New plant for Kilsaran Concrete
Some of the original photographs used in this article have been changed on request from Kilsaran to protect their commercial interests. The photos supplied as replacements are labelled accordingly.
The phenomenal growth in the Irish construction industry as a whole, and the market for concrete block paving (CBP) in particular over the past few years has seen at least three new production plants come on-line in the past 9 months, the latest being the massive 20 million Euro plant built by Kilsaran at their Co. Meath headquarters at Dunboyne.
While it's been making blocks and flags for a while now, the impressive secondary processing facility, housed in the same building, is still being fine tuned, and the range of products the company is now able to manufacture is truly staggering.
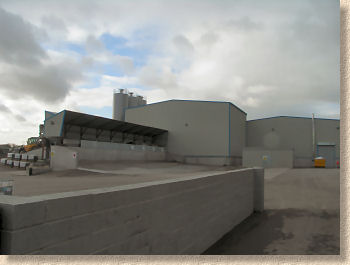
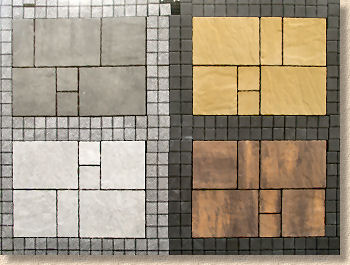
The main press is a Hess RH 1500-2VA machine from Germany, utilising a three-colour blending system from Haarup in Denmark, and turning out a little over 1 square metre of paving every 11.6 seconds (roughly 320m² per hour) from the enormous collection of Rampf moulds of every shape and size in which the company has invested. The freshly-pressed paving is directly transferred to the adjacent curing chamber, which is a great place to hide-out on a cold November day, being heated to a very comfortable temperature and fed with steam to enhance curing and minimise the incidence of efflorescence. In fact, it was so warm and humid that it was almost impossible to get a photo of the very clever inverting finger cart due to the camera lens repeatedly steaming-up.
Paving will spend anything from 6 hours to a couple of days in the curing chamber, depending on the actual product and the individual requirements of any secondary processing. Two feed lines leave the curing chamber; one carrying paving direct to the cubing and packaging area, while the second transfers blocks and flags to the relevant section of the secondary processing area.
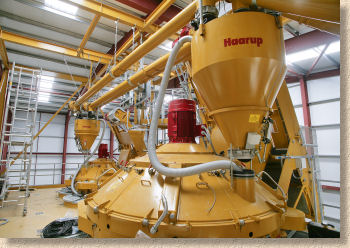
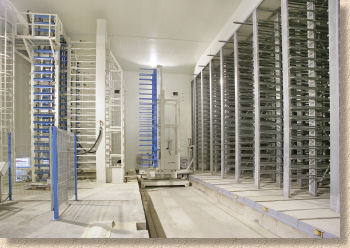
Anyone familiar with block and flag manufacture technology has probably dreamed about a set-up like this. No less than seven separate treatments can be applied individually or sequentially, as the product requires, before the processed paving is carried to the dry side for cubing and packaging. All of the secondary processing kit hails from the German SR-Schindler company.
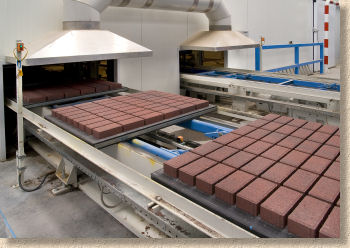
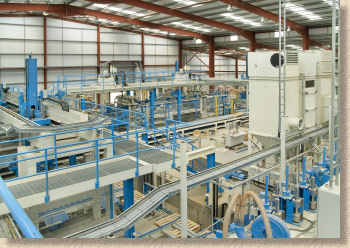
The first machine is a polishing/grinding line, which uses composite grinding heads to abrade the surface of the pavers, exposing the matrix and aggregate within, creating a terrazzo-like finish. Although diamond grinding heads are available for specific products, the standard abrasive heads will have a service life of just a few days before requiring replacement.
Alongside the grinder/polisher lies a line with two machines. Paving is passed along the line and subjected to one or both treatments as required. The first unit is the shot-blaster, which uses small steel balls to chip away at the soft matrix of the paving elements without overly damaging the coarse aggregate content.
From the shot-blaster, whether the elements have been blasted or not, the next process line is the new Curling machine, the results of which were first shown at Plan Expo in Dublin at the beginning of the month. In essence, curling involves using a series of six rotating cylindrical brushes with bristles of differing materials and stiffness, rotating at various speeds, which sweep over the paver surface, gently polishing it and creating an intriguingly smooth and silken finish that has to be felt to be appreciated. This new-ish technique (it's basically the same process as used to 'antique' imported natural stone paving, although the use of the word 'antique' can be confusing, as we'll see shortly) is claimed to render concrete paving easier to maintain, as well as reducing the quantity of sealants needed to treat any given area. What is certain is that the 'curled' surfaces are much kinder to bare feet and will certainly appeal to those looking to use one type of paving through the conservatory out into the garden.
