Introduction:
Many of the terms used to describe the jointing and pointing of paving work along with definitions of some of the associated words and phrases which crop up repeatedly are explained on the Terms and Definitions page
There are several ways of sealing the joints between paving units: the end use and type of unit will determine the most appropriate method. Many of the most popular methods incorporate a cement and so create a solid, inflexible joint. This is what is normally referred to as "Mortar Pointing" or rigid pointing. An alternative strategy utilises a pure kiln-dried sand, and is typically reserved for flexible block paving , small element paving and some decorative patio flags/slabs.
The first of the linked sub-pages in this section considers the use of Modified Mortars and of polymeric sand , which is best thought of as a special sand that is chemically 'glued together'. The further page looks at some of the more unusual or esoteric other materials that can be used for jointing special paving or for designer paving.
There is also a separate page detailing a case study which illustrates the pointing of a flagstone patio using a coloured mortar, and a Product Study page looking at a range of high quality polymeric jointing products from Romex.
There is also a substantial section that considers the methods and materials used to joint stone pavements of all types. Some of these methods replicate those covered in this section, so there is some inevitable repetition but, in general, the information contained within the 'jointing stone pavements" section is more detailed and up-to-date so is well worth checking.
- Mortar Pointing - for flags/slabs of all types, and rigid block paving
- Coloured Mortar Case Study
- Pointing Styles - different forms and styles for mortar pointing
- Re-jointing paving - a case study following the re-jointing of a flagged patio
- Wet Grouting - for some flags/slabs
- Dry Grouting - for decorative patios
- Dry sand Jointing - for blocks, small elements and some patios
- Polymeric Sand - for all light-use paving joints wider then 5mm
- Modified Mortars - for wide joints and heavy use applications
- Other Materials - alternative materials for special paving projects
- Romex jointing materials - a product study
- GftK Epoxy Jointing Mortars - product study
- GftK Polymeric Jointing Mortar - product study
- Jointing Stone Pavements - Umpteen pages of methods and materials
Mortar Pointing
This is the most common method used for sealing the joints between flags/slabs. It is also used for rigid block paving and for pointing the joints that occur between sectional kerbs and edging units.
Timing
Ideally, when working with paving that has been laid on a cement-bound bed and or with buttering mortar, the pointing should be undertaken within 4 hours of the paving being laid, while the joints still have fairly fresh mortar within them from the buttering process. The pointing will 'top-up' the buttered mortar to form a solid mass with no day joint between butter mortar and pointing mortar.
However, if the pointing has been delayed for some reason, the joints should be checked before the work commences and any detritus or litter removed. 'Catch-up' pointing is best undertaken as soon as possible after the paving has been laid, and should be done on a fine day, when there is no chance of rain or frost.
Note that on very hot days, when undertaking 'catch-up' pointing, the relatively small amount of mortar used in each joint can dry out too quickly and crumble to dust in the space of a week. The biggest cause of pointing failure is exceptionally 'thirsty' flags sucking the essential moisture out of the pointing mortar before it has a chance to set properly. By hosing down the flags a few hours before pointing, it quenches their thirst and gives the mortar a better chance. On such days, it is best to leave the work until late afternoon or early evening.
Make sure the paving is dry on the surface before commencing the mortar work, as very damp or wet paving is more likely to stain.
Preparing the mix
The mortar should be a Class II and made up in advance as shown on the mortars page. It should be just damp enough so that it clumps into a ball when compressed in the hand, but no water should dribble out between the fingers. The 'wetness' of a mortar or concrete is properly referred to as its "slump" and most mortars have a low slump value, often 20mm or less, ie, they are fairly 'stiff'.
Never mix more than about a barrowful at one time, as the mortar starts to harden quite quickly and pointing can be slow work. The use of a plasticiser for pointing mortars cannot be recommended too highly - it makes the job 10 times easier.
The Pointing Process
Load some of the mortar onto a large brick trowel, and trim any overhang to prevent mortar spillage and stains. Assuming you're right-handed, hold the loaded brick trowel in your left hand along the joint you wish to point. Using a smaller pointing trowel, feed the mortar into the joint, being careful to avoid excessive staining on the edges of the flags/slabs.
