Introduction:
It seems there are almost as many different types of paving sealants as there are types of paving and it can be totally confusing to decide which is the most suitable for any particular type of paver. The situation is not helped by some manufacturers claiming that their brand is suitable for any paving type, in any situation. Bear in mind the old adage regarding the inappropriateness of jack-of-all-trades.
There definitely are sealants that perform better with one form of paving or another, and there are a worrying number of concoctions that are potential paving despoilers. Sadly, the manufacturers of these snake oils are overly concerned with making empty promises about the panacea their product will deliver and fail to draw attention to the various shortcomings of their infernal compound.
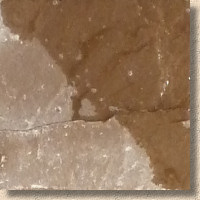
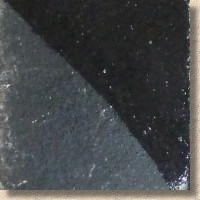
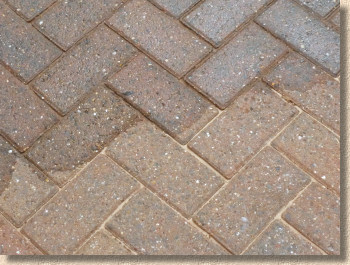
Any attempt to sort the multitude of sealants into appropriate categories would turn into a long and boring chemical analysis. There are polyurethanes (PU), acrylics, 1- and 2-part epoxy resins, fluoropolymers, silanes, siloxanes, waxes and umpteen more. While it may sometimes be possible to identify a most-appropriate chemical type for particular applications (such as PUs for concrete block paving), it is not possible to definitively state that any particular chemical type is best for all pavement surfaces.
Sealants can have a dramatic effect on the appearance of a pavement, and that effect may well be permanent and irreversible. That's why all sealants should be tried out in a discreet corner or on surplus paving before applying it to a wider area.
An extensive independent and impartial trial featuring 24 different sealants has been carried out by pavingexpert.com.
The procedure and results can be read starting at this page - Sealant Trials
Classes of Sealant:
Looking beyond the chemistry involved in each class of sealant, all of them can be assigned as either Coatings or Impregnators .
Coatings:
Coatings, also known as Surface Sealants, are those products which merely sit on top of the substrate , acting as a barrier between the paving material itself and the real world. These coatings are, generally, removable. Once applied they can be stripped using a product similar (if not identical) to paint-stripper. Some specialist sealants for other flooring materials may be not removable, but, in general, these are not suitable for use with stone or decorative concrete paving.
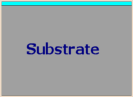
Impregnators:
These sealants actually penetrate the substrate itself, soaking into the microscopic interstices or capillaries which exist between the individual grains of a sedimentary stone or concrete, or adhering to the surface of mineral grains in other rock types.

Colour Enhancers:
Some sealants have no discernible effect on the appearance of the substrate following successful treatment, which may or may not be desirable. However, some people like the enhanced colours that are evident when flagstones (or blocks, setts, cubes, etc) are wet. This effect can be replicated by first treating the paving with a "Colour Enhancer", which works to accentuate the colour and deepen the tones, before applying the seal coat itself.
What's the point of all that, you may wonder. Surely, if you like the enhanced colouring then use a wet-look sealant! However, by separating the colour-enhancing function from the sealing function, you have much greater control over the finished appearance. You can apply as much or as little of the enhancing treatment as is required to achieve a desired look, and then apply the seal coat to complete the procedure, whereas relying solely on a wet-look sealant gives no fine control over the finished looks - it's wet-look, and that's it. If, after treating the paving with a wet-look sealant, you feel that the effect is too dramatic, or not as bold as you'd hoped, then you're stuck: there's nothing further you can do and additional coats of sealant will merely serve to darken the substrate, and not enhance the colour, whereas a colour enhancer can be built up, a bit at a time, until the required depth of contrast and colour enhancement is just as required.
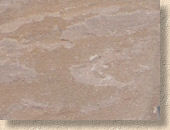
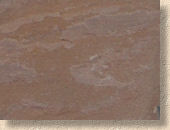
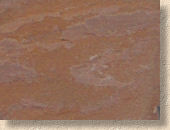
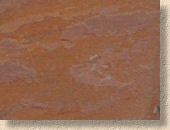
Using a colour enhancer allows the depth of colour to be gradually built-up to suit individual tastes
We trialled 14 different sealants and colour enhancers on black limestone to see which worked best. Read the results here .
