Introduction:
Permeable paving is a relatively recent introduction to the British and Irish paving markets, but one that is set to dominate the trade in the coming years due to its critical role in the future of our towns and cities. It is one of the key technologies behind SUDS - Sustainable Urban Drainage Systems - as it enables "Source Control" , control of storm water at its source, rather than at some treatment works several kilometres downstream. As more and more of the country is developed and an ever greater area is covered by roads, pavements, roofs and other buildings, two problems have come to prominence; the increased load we place on our already struggling sewer systems and the risks posed to our delicate treatment systems and watercourses from pollutants originating on the traditionally-drained impermeable surfaces. SUDS aims to address this problem - read more about it on the SUDS Introduction page .
As the percentage of open ground is reduced, rainfall that would have been naturally absorbed and retained by the ground is diverted, resulting in large volumes of run-off water that have to be channelled via sewers that may be over 100 years old, or along watercourses that cannot adequately handle such large flows. Therefore, we see more sewer failures and increased erosion of our natural watercourses, requiring costly repair, maintenance or re-construction, all of which comes from our own pockets via our water bills.
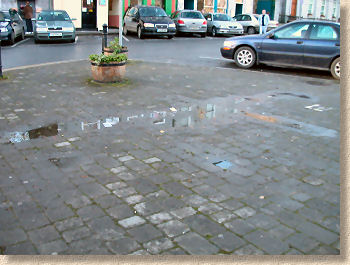
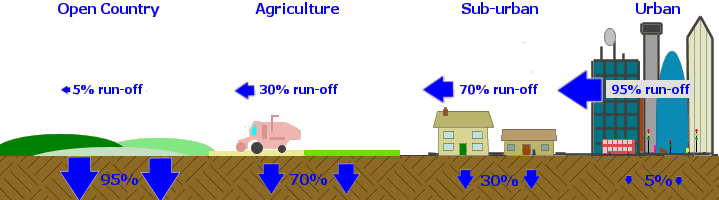
Also, with ever increasing numbers of vehicles and machines being used by society, we see more pollutants, especially hydrocarbons and heavy metals, being released into the environment. With impermeable surfaces, these pollutants are typically carried by run-off water into our sewers and natural watercourses, where they can cause significant and costly damage to treatment plants, or devastate the fauna and flora of our ditches, streams and rivers. Permeable systems enable pollutants to be trapped by the sub-base or by a geo-textile . See below for more details on how pollutants can be more effectively managed by permeable paving systems.
Consequently, many planners, local authorities and developers are now giving serious consideration to the use of permeable paving systems, as they can be more cost-effective than traditional collection and dispersal systems and offer significant environmental advantages, such as natural breakdown of pollutants, replenishment of aquifers, and the possibility of water harvesting.
Types:
From a construction point of view, there are two main types of permeable paving system:
Infiltration - surface water is directed via voids within areas of solid paving
eg: Concrete Block Permeable Paving (CBPP)
Read More about CBPP
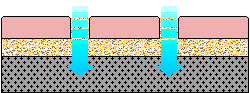
Porous - water is drained directly through the surface
eg: Cellular gravel-filled
paving Permeable Resin Bound surfacing
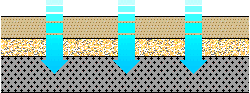
For low-speed traffic areas, such as car parks, an infiltratable concrete block paver system is usually chosen, whereas a grass paving system may be used on non-trafficked areas or those areas subject to occasional trafficking. There are also porous asphalts and macadams now being trialled on urban highways, along with pervious resin-bound surfacings and it should not be forgotten that gravel is the simplest of all permeable surfacings.
Permeable, porous and pervious pavings and surfacings:
- Concrete blocks - now referred to as CBPP (Concrete Block Permeable Paving)
- Clay pavers
- Permeable macadam
- Permeable resin bound aggregate
- Gravel
- Grass pavers/cell matrix Ground Reinforcement
- No-fines concrete
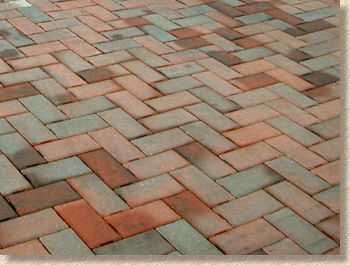
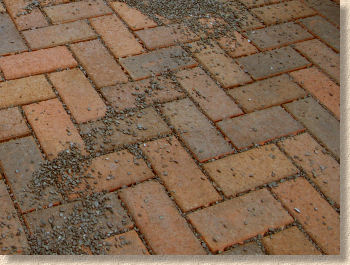
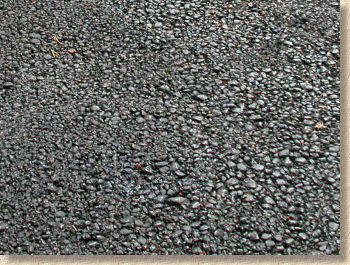
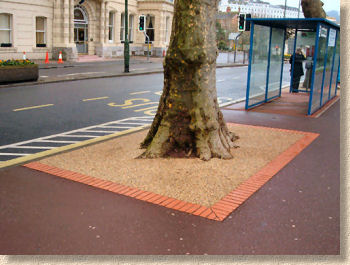
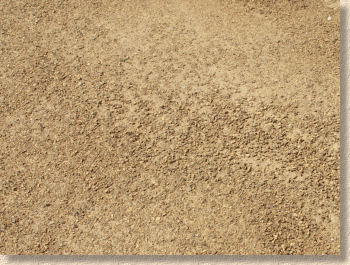
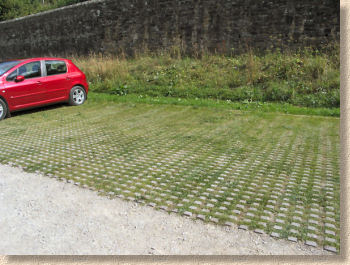
System Designs
Permeable concrete block systems may rely solely on infiltration blocks or use a combination of infiltration blocks with additional drainage, either at the surface or within the sub-base. Small projects of less than 100 m² (depending on sub-grade permeability) can often be managed using 100% infiltration, whereas larger schemes will often need a combined system, with some form of surface water system provided as back-up for periods of exceptional flows.
