Introduction:
Unless you are blessed with an infallible eye for geometry , or have a completely modular design, there will come a point when a flag or block needs to be cut, or trimmed, to fit in a particular position. Different materials are cut by different methods. Three of the most common tools are described here; hammer and chisel, power saws and block splitters. The power saw has become a standard tool in the paving industry over the last 30 years, and the traditional skills of cutting with hand tools are being lost and becoming almost mythical. As a young child in the 1960's, I would watch and marvel as my Father cut a perfect rectangle from the centre of a flag , to fit around a stop-tap box in a footpath, with only three different chisels, a lump hammer, and a professional hand and eye.
While this page looks at the more popular tools used to cut and shape various paving materials, separate pages deal with the techniques involved in cutting flagstones and block pavers , and further pages consider techniques such as Mitre Cuts and Cutting Notches .
From May 2008, the Health & Safety Executive has issued new recommendations for using power saws when cutting concrete paving. These recommendations are fully supported by pavingexpert.com. In essence, the advice is that cutting should be avoided whenever possible but, when there is no viable alternative, dust suppression (usually by water) MUST be used. The launch of the revised advice is covered more fully on this news page and the promoitional DVD issued with the advice can be viewed below .
With all cutting operations involving concrete, bricks or stone, there is a real danger of injury from flying scalpings. ALWAYS wear protective goggles/glasses, and when cutting with a power saw wear a dust mask and use water suppression. Power saws are lethal in the wrong hands. Don't take chances!
Which is best?
Each of the different cutting techniques has advantages and disadvantages, and certain techniques work better with some paving types than with others. This key points are summarised in Table 1, below.
Type of Paving
Hand Tools
Power Saws
Splitters
Pressed concrete flags
Can look less than tidy
Fast, neat cuts. Some cuts may still need to be hand trimmed
Dust MUST be suppressed - See this page
Only really suitable for small element paving. Thicker units (>65mm) may need a hydraulic splitter
Wet Cast Flags
Tends to be unsuccessful due to the material characteristics of the units
Fast, neat cuts. Some cuts will still need to be hand trimmed
Dust MUST be suppressed - see this page

Not usually suitable for the same reasons as given for hand tools
Natural Stone
Usually fine, but can be strenuous with harder stone. Gives a traditional quarry-fettled look

Fast and neat - can look out of place with reclaimed materials where a hand-tooled finish looks more natural
Consider Fettling
Dust MUST be suppressed
Ok, depending on size and type of stone.
Hydraulic splitters may be needed on harder/thicker stones
Concrete Block Pavers
Ok, but splitters are faster
Simple, fast, accurate and fairly clean
Clay Pavers
Ok, but splitters are faster
Fast, neat cuts, but a lot of dust is generated, so use suppression . Table mounted saws with a diamond blade and a water source are preferred
Simple, fast, accurate and fairly clean. Specialist clay splitters available
Hand Tools - Hammer and Chisels
The chisel we traditionally use to split or cut into a stone or concrete paver is known as a Pitching Chisel or Pitcher. These are rare nowadays, and are not worth hunting down unless you intend to take up streetmasonry as a career. Most manufactured materials can be split with a 75mm bolster chisel and trimmed, if necessary, with a cold chisel.
The preferred hammer is a lump hammer, with a head weighing around 1Kg (2.2 lbs). There are special masons' hammers, goat's head hammers, brick hammers and umpteen other types that could also be used, but, for all-round use, a lump hammer is the most commonly used tool.
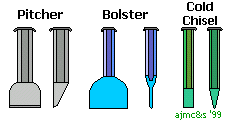
Power Saws
Paving saws now have their own page where the various types used in the industry are examined in more detail.
There is a variety of powered saws used for cutting pavings and pavements in the construction industry. Bench or Table Saws are favoured for cutting large numbers of clay bricks and masonry units on site, and Floor Saws are used to cut control joints or trench edges in concrete, tarmac, and asphalt surfaces, but the most commonly-used tool by far is the hand-held cut-off saw, also known as a Stihl Saw, Skill Saw, Con Saw, Disc Cutter, Whizzer and umpteen other local/regional names. Only this type of saw will be considered in this section.
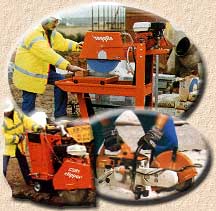
These tools have become an essential item for most groundworking trades since their introduction 30 or so years ago. Not only are they used to cut paving materials, they are used to cut clayware pipes, bricks, blocks, lintels, kerbs, reinforcing steel, asphalt and just about any other hard material used in the construction industry.
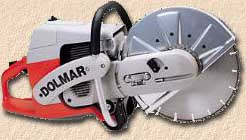
There are petrol-engined models and electrically powered models, although the latter tend to be used on sites where electricity supply is not an issue, rather than general use by contractors who cannot guarantee an electricity supply on their next job. The electric models are very similar to large angle grinders.
However, it is the size and type of blade that determines how effective a power saw will be. Most of the saws used by Contractors will have a 230mm or 300mm diameter blade, with a typical speed of 3,000-7,5000 rpm. There are 3 common groups of blade types; abrasive for cutting stone/concrete, abrasive for cutting steel/metal, and diamond tipped, normally used for cutting stone/concrete. Obviously, there are different 'grades' or qualities within each of these groups, and the diamond blades are usually further classified as 'wet cut' (the blade is continually cooled and the dust dampened by a stream of water) or 'dry cut'.