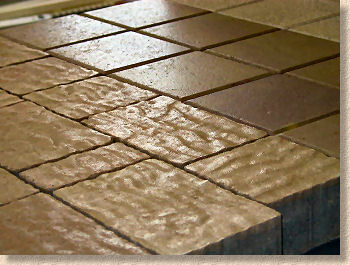
'Antiquing' is the term used in the secondary processing business to describe a technique that makes paving elements look worn or aged. However, there is now some discrepancy between the 'antiquing' process used for natural stone elements, particularly those from India and south-east Asia, and the techniques used in the production of concrete paving. Stone flags are 'antiqued' using the process described above as 'curling', whereas concrete pavers are 'antiqued' by distressing the surface, rather than brushing it. The traditional 'antiquing' process is tumbling: putting cured pavers into a rotating drum and allowing them to turn over and bash the living daylights out of each other. This is a dirty, dusty process, with relatively poor control of just how much 'antiquing' is done to each paver. The newer 'antiquing' machines, such as these at Dunboyne, use a series of mechanically-controlled vibrating hammers to delicately distress the arisses and upper surface of the pavers, and all without them ever leaving the layer in which they were manufactured and cured (the old traditional tumbling drums mix the paving units and require a further machine to sort the distressed blocks back into layers for cubing and packaging).
There's two sequential antiquing units here at Kilsaran, allowing them to be set-up to produce paving with a finely controlled degree of distressing, to one or both horizontal surfaces as required. The only issue I have with Schindler antiquing is the distinctive marks left on the surface by the vibrating hammers. Yes: these do disappear over a relatively short period of time thanks to trafficking, but when a contractor is attempting to sell paving to a less-knowledgeable private customer, it can be difficult to convince the client that the minor marks and scratches are a result of the manufacturing process and not caused by something the contractor has done incorrectly.
Beyond the antiquing machines is the hydraulic splitting unit, which will normally be used more with the rapidly-expanding range of walling blocks being manufactured by Kilsaran. Nothing overly fancy here, but it is the one machine that allows a full view of the conveyor belt system that collects dust and debris from all parts of the secondary processing area and carries it below floor level to a single waste facility.
The final machine (for now) is the bush hammer. This is a more violent version of the previously described antiquing process, with a series of pointy-toothed hammers of the type used as steak-tenderisers, which bash the paver surface, exposing the matrix and partially roughening the coarse aggregate to create a subtly different, more natural-looking finish compared to shot-blasting.
All of this kit is controlled from the floor via hand-held wireless devices that link back to a central control panel which can also be accessed via touch-screen from a single station, eliminating the need for operatives to enter machinery cages to adjust settings.
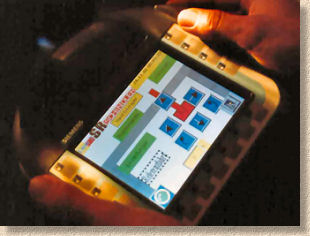
An in-house quality control laboratory and research workshop were being completed during this visit and should be up and running within the next month.
Overall, this is the most advanced paving manufacture plant I've seen this year. To be honest, the actual element production is nothing exceptional, but the enormous range of moulds that have been made available place it into a different league. However, what sets this place above any of the others is the secondary processing. The only technique not seen is a washing unit, but with at least five separate processes for paving alone now available to Kilsaran, I don't think they're going to be stuck for new ideas.
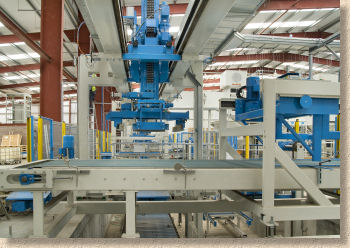
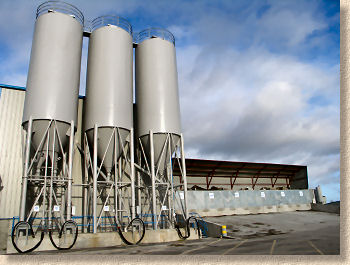
And the fruits of all this lovely new kit are already there to be seen. No longer will Kilsaran be a second division manufacturer churning out standard blocks with a potential upgrade to a dusty tumbled offering: now they are premier league, with the finance and the machinery to compete with anyone in Europe. Let's just hope the construction downturn doesn't spoil the party!
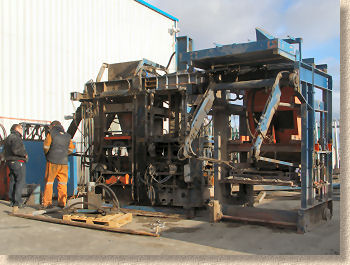