
I have received several quotes for a block paved drive all within £100 of each other. I was wondering if you could tell me if you recommend geotextile membranes between the sub base and sand course. Contractors who do not use the membrane say it can cause problems later and is not necessary but the ones who do, say it is beneficial.
The Why...
Some contractors are suggesting or even recommending that residential driveways and even patios should incorporate a "membrane" for best results. Unfortunately, quite a few of the contractors recommending the inclusion of a membrane seem to be unsure as to the benefit it brings to the finished pavement. Some claim it is a weed-proofing measure, while others claim it helps reduce the amount of sub-base required, and yet others claim it can eliminate the need for a sub-base completely. We've also heard claims that it prevents the settling of bedding sand and even that it prevents flooding!
Several of these claims are spurious, to say the least, and some of them are pure fantasy. The true purpose of a geo-textile used in the construction of a typical block pavement is explained on the Geo-sheets page , but, to summarise, its primary purpose is as a separation membrane , preventing the sub-base or bedding material mixing with the underlying layers, which can result in excess settlement or pumping of a particularly weak sub-grade, which, in turn, can cause settlement and rutting.
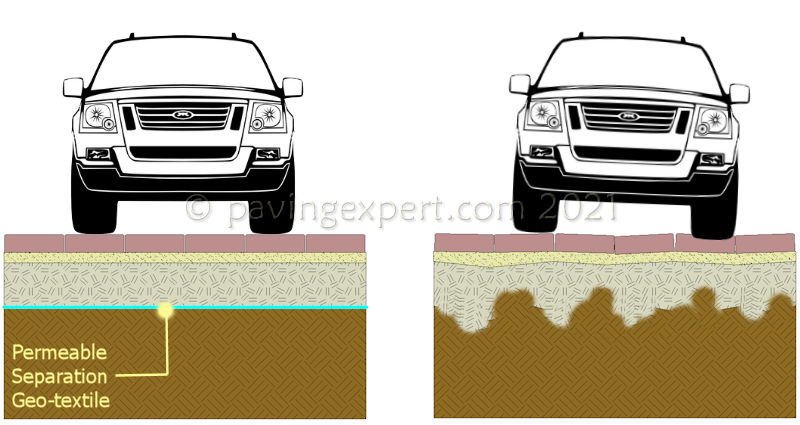
The What...
There have also been some reports of less-than competent contractors and some misguided diy'ers using 'plastic' or polythene sheeting as a separation membrane within a pavement. This usually turns out to be some form of building film, protective sheeting or a damp proof membrane. One correspondent asked if he could use 'Bubble Wrap' misappropriated from his place of work as he could not find a local supplier of a genuine separation membrane!
An impermeable film or membrane will cause all sorts of problems with most types of paving. It will prevent proper drainage of the overlying layers, which can cause saturation of the bedding layer and all the headaches that come with that, such as pumping, settlement and channelisation. Only a genuine separation membrane should be used - not a " landscape fabric ", not a damp proof membrane, not a layer of polythene, and certainly not a roll of bubble-wrap!
Links to manufacturers of quality geo-textiles are given on the Geo-fabrics page.
The Where...
There also seems to be some confusion and disagreement as to just where a membrane should be placed within the pavement structure, with some contractors claiming it should be placed on top of the sub-base, between the "hardcore" and the sand bedding, and others insisting it should be placed between the sub-grade and the sub-base.
The reasoning behind the 'sub-base:bedding' school of thought is that the membrane prevents the bedding from trickling down or being washed into any voids within the sub-base material, while the 'sub-grade:sub-base' orthodoxy, in which I include myself, maintains that keeping the sub-base material from mixing with the sub-grade, and reducing or eliminating any risk of pumping (see above) is more relevant.