There are three commonly specified 'systems' used for permeable pavements. These are examined in more detail on the CBPP page.
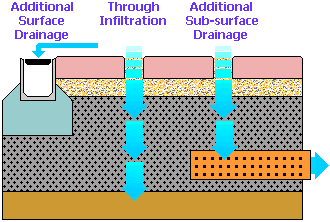
The design standards for permeable pavements are spread through several documents, including BS 7533:3 (2005 ed.) CIRIA's Suds Manual and Interpave's guide to Permeable Pavements. While there are 'generic' designs for smaller pavements, larger system needs to be designed by a competent engineer after a thorough investigation of the site and an assessment of the needs of the project. Fortunately, all the major manufacturers have teams of engineers who are prepared to design a system specific to each project.
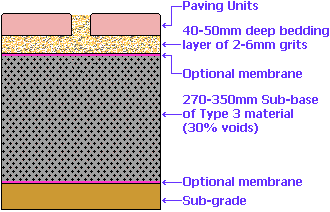
The basic structure of a permeable pavement is not dissimilar from that used for a standard block pavement . The sub-grade is prepared, a sub-base of a specified material is laid, then a laying course consisting of a no-fines granular material, such as 6mm grit, and finally the blocks themselves. There may be one or more geo-textiles incorporated into the structure, depending on the project parameters. With Infiltration Paving, the surface voids are also filled with a no-fines granular material.
Dealing with pollutants
As noted above, geo-textiles or the sub-base can be utilised to 'trap' pollutants and prevent them being carried into sewers and watercourses. For example, a geo-textile laid between the sub-base and the bedding layer can be used to trap any organic matter, which will then decompose in the normal manner, and will also help to 'trap' hydrocarbons and other pollutants before they get into the sub-base.
The use of an impermeable membrane beneath the sub-base will work to contain any pollutants within the sub-base from where they can be directed to the appropriate treatment facility or storage lagoon. The invert level of the discharge pipe can be set according to needs; when set at or near the bottom of the sub-base layer, it will drain all the groundwater; if set nearer the top of the sub-base, it will act as an overflow feature, allowing the sub-base to retain a proportion of the groundwater.
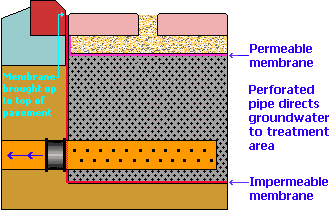
One major advantage of tanked permeable paving systems is that any significant contamination, for example, a diesel spillage, will be restricted to the immediate area and not transported into local sewers or watercourses, making any clean-up operation much easier and less costly to implement.
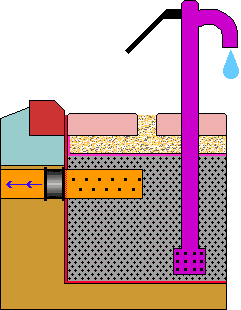
Hydrocarbons can be slowly broken down within the sub-base by natural processes. Alternatively, regular application of oil-digesting microbes over the permeable pavement will accelerate the breakdown process. In heavily trafficked areas, such as car and lorry parks, a designated treatment process should be incorporated within the system, to prevent pollutants building up to unacceptable levels.
Projects where the groundwater and any pollutants are 'corralled' within the system are said to be 'Fully Contained'. Full containment should be designed in to the system where the water table is relatively shallow, or where there is a potential threat to potable water aquifers or other sensitive resources. Fully contained systems can also be used to create storage for later harvesting as 'grey water'.
Maintenance
With Infiltration systems, the top 15-25mm of the voids has a tendency to self-seal with washed-in organic matter, muds and silts. This phenomenon obviously reduces the potential drainage capacity of the system. On the continent, engineers conservatively assume a reduction in the potential drainage capacity of a permeable pavement to around 10% of the theoretical maximum and so, additional run-off drainage is provided to cope with periods of exceptional flow. Longer-term research shows this 10% value to be somewhat pessimistic and although there is a measurable reduction in performance over time, the actual reduction does seem to stabilise in a period of 3-6 years to a value between 10 and 20%.
Regular jet-washing of infiltratable systems can be used to keep joints and voids clear, but is an expensive and labour intensive operation, so designs tend to assume that silting and reduction in capability will take place over time.
Porous systems may depend on periodic jetting or brushing to unclog blocked pores and so maintain system performance. The required frequency of jet-washing will be determined by local conditions. It has been shown that regular jetting can unclog around 80% of the original voids within the porous structure.