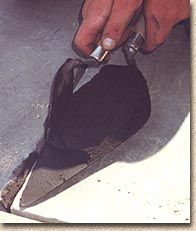
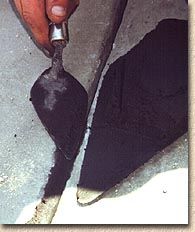
Pack down the mortar with the edge of the pointing trowel until the section of joint is filled. Move along the joint and repeat the operation until the entire joint has been filled with mortar.
If you are unsteady or determined to minimise any possible staining, the edges of the joint can be masked with cardboard or 4mm plywood, moving the mask along as you work.
Next, strike (polish) the mortar by running the edge of the pointing trowel at a slight angle along the top of the filled joint. Alternatively, the mortar can be 'polished' with a rounded, or even a V-shaped, pointing bar, which can be fashioned from a short length of copper tube.
At one time, it was thought that striking a mortar joint was purely cosmetic, but it is now known that the striking action helps harden the mortar and make it less susceptible to frost or water damage.
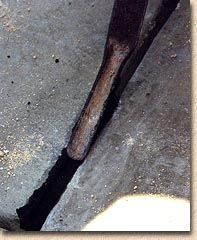
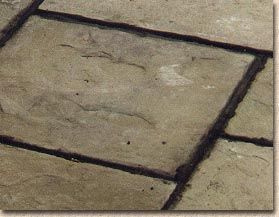
Allow the mortar to become quite dry, say 1 hour or thereabouts on a fine, but not hot, day. Use a soft brush to sweep ACROSS the joint to dust off any mortar left on the surface of the flags/slabs. Collect up the sweepings and dispose. Re-strike the joints if required while the mortar has still not fully set.
On very hot days, we find it helps to shade the freshly pointed flags with lengths of timber, hessian sacking or whatever we can find that will keep the direct sun off the joint, causing to mortar to dry too quickly.
This mortar should start setting within 2 hours, faster in summer, slower in winter. It should be protected from foot or vehicle traffic for at least 48 hours.
Wash off all tools when finished - mortar is much easier to remove when still wet than when it has set.
Wet Grouting - aka Slurry Grouting
This is a method rarely used to seal the joints between flags except on larger scale projects, when conditions favour its use, but it is a fairly common technique for jointing setts and cubes , which can have several linear metres of joint per square metre of paving. For flags, it is most often used on public footpaths, where a pristine and perfectly clean finish is not required but where a large area of paving has to be firmly jointed in a limited amount of time. It is also a useful technique for re-jointing an existing pavement that has several units that 'rock' or 'wobble' when trafficked.
It is not recommended on textured paving, or on any decorative paving where the appearance of the surface finish is paramount, as it can leave a thin veneer or "haze" of cement over the surface, which will weather away over time but is not to everyone's taste.
There are two sets of weather conditions that suit this method of sealing; damp or wet weather, and baking hot days. Conveniently, these are probably the two worst conditions for mortar pointing, so, between the two methods, there's usually some way of sealing the paving regardless of weather; snow and frost being the obvious exceptions.
The method relies on making a mortar slurry, ie, a very, very wet mix, with the consistency of a hearty pea soup. This slurry is brushed over the paving and into the joints. After a short period of time, usually twenty minutes to an hour, the excess is removed from the surface and the jointing struck or polished.
A Class II mortar is prepared as detailed on the Mortars page, although a plasticiser may be omitted. If it is not already wet, the surface of the paving is soaked with water from a hose - not just dampened, not simply wetted, but absolutely SOAKED. A very generous amount of pre-mixed mortar, about a half barrowful at a time, is dumped on the paving and very roughly distributed over the area using a spade or shovel.
