
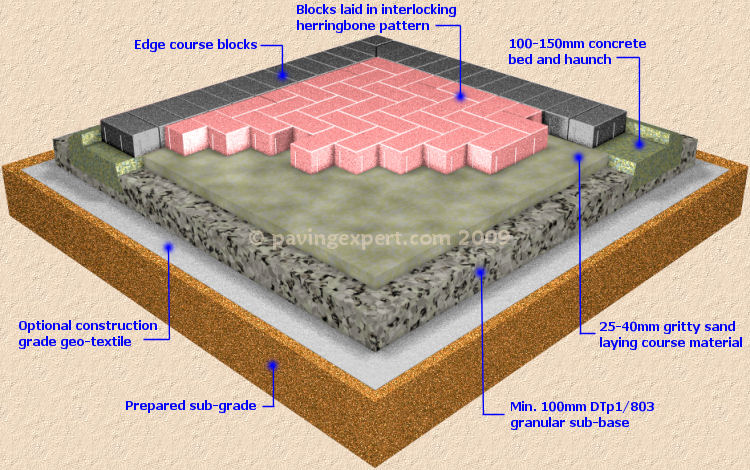
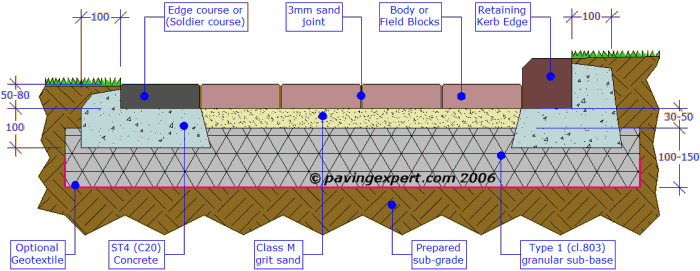