Key properties
The two key properties for all sealants are their ability to repel oil and water. An ability to repel oil (oleophobic) means they will protect the paving from oils, fats and greases from cooking, from fuel or engine leaks, and to some extent, from accidental staining with some paints, tars and gums. The ability to repel water (hydrophobic) enables the paving to resist staining from water-based contaminants such as beverages, fruit juices, wines, beers and spirits, urine and faeces (from pets), and vegetable matter, such as grass clippings, leaves, etc.
A sealant that is oil repellent is nearly always water repellent as well, but a treatment that is water-repellent is not necessarily oil-repellent.
It's also worth noting that there is a significant difference between repellence and resistance. While a product that is repellent to oil and/or water based contaminants will actively protect the stone from such contaminants, an oil or water resistant product will only slow down or hinder the contaminant to a greater or lesser degree.
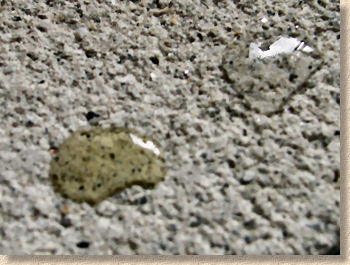
Pros and Cons:
Coatings:
- Tend to be relatively inexpensive
- Simple brush-on application
- May impart added slip resistance to some flagstones
Impregnators:
- Longer life-time as the protection is contained within the substrate, and not simply on the surface
- Usually not affected by UV light
- Allow the stone to 'breathe' and so retained moisture can escape
- tend to abrade quite easily, leading to obvious areas of scuffing or wear
- need to be re-applied quite regularly
- can build-up over time to impart a varnish-like appearance to the substrate
- low quality coatings tend to turn nicotine-yellow when exposed to UV light (sunlight)
- can trap moisture in the substrate itself, leading to problems with efflorescence or damage
- tend to be solvent based and may be noxious or harmful to the environment
- care needed when applying to ensure even coverage
- tend to be more expensive than coatings
Factors to consider:
Finished appearance
- Invisible - Wouldn't know there was a sealant present
- Damp-look – Colours enhanced but not shiny
- Matt/Low sheen - just a hint of shininess
- Wet-look – the full horror; shiny, varnished appearance.
Substrate
- Fairly permeable natural stone (sandstone)
- Barely permeable natural stone (granite, porphyry, basalt, slate)
- Wet cast concrete flagstones
- Pressed concrete flagstones
- Concrete block paving
- Clay pavers
- Plain concrete
- Pattern Imprinted or other Decorative Concrete
- Tarmacadam/bitmac/asphalt
- Resin-bound or resin-bonded
Repellence
- Oil repellent
- Water repellence
- Oil + Water repellence
Choosing the right sealant:
For commercial projects, the criteria used to select the best sealant will inevitably involve slip resistance, durability and wear, resistance to chewing gum, ease of application (particularly drying/curing time) and cost. Having seen a good number of sealant applications on commercial schemes, it's fairly apparent that aesthetics is often well down the list, somewhere after aroma, colour of tin, and catchy name.
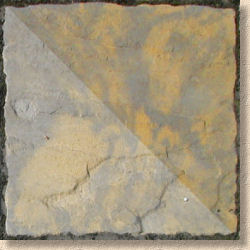
For residential contractors, reliability, cost and ease of application will be paramount. The primary concern is to provide a reasonable quality sealant for their clients with minimum fuss, risk or hassle. The last thing any good contractor wants is a sealant that causes problems which will involve additional (usually unpaid) work to make good.
DIYers and homeowners, meanwhile, tend to look for something at the local DIY shed, which is almost always the worst possible product for their project (see comments above regarding jack of all trades), but in their mind is preferable to being identified as a clueless civilian at a Builder's Merchant/Provider. Far too often, concern for aesthetics is virtually non-existent due more to ignorance rather than apathy. It's only when they realise their patio is now a shiny, glassy-looking horror that they discover there are alternative finishes.
Application:
There are several different methods of applying sealants. Many of the 'heavier' sealants, such as the Polyurethanes, are best applied using a squeegee, which ensures the whole of the surface is coated but prevents 'pooling' of liquid sealant in low spots. Other sealants may be applied by roller (as in paint roller) or via a sprayer. Less successful (but not impossible) is application by brush (paint brush or soft brush).
The surface to be sealed MUST BE DRY . Moisture on the surface, within the joints or even a bit of damp within the paving itself can cause some sealants to turn 'milky', effectively ruining the finished appearance. Those sealants sold as suitable for all surfaces (the jack-of-all-trades) tend to be more prone to this than some of the higher-end quality products.