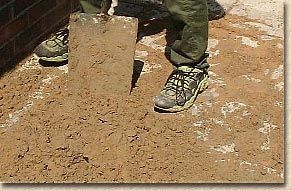
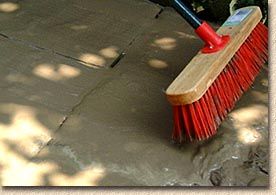
When a suitable patch, say 10m², is ready, the hose is once again brought into play, and used to saturate the mortar on the paving, brushing all the while, keeping the slurry in motion to stop the sand and cements from separating, while simultaneously guiding it into the joints. Once all the joints are filled, any surplus can be moved on to the next section or removed from the area.
Using a stiff brush, the area should then be repeatedly swept, at an angle of 45° to the direction of the paving joints, to progressively remove progressively more and more of the surplus mortar slurry.
In hot weather, the area can be hosed down, or left to dry in the sun, as long as the brushing continues more or less non-stop. If the "allow to dry" option is taken, repeated brushing ensures that no thickness of mortar is permitted to build up and 'adhere' to the paving, and any surplus gradually turns to dust, which is best removed by changing to a soft brush and sweeping again. This dry residue should not be re-used unless mixed with fresh cement.
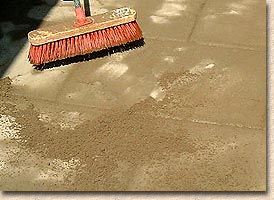
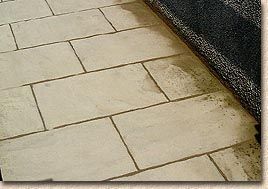
Hosing down is often used in damp or wet weather. The slurry is given a period of time to settle, and then the hose is played onto the surface at a shallow angle while a stiff brush is used to sweep the surplus off the paving. At no time should the hose be directed onto a joint, as it will simply blast out the mortar. It is important to hose down the area as thoroughly as possible - the cement is very fine-grained and tends to hang much more readily than do the sand grains. If they are not removed, they will set and stain the paving.
Finally, the joints are struck with the edge of a trowel or a pointing bar, topping up any joints that have settled.
As was mentioned earlier, this method of jointing is a useful technique on pavements that have a few loose elements, as the slurry seeps into places a normal mortar would never reach, filling voids and replacing lost bedding, and, hopefully, stabilising the pavement without having to undertake a complete "lift and re-lay" exercise.
However, it should be noted that because such a large quantity of water is used with this method of jointing, the strength of the mortar will be adversely affected. This is not a big issue on small residential patio or driveway projects, but on commercial and/or civic paving schemes where joint mortar strength is critical, then a stronger starting mortar should be used to offset the loss of strength due to the high water:cement ratio (w/c ratio - see Concretes page for fuller explanation). For projects where joint strength is critical, proprietary "high water content" mortars are available for use as a slurry jointing medium.
Dry Grouting
This is a variation on the wet grouting method described above, and can only be carried out when the surface of the paving is perfectly dry. It is a common method of jointing decorative patio flags, where a wet grout or a mortar pointing would cause unacceptable staining, and is sometimes used on public footpath works where the flags have been ' buttered ' with mortar prior to laying. On most flagging projects, it is a easy way to seal the paving effectively and keep the surface staining to a minimum, as long as the joints were buttered and the mortar used to butter the joints is still relatively fresh (less than an hour old). It is less satisfactory when the flags are dry- or butt-jointed, as the dry mixture does not to bond to the edges of the joints.
The 4:1 mortar mixture is mixed dry - no water is added at all, and it is essential that the sands and cement are thoroughly mixed together in the dry state before scattering onto the dry paving surface, and then using a soft brush to sweep the mix into the joints. Once an area has been covered, every joint is forcibly struck with the edge of a trowel to pack down the dry mix into the joints, and the process is repeated as required. Sweeping at an angle of 45° to the direction of the paving joints prevents the mix from being swept out of the joint. All surplus mix should be swept off and disposed, it can be re-used to seal other areas, if required, as, unlike the wet grout above, the cement content has not been wetted and is therefore still relatively fresh.
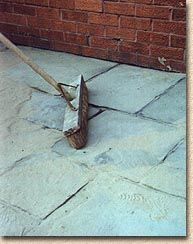
Once all the joints are filled, some contractors prefer to sprinkle the area with a fine spray to dampen the mixture within the joints, but we find this tends to splash some of the mix onto the paving surface.
