Introduction:
The mortar to be used is a general purpose Class II cement mortar, roughly 4 parts soft or building sand to 1 part Ordinary Portland Cement, mixed to a wettish slump, and incorporating a plasticiser to improve workability.
Tools:
- Pointing trowel
- Bricklaying trowel
- Pointing bar(s)
- Soft bristle cleaning brush
- Optional: Hawk

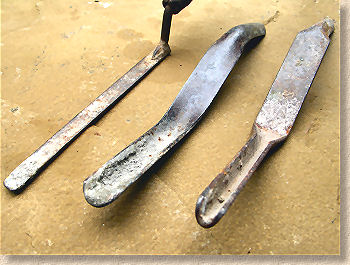
Technique:
The prepared mortar is loaded onto a large brick trowel. Any mortar overhanging the edge of the trowel is trimmed to prevent accidental spillage and stains. A smaller pointing trowel is then used to feed the mortar into the open joint, care being taken to avoid excessive staining on the edges of the paving units.
Once in the joint, the mortar is packed down using the edge of the pointing trowel until the section of joint is completely filled. This procedure is repeated, moving along the joint until the full length has been filled with mortar, and there are no voids or air pockets.
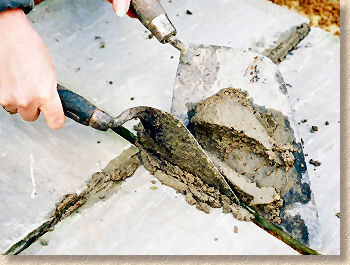
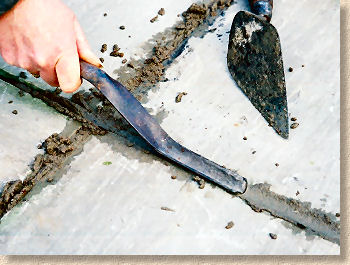
When the joint is filled, the mortar should be smoothed off (known as 'Striking' or 'Polishing') using the edge of the pointing trowel or a pointing bar/iron to create a snag-free, even surface. 12mm or 15mm diameter copper tube is sometimes used to fashion a cheap'n'cheerful pointing bar, but professional contractors tend to have a selection of steel tools with a variety of profiles, including rounded and V-shaped.
For those that are unsteady or determined to minimise any possible staining, the edges of the joint can be masked with cardboard, 4mm plywood, or proprietary "pointing aids" which generally involve some form of 'gap' in the centre of a protective sheet or mask, moving the gadget along the joint as work proceeds.
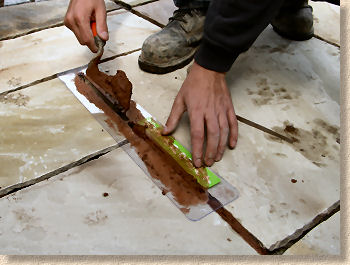
At one time, it was thought that striking a mortar joint was purely cosmetic, but it is now known that the striking action helps harden the mortar and make it less susceptible to frost or water damage.
Any spillages should be cleaned immediately: they WILL stain. Scrape up as much as possible using a trowel, but avoid smearing wet mortar over the pavement surface. Any residue can be sponged off using a damp cloth or similar. In hot, dry weather, small amounts of mortar on a paved surface will usually 'parch' and the dried residue can be removed using a soft brush.
Allow the mortar to become quite dry, say 1 hour or thereabouts on a fine, but not hot, day. Use a soft brush to sweep ACROSS the joint to dust off any mortar left on the surface of the paving. Collect up the sweepings and dispose. Re-strike the joints if required while the mortar has still not fully set.
On very hot days, we find it helps to shade the freshly pointed paving with lengths of timber, hessian sacking, cardboard or whatever we can find that will keep the direct sun off the joint, as this can cause to mortar to parch, to dry too quickly where the water content is evaporated away before the cement has had a reasonable chance to hydrate.
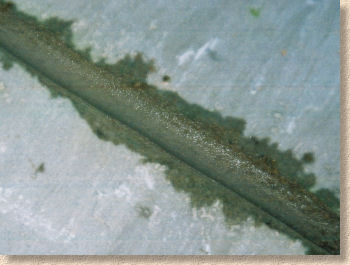
This mortar should start setting within 2 hours, faster in summer, slower in winter. It should be protected from foot traffic for at least 48 hours and from vehicles for at least 5 days.
Wash off all tools when finished - mortar is much easier to remove when still wet than when it has set.
Examples
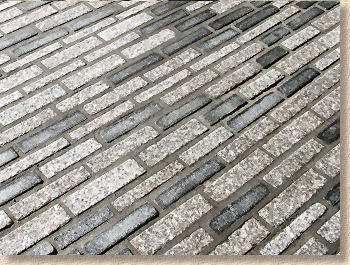
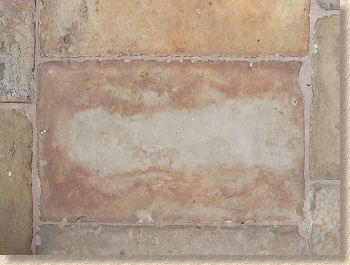
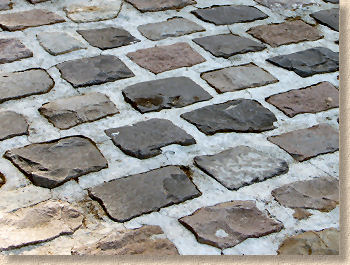
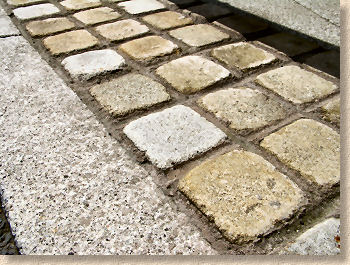
Comments:
Hand pointing is slow, tedious, back-breaking work that actually requires a great deal of skill and a wagon-load of patience to ensure a good standard of work. The coverage rate depends mostly on the size of the paving elements: it takes far longer to point a square metre of 80x80mm cubes than it would to point a square metre of 900x600mm flagstones. However, reckon on 1-3 minutes per square metre for flagstones and 5-15 mins/m² for setts or cubes.
Other pointing and jointing pages...
- Introduction
- Terms & definitions
- Pointing Styles
- Spacers for Paving
- Cement Mortars
- - Hand Pointing
- - Pointing Riven Flagstones Using Coloured Mortar: A Case Study
- - Wet Grouting
- - Dry Grouting
- - Slurry Grouting
- - Steintec Tufftop Slurry Grouting
- - Gun Grouting
- - Poured Grouting
- Resin Mortars
- - Polymerics
- - GftK Polymerics: A Product Study - VDW 840+
- - Romex Polymeric Mortars: A Product Study
- - Jointex Polymeric Mortar: A Product Study
- - Slurries
- - GftK Slurry Mortars: A Product Study - VDW 800 Permeable
- - GftK Slurry Mortars: A Product Study - VDW 850
- Re-jointing paving
- Pitch Jointing
- Loose Fill Jointing
- - Stabilisation
- Alternative Jointing Materials