Introduction:
Originally developed as a cheaper, lighter method of providing a Grass Paved surface, the potential uses for these moulded plastic systems are being expanded all the time. In our experience, the largest area of growth over the last few years has been their use with gravels . They stabilise a gravelled area, making it much more user-friendly to both pedestrians and vehicular traffic, as well as reducing scatter and drift, problems that have troubled gravels and other loose surface dressings for aeons.
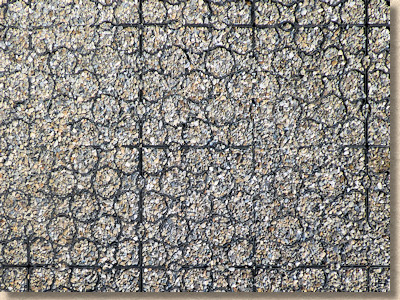
Uses identified for cellular/matrix pavers include occasional and/or overspill car parks, access lanes, fire access roads, caravan hardstanding, amenity areas and picnic sites, event areas, rural/canalside paths, helicopter pads, golf course paths and parking, erosion control and stabilisation of earthworks, along with applications for residential paths and driveways.
Core Gravel UK Ltd
Eco-friendly ground stabilisation and decorative landscaping products
Units 1-3 Calves Lane Yard
Iver
Bucks
SL0 0LU
Tel: 01753 652 555
sales @ corelp.co.uk
http://www.coregravel.co.uk/
Types
There is a good selection of systems on the market, and choice of the most suitable systems for any particular project will need to take into account planned usage, anticipated loads, volume and type of traffic, existing ground conditions, drainage and, of course, cost.
Many of the most popular systems are based on a hexagonal cell, although square cells systems are available. The key points to note with any system is the open percentage, both at the top surface and at the base.
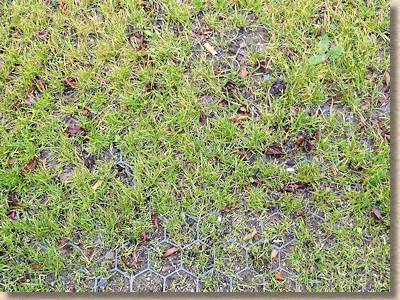
The open percentage for the top surface indicates just how much of the cell is visible once it's laid and filled. Most of the modern systems offer a minimum of 90% open surface.
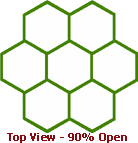
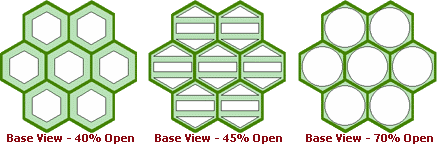
The open percentage for the base affects the load-bearing capacity of the system. The manufacturers need to find a compromise between a fully open cell base, which offers best drainage but will be driven into the laying course when trafficked, and a fully closed cell base, which offers best load-bearing capacity, but cannot drain through. A typical 'compromise' for the amount of open base is in the range 40-70% and many of the systems on the market are capable of carrying loads well in excess of 150 Tonnes per square metre.
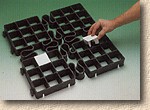
Some systems offer accessories and other 'extras' such as bay marking caps and edge units, but one big drawback is that the various systems tend not to be compatible, so if a project is likely to be extended or amended at some future date, it's essential to ensure the range will be supported by the manufacture for several years to come.
It is not necessary for this site to catalogue and detail the various systems available – comprehensive information on the products is readily available from the manufacturers listed on the Links page, and they will also be able to provide details of their stockists and distributors.
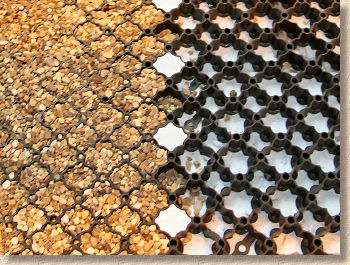
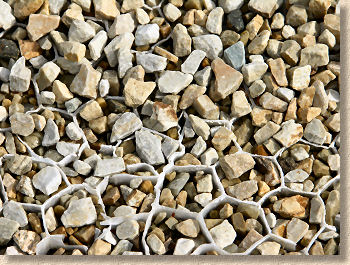
Construction
Sub-Grade
Although there are a wide variety of cellular systems available, the construction methods recommended by the manufacturers are fairly similar and a typical construction is detailed here. The sub-grade is prepared by removing vegetation and other unacceptable material and then digging down to formation level, creating a reasonably level and compact sub-grade in the process. A drainage composite or separation membrane is often recommended and this should be installed as directed by the manufacturer at the sub-grade/sub-base interface.