We only use this dry grouting method with freshly buttered joints, where find that there is sufficient moisture from the 'proper' mortar to initiate setting of the dry mix. Dry mix into dry joints rarely, if ever, produces a good joint
Dry Sand Jointing
This method is used on all flexible block pavements, and on pavements constructed using small element pavers. It is also used with some decorative patio flags where a mortar joint is not required.
Three important points to note:
- there is NO cement used: None, nil, zero, zilch, nada, neamhní, nowt.
- the sand used is specially selected
- the surface must be dry
Building sand, playpit sand, beach or river sand, grit, coarse, bedding, soft and plastering sands are not normally suitable. The sand to be used consists of grains that fall within an upper and lower size range, to ensure maximum interlock between grains.
The table opposite is taken from Table D4 in BS7533:Part 3 and gives the grain size limits, but you'll be relieved to know that the aggregate companies have very kindly done all the sieving and sorting on your behalf, used a kiln to thoroughly dry the sands that pass muster, and then packed the results into convenient, if pricey, 25Kg polythene sacks, which are obtainable from most Builder's Merchants for £3 - £5 per bag.
If the sand is damp, don't accept it. It needs to be bone dry to 'flow', and you can get damp sand for a fraction of that price!
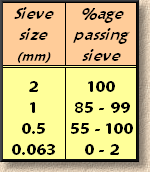
The surface must be dry otherwise it will simply dampen the sand, preventing it from flowing freely into the joints. We use a wide-headed soft brush to spread the sand and chase it into the joints. On block paving, some contractors like to leave a small surplus of sand on the surface before compacting with a vibrating plate, so that when the plate compactor 'shakes' the sand grains down tight into the joints, the surplus will be vibrated into the partially-emptied joints to ensure they are full. Properly filled joints provide the interlock that is needed to hold the paving firmly in place. However, there is an issue using this strategy with some jointing sands, because the grains can be crushed onto the surface of the blocks which can result in a near-permanent 'spot' stain, and so it is usually recommended that surplus sand is removed prior to consolidation to avoid just this problem. Additional sand, needed to top-up any 'hungry' joints, can be spread over the surface following consolidation.
Obviously, a vibrating plate compactor isn't suitable for use with most patio flags and so we have to rely on gravity and foot traffic to settle the jointing sand.
Once all the joints are full, any surplus sand is swept off and the job is complete. All sand joints, regardless of type of paving, should be checked after 4-6 weeks, as there is always some slight settlement that results in a small number of empty or partially-empty joints. Additional kiln-dried sand should be brushed-in as required. After 3-6 months, the sand will seal itself with detritus on the surface and become almost impermeable. Empty joints result in loose paving, so it is essential that sand joints are kept full.
Stabilising Compounds and Liquids
This section has been moved to this page
Associated Pages
- Basic Pointing and Jointing
- Terms & definitions
- Re-jointing paving
- Paving Spacers
- Pointing with a Coloured Mortar - A Case Study
- Polymeric Sands and Modified Mortars
- Other Jointing Materials
- Product Study - Romex jointing products
Jointing Stone Pavements
- Introduction
- Terms & definitions
- Pointing Styles
- Spacers for Paving
- Cement Mortars
- - Hand Pointing
- - Pointing Riven Flagstones Using Coloured Mortar: A Case Study
- - Wet Grouting
- - Dry Grouting
- - Slurry Grouting
- - Gun Grouting
- - Poured Grouting
- Resin Mortars
- - Polymerics
- - GftK Polymerics: A Product Study - VDW 840+
- - Romex Polymeric Mortars: A Product Study
- - Jointex Polymeric Mortar: A Product Study
- - Slurries
- - GftK Slurry Mortars: A Product Study - VDW 800 Permeable
- - GftK Slurry Mortars: A Product Study - VDW 850
- Re-jointing paving
- Pitch Jointing
- Loose Fill Jointing
- - Stabilisation
- Alternative Jointing Materials