Introduction:
The most popular products affected by the problems examioned here include beige or buff sandstones, pale limestones, travertines, and silver or light grey granites.
Much of this pale or light-coloured stone is sold as a premium product at a slightly higher price than the run-of-the-mill riven stone because this is said to reflect the cost of the additional sorting and processing that is required during its production. It is often calibrated to a particular thickness and much of it will have a textured or specially prepared surface which enhances (it is claimed) the colour and characteristics of the stone.
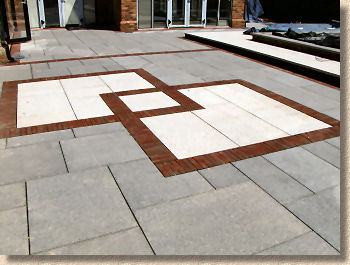
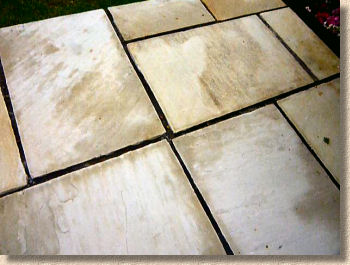
However, some of the lighter coloured products may be adversely affected by discolouration when laid using 'standard' bedding and jointing materials. This can appear as dark marks on the surface, pinkish or orangey staining on some or all of the paving, or distinctive 'picture framing' to the edges of affected individual flagstones.
Why it happens
This effect has been shown to result from a number of different causes, including contamination by dark-hued minerals within the bedding and/or jointing mortar moving into the porous structure of the stone immediately after installation, and movement of organic material naturally present within the stone brought about by the action of the alkaline solvents that are found in many cements. This latter problem is thought to be involved in many cases of discolouration in pale limestones.

Other than altering the choice of stone, there is not much that can be done about the migration of organic matter within the stone (the alkaline metallic hydroxides that cause it are present in virtually all commercially available cements), but there are some steps that can be taken to help minimise the risk of contamination from the bedding and jointing materials.
A suitable mortar
The disfiguring darker tones originate in both the sand and the cement used to make a standard mortar. Many native sands, especially those from land-based quarries, contain relatively high levels of iron particles. This is what gives the sand its familiar reddish or orangey-yellow tones: it is iron in a form similar to everyday rust. There may also be a relatively high quantity of clay particles present within a sand.
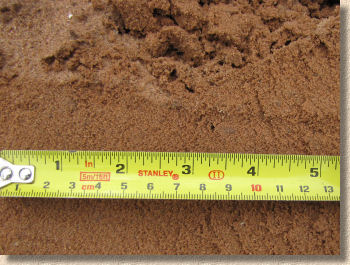
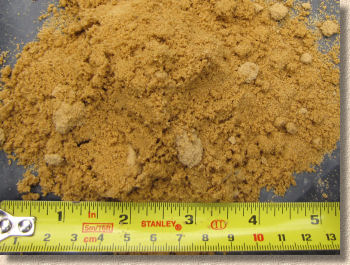
Ordinary Portland Cement (OPC) also contains many dark-hued components, ranging from the greeny-grey chromates, manganese and iron compounds which are found in most OPCs, to the clay particles used as filler. These give OPC, and the mortars and concretes created using it, a noticeable dark tone once it has cured. Further, many of these darker particles are either water soluble or easily transported by water, which is how they are transferred into the new paving.
To minimise the risk of contamination, it is usually recommended that a special mortar is used for both bedding and jointing. This mortar is prepared using a colour-neutral sand and a white cement.
What to use
The sand normally recommended is known as "Silver Sand". It is essentially the same as a 'standard' grit sand except that most, if not all, of the iron content and other dark minerals, are absent. Think of the much-vaunted 'silver strands' featured in the holiday brochures (although these are often beaches where the sand has a high shell content, rather than a cleaner silica sand).
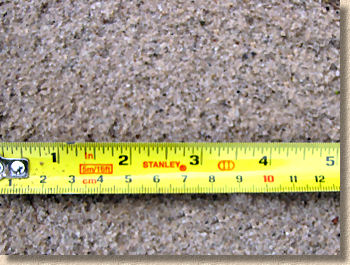
Similarly with the cement. In place of OPC, a special "White Cement" is used. This cement is manufactured to have a significantly lower content of dark minerals and often uses kaolin (aka China Clay) in place of standard clay fillers. It may also contain a small quantity of Titanium Dioxide (as used in white paint) to improve reflectance/brightness. All of this helps ensure a lighter, brighter cement and lighter, brighter mortars and concretes as a result, which explains why white cement is regularly used in the manufacture of light-coloured concrete screeds, pavings and masonry units, as well as coloured pre-mixed mortars. White cement significantly enhances the colouring effect when used with mortar dyes, particularly reds, buffs and even blues!
Costs and handling
It should come as no great surprise to learn that both silver sand and white cement are more expensive than the usual fare. Silver sand commonly retails at around three times the price of standard building sand, and white cement is typically three or four times the cost of OPC. Consequently, mortars and concretes prepared using these ingredients are more expensive, which pushes up the overall cost of paving installation.
These products are not always readily available and are more likely to be obtained from a Builders' Merchant rather than a DIY or Garden centre. Silver sand is sold under that generic name, but look for construction or builder's grade rather than the even more expensive horticultural grade (which is washed to remove any lime). For white cement, look for brands such as "Snowcrete" from Lafarge-Blue Circle, "Aalborg White" from Heidelberg, or "Rugby White" from, errrr, Rugby.
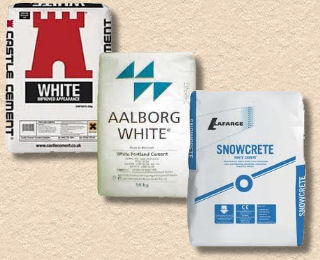
Mortars and concretes incorporating white cement and silver sand are prepared in exactly the same way as standard mortars, and using the same proportions. For paving a 6:1 mix is adequate for bedding but use a stronger 3:1 mix for jointing. Use a plasticiser to help minimise the quantity of water needed to mix the mortar and to improve its workability.
Handling and performance are more or less identical to those for mortars prepared using plain sand and OPC. There should be no noticeable difference in working life, curing time, or design strength. Maintain usual health and safety precautions (it might be white and more expensive, but is still burns bare skin like buggery!) and be sure to clean off any spills and stains immediately using water and a damp cloth or sponge.