Accordingly, we would strongly recommend that sealing should only be undertaken during the warmer, drier months, say May to October. While it is possible to seal at other times, the problem of residual moisture in the paving and relative humidity in the atmosphere can have unpredictable consequences. Further, we would also recommend that a sealant should not be applied until there have been at least three consecutive days of warm (>10°C), dry weather.
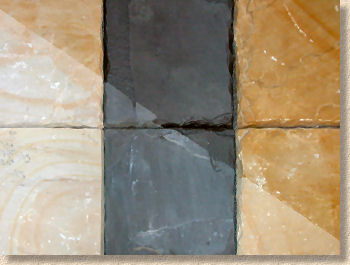
The paving should be clean, dry, free from dust, detritus and organic material (weeds, mosses, algae, etc). See the Cleaning Paving page for further guidance.
New paving should always be allowed to 'weather in' for at least 6 weeks before applying a sealant. Generally speaking, if there are to be any serious problems with new paving, they'll become apparent during those first few weeks, and so it makes sense to give the pavement a few weeks to see how it performs in use. Also, with sand-jointed modular paving (eg: concrete blocks, clay pavers, some flagstones), the jointing sand needs to be topped-up after a few weeks. Premature sealing not only precludes this essential topping-up, it can also exacerbate the problem by making loosely-filled joints seem properly full and thereby reducing the vertical interlock that gives this type of pavement its strength.
And if all that hasn't convinced you to wait a few weeks before daubing on the sealant, think about the potential for efflorescence . There's absolutely no point sealing-in the disfiguring white powdery stain. It's much better to let it work its way out of the paving and then undertake the sealing once the temporary period of eff bloom is over.
Coverage
Most sealants will require two coats for most effective results. The first coat onto previously untreated paving will often reduce the typical coverage data provided by manufacturers, but second and subsequent coats should see more square metres per litre. There is significant variation in coverage between the various types and brands of sealant, and particularly between different substrates. Very, very rough guidance is given below:
Sealant and Substrate
First Coat
Subsequent Coats
PU sealant on concrete block paving
1-3m² per litre
2-7m² per litre
Impregnator on sandstone
3-5m² per litre
5-15m² per litre
Impregnator on granite/basalt
10-20m² per litre
15-30m² per litre (if required)
Fluoropolymer on most surfaces
3-5m² per litre
Second coat not normally required
Sealants for Stone Paving
The use of stone paving has experienced a massive resurgence over the last decade or so. And not just in the commercial sector: the ready supply of low cost imported flagstones and setts have seen stone increasingly used on residential driveway and patio projects.
Understandably, installers and homeowners have considered using a sealant to enhance and/or protect the new stone paving, and this has resulted in a proliferation of allegedly suitable sealants on the market.
Given the huge variation in types, formats and quality of natural stone now available, compounded by the huge variation in quality of sealants, the section dealing with sealants for stone paving has been moved to a standalone page to allow more detailed examination of the issues.
Suggestions:
One of the most commonly asked questions by email and in The Brew Cabin is to recommend a sealant for a particular project. In fact, it's such a common question that there is now a FAQ to provide what will surely be regarded as a very unsatisfactory answer.
Hopefully, some of the above will have reinforced the idea that, if a sealant is genuinely necessary, then there is no one sealant that can be recommended for every job: all the factors already discussed will have an impact on choosing the most appropriate sealant for each job.
However, it is just about possible to compile a 'shortlist' of the most suitable sealants for a range of substrates and this is given below.
It is strongly recommended that samples of possible sealants are obtained and tested before being applied to larger areas. Contact details for the manufacturers and suppliers of all the products mentioned below can be found on the Sealants Links page.
For concrete block paving and pressed concrete flags
- Resiblock 22 (matt)
- Resiblock Superior (wet look)
- K-Seal Total (damp look)
- AdSeal (low sheen)
- USP (neutral)
For clay pavers
- Resiblock 22 (matt)
- AdSeal (low sheen)
- USP (neutral)
For cast concrete flags (patio flags)
- USP (neutral)
- Romex Seal (low sheen)
For porous natural stone
- Dry Treat (neutral)
- Weiss StainProtect Profi (neutral)
- Lithofin MN StainStop (matt/ barely damp look)
- ProtectGuard WL (wet look)
For crystalline natural stone
- Sio-Seal from RR Stone (neutral)
- Weiss StainProtect Profi (neutral)
- Lithofin MN StainStop (matt/ barely damp look)
- Wet Seal by Delta (wet look)
For PIC
- PICSeal (low sheen)
For macadam, asphalt, resin
- Not necessary