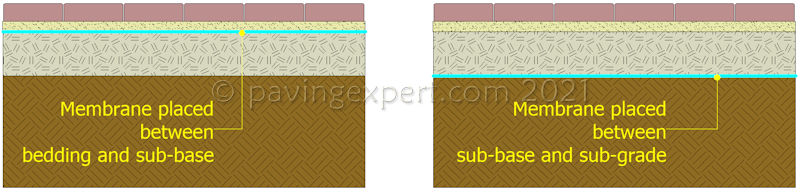
In the vast majority of light-use constructions (patios, driveways, footpaths, etc) there is absolutely no need for a membrane to be placed between sub-base and the bedding layer: it achieves almost nothing, as a well-selected sub-base material will have what we call a 'tight' or 'close' finish, that is, there will be very few, if any, significant voids. Further: when constructing a sub-base, the good contractor will 'blind' the surface with fines or grit sand to ensure that there are no nasty voids that could gobble up the bedding material.
There are projects where a separation membrane between the sub-base and bedding would be justified. These are often special applications, such as permeable paving, where the sub-base is purposely open in texture to aid drainage, and so a cogent argument could be made to include separation membranes at both interfaces, which would, no doubt, delight the membrane manufacturers, but, if a membrane is to be used, then it should be placed on top of the excavated sub-grade, between the bare earth (or capping layer) and the sub-base.
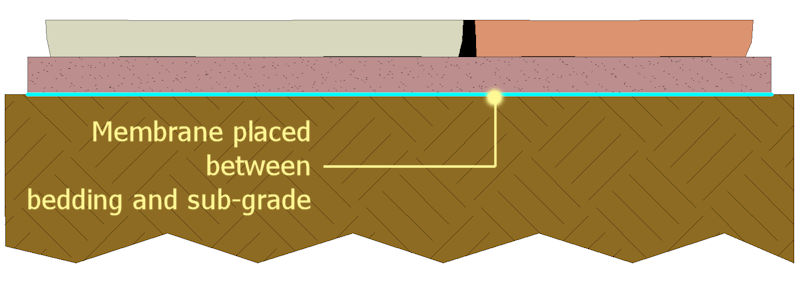
Obviously, where no sub-base is present, as is often the case with flagged patios and domestic footpaths, then if a membrane is to be used at all, it should be positioned between the sub-grade and the bedding.
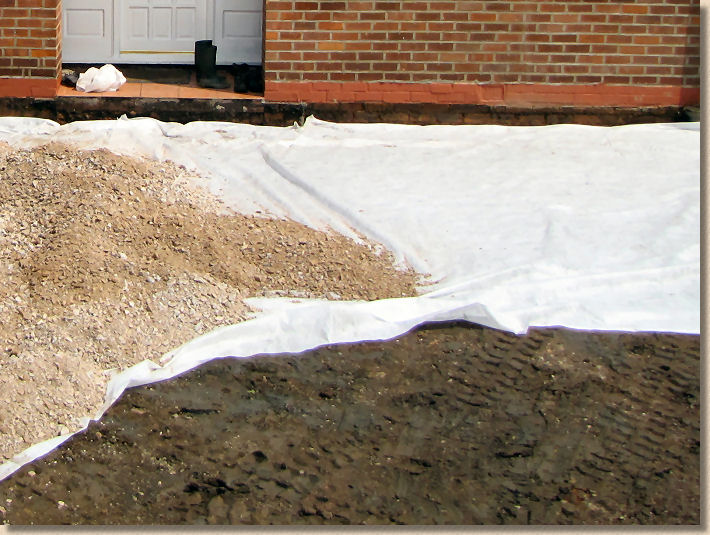
The Facts...
So, what about the claims made for the inclusion of membranes within residential paving jobs? Taking the 'claims' quoted above one at a time...
The Claim:
A membrane reduces or minimises or eliminates weeds
Degree of Veracity:
Piffle
Reasoning:
Other than the really pernicious, nuclear-bomb proof weeds such as Japanese Knot Weed (Fallopia japonica) and Mares' Tails [Equisetum spp.], the vast majority of weeds will not grow through a properly constructed pavement as described on the introductory Block Paving page. Consider said block paving: there's 200mm or more of heavily compacted, weed-unfriendly material between the sub-grade and the surface, and your average dandelion or daisy does not stand a chance of getting through that lot, whether there's a weed membrane there or not. Even with a well-laid patio, with concrete flags laid over a cement-bound bedding material of the type recommended elsewhere , there is little or no chance of the average weed forcing its way through.