Sub-Base
The sub-base layer is typically constructed from a selected free-draining material depending on the planned end use of the surface. Where light and/or occasional vehicular traffic is expected, a traditional Type 1 or 2 sub-base material may be used, often incorporating some form of integral drainage, but on those projects where sharp drainage is the prime requisite, the sub-base is more likely to be constructed from Type 3 Close Graded Aggregate , a gravel or an approved filter medium. Other projects may opt for a select fill.
Sub-base thickness will vary according to planned usage and ground conditions but is generally somewhere between 100mm and 200mm as a minimum.
Kerbs/Edgings
Although kerbs and/or edgings are not always essential, they can improve the finished appearance of the paving by providing a neat and tidy edge. On projects subjected to regular vehicular traffic, then a kerb/edging is beneficial as they help restrain the matrices and prevent slippage or movement under turning forces.
Transverse restraining edgings are also a good idea when cellular matrices are used on gradients. As the name suggests, these are laid across the slope to prevent slippage of the units under load or because of gravity. The amount of separation between transverse restraints will vary depending on the gradient itself and the ground conditionsb but is generally somewhere between 4m and 10m.
Transverse restraints are typically a rigid edging, most often a flat-topped edging kerb (Type EF) laid on and haunched with concrete. Where only occasional traffic is anticipated, a securely anchored timber edging may also be used.
Almost any form of edging or kerb is suitable; where a rustic or natural look is required, a timber edging may be preferred, but for traffic schemes, a concrete edging may be a better choice. If edgings/kerbs are to be used, then they should be installed at this stage, ie, before placing and screeding the laying course material.
Laying Course
The laying course material for most cellular pavers is typically a grit sand. However, some manufacturers prefer to recommend a mix of sand and selected topsoil (usually 2 parts sand to 1 part soil) for use as the bedding layer when the cells are to be grassed.
The chosen bedding material may be laid over a separation membrane if there is a potential problem with the laying course material settling or being washed into the sub-base, or, in the case of grass paved cells, if there is the need to prevent the roots of any vegetation penetrating the sub-base.
The prime purpose of the laying course is to provide a well-profiled bed for the cellular tiles, and so thickness is kept to a minimum, generally 35-50mm, although this may be increased to 60-100mm or so where the cells are being used to support grass or other vegetation.
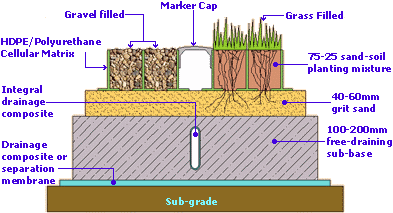
The laying course is prepared is the same way as any other screeded laying course and the methods used are described on the Screeding page.
Laying the Cells
Finally, the cellular tiles themselves are laid in accordance with the manufacturers' instructions. Some systems rely on small pegs or pins that are driven through adjacent units into the laying course and/or sub-base, tying the units together and anchoring them in place. Others feature a click-together system or lock-pins that connect adjacent units.
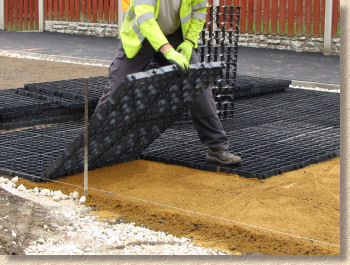
Full units are laid first and then the gaps are in-filled with units cut to size using a basic saw (hand saw, hacksaw or power saw). It is not usual for the unfilled units to be compacted: this is typically carried out once the cells are filled with the chosen material, be it gravel, soil or some other loose fill.
In the case of grass paving, the soil fill should be in accordance with the manufacturers' recommendations, which is normally a free-draining sandy loam type of soil. Care should alos be exercised in choice of grass seed to ensure a tough, hard-wearing mixture is selected.