However, weeds will settle onto the surface of a completed pavement and grow into the joints, and no weed membrane can stop that, regardless of where it's positioned, beneath the bedding layer or beneath the sub-base (if one is used). The only way to prevent weeds colonising the surface of an elemental pavement is to ensure the joints are intact and impenetrable, either by using a bound jointing material (such as mortar ) or by applying a sealant that closes off the joint from the outside world.
Conclusions:
Ignore, unless there is a known threat from pernicious weeds
The Claim:
A membrane reduces the amount of sub-base material required
Degree of Veracity:
Yes but....
Reasoning:
A membrane can, indeed, help reduce the amount of sub-base material required in those situations where more than a single, 225mm layer might be needed. In fact, there are numerous case studies published by the membrane manufacturers that make much of this benefit, as it offers significant cost savings to the contractors, not just in terms of sub-base material imported to site and compacted, but also in terms of reduced excavation volumes.
However, a typical residential driveway will have a sub-base of only 100-150mm thickness and any reduction to less than 100mm results in a sub-base with no inherent strength: at less than 100mm thickness, there isn't enough substance to form a coherent layer that is capable of carrying loads. Admittedly, where the sub-grade is suspect in some way, a membrane can be a great advantage in that it strengthens the construction and could, possibly allow a 100mm thick sub-base top be used in place of a 150mm layer, but, for 90% or more of what we term 'light-use pavements', there is no great saving to be made.
Conclusions:
Not feasible on a typical driveway.
The Claim:
A membrane eliminates the need for a sub-base
Degree of Veracity:
Tosh
Reasoning:
While a membrane can increase the competence and long-term performance of a reduced thickness sub-base, as described above, it cannot replace a sub-base completely. The improvements in performance that come with a membrane depend partly on the load-distributing and separating properties of the membrane, combined with the load-distributing properties of the sub-base material itself. Omit the sub-base material and you're left with a sheet of non-woven flexible material lying on bare earth and covered with a scattering of sand - how is that supposed to carry the weight of a pavement and its traffic?
Conclusions:
Unless the sub-grade has a high CBR and can be accurately formed to level, then a membrane can never replace a sub-base.
The Claim:
A membrane prevents bedding sand settling
Degree of Veracity:
True but irrelevant
Reasoning:
Because the membrane acts as a separation barrier and its pore size is far smaller than the grains of sand in the bedding layer, the use of a membrane would prevent the bedding sand from settling into a sub-base, but if the sub-base was to be constructed using properly graded material, preferably Type 1, and prepared with a 'tight' finish (that is, with no obvious voids in the surface layer) then there is no place for the bedding sand to settle. If a sub-base appears to be open-textured on compaction, then additional fines or bedding sand can be used at that stage to 'tighten up' the upper surface, vibrating in the finer material to fill all voids and thereby reduce or eliminate the risk of excessive settlement of the bedding material on completion.
Conclusions:
Not really applicable for light-use residential paving projects.
The Claim:
A membrane prevents flooding
Degree of Veracity:
Total obllocks
Reasoning:
I'm not sure how this is supposed to work. Perhaps the contractors making this claim are confusing a separation membrane with a horizontal drainage composite but there is no way on this earth that a permeable, flexible sheet of non-woven material can prevent flooding.
Conclusions:
Cowboy Alert!
The Last Word...
- For the vast majority of light-use paving in Britain and Ireland, a membrane is not required.
- The inclusion of a separation membrane within a light-use pavement can be beneficial, but it is not a replacement for good practice or proper construction, and it is not carte blanche to skimp on sub-base materials.
- It is a low cost addition that will not detract from the construction, but neither will it safeguard against poor workmanship or shoddy materials.
- If a membrane is to be used, then only genuine geo-textiles, labelled as such and described as suitable for use as a separation membrane should be installed.
- Polythene is NOT suitable!