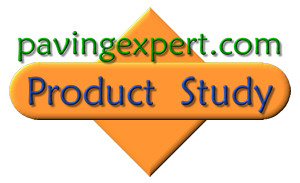
A comprehensive case study following the installation of Ground Reinforcing Grid System plastic cellular pavers to a multi-vehicle parking area can be found on a separate page by following this link
Gallery
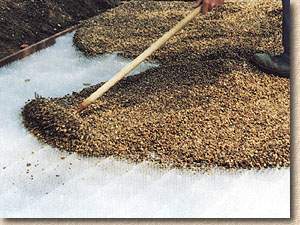
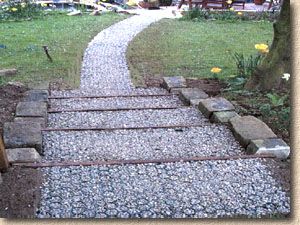
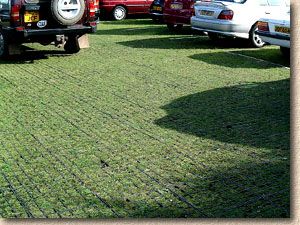
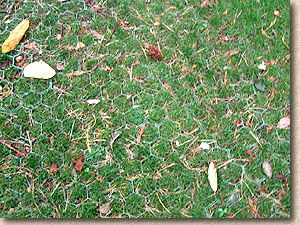
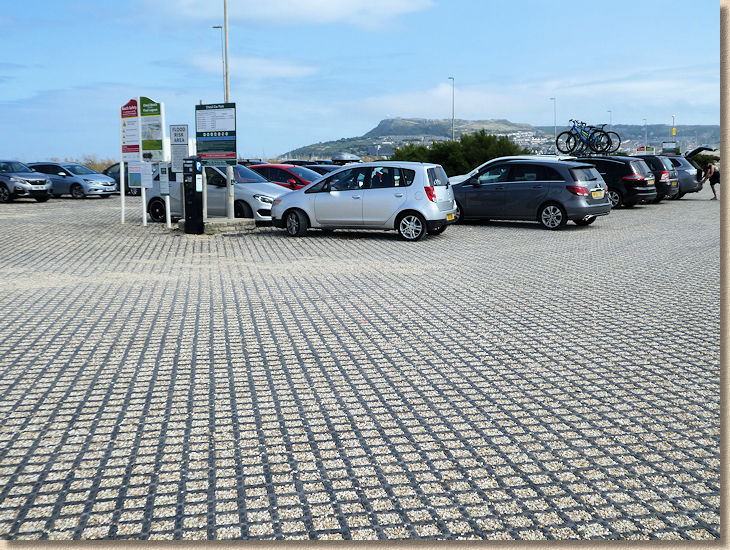
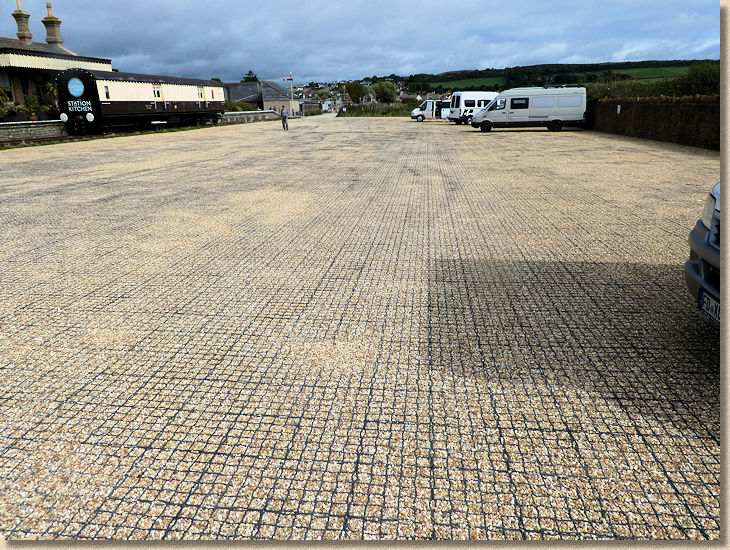
Construction Diagram