Most Paving Contractors will rely on a diamond-tipped blade , because they offer a longer working life and, more importantly, a constant depth of cut. A normal abrasive blade wears as it cuts, so, for example, a 300mm diameter blade capable of cutting to 100mm depth when new will only be capable of 'nicking' a paver after a dozen or so cuts, because the blade diameter will have been reduced to, say, 130mm, giving a maximum cutting depth of 25-30mm.
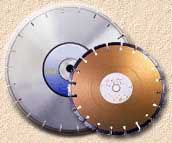
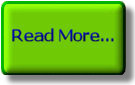
For those using a power saw to cut paving materials, there is a separate page which looks at what needs to be considered when choosing a diamond blade
Petrol-engined power saws can be hired from hire centres at approx. £20 per day. A 230mm or 300mm blade is best for cutting paving materials; the smaller diameter blades used on Angle Grinders are not really suitable. If you have a lot of cutting work to do, leave it until the end of the project, hire a saw for just one day, and do all the cutting in one session. Tell the hire centre exactly what type of material you will be cutting - there are different blades for different materials.
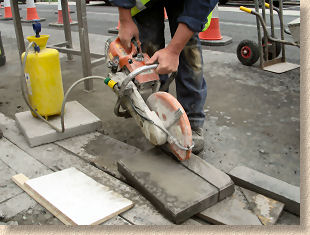
From May 2008, the HSE in Britain requires all cutting of concrete paving materials (so that's blocks, flags and kerbs) to be avoided whenever possible and to use dust suppression when there is no viable alternative.
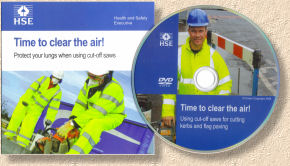
Available on request from HSE
Limited numbers available
Time to clear the air! - promotional film
For most contractors, this will involve the use of a water source to suppress the dust, to prevent it becoming airborne and being inhaled, doing untold damage to the lungs. Water suppression equipment is readily available at most Hire Shops.
Block and Slab Splitters
For ease of us when it comes to cutting paving materials, first place must surely go to these cracking little machines, the block and slab splitters. They are simple to use, require only the most rudimentary of training to use, have no lethal moving parts, generate virtually no dust, are a doddle to maintain and can be used on a wide variety of paving types.
They come in a range of sizes, with different models offering different cutting-widths capable of handling materials from brick size up to flagstones, and various jaw-opening sizes for units ranging from 25mm up to and beyond 200mm.
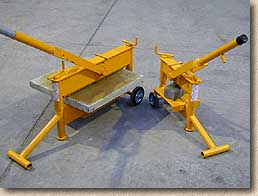
These handy little machines are also available at hire centres, starting at around £25 for a day, although all good contractors will have at least one machine, if not two or more, to suit various materials and unit sizes.
There are three basic types:
- manually operated for smooth/regular pavers
- manually operated with individual toothed blades for pavers with irregular surfaces
- hydraulic - for the big, awkward stuff, such as thick stone paving
All three types work on the same principle of 'squeezing' a paver between an upper and a lower blade and exerting such force than the paver 'snaps' along the line of the blades. Hopefully. Most of the time.
The most commonly used machine, and the type most often stocked by Hire Centres, is the manually operated model for regular pavers. This has two simple toughened steel blades, top and bottom, which are often 3-side or 4-sided in cross-section, and usually they can be rotated to give a longer blade life. The snapping force is generated by a lever, often with an extended arm to generate extra force, operation on a cam or other device to move the top blade down compressing the paver in the process.
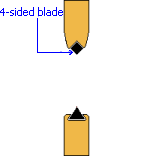
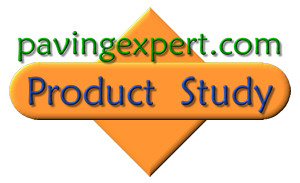
There is a separate page which examines the use of block splitters in much greater detail, and follows their use on a range of cutting-in jobs using various paving materials.
While the simple blade type described above is adequate for smooth or regular pavers, some materials, notably clay pavers and some types of riven stone, have an irregular surface that precludes the use of a simple blade, as the blade would only be in contact with the 'high points' on the surface/base of the irregular paver, and therefore the compressing force would not be evenly distributed through the paver, which usually results in it fracturing in the wrong place.
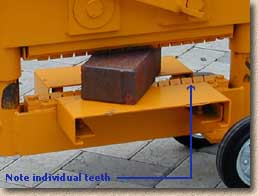
To counter this, there are machines that feature blades composed of a number of individual spring mounted teeth that can accommodate the variation in the surface of the paver and ensure a neat and accurate cut. The most popular machine with this feature is the AL33S manufactured by Probst and shown opposite.
This type of machine allows each 'tooth' of the blade to find 'best contact' with the surface of the paver being cut as the jaws gradually close, so that an accurate cut is far more likely when full pressure is applied.
The final type of machine is the hydraulically operated version. This type is normally used on thicker or tougher pavers and stone that defeat the brute force of the average streetmason. Rather than rely on the operative bouncing up and down on the end of a long lever to generate sufficient force to snap the paver, a hydraulic ram is employed to gradually build up the pressure on the paver.
On site models, the hydraulic ram is usually some form of 'bottle jack' that is pumped up by a short lever, but the larger, industrial models run on an electrically-pumped hydraulic system capable of generating HUGE forces. At the largest scale, variations of this type of machine are used in the manufacture of items such as split-faced walling, stone setts etc.
This type of splitter is much slower than the manually operated types, and therefore its use is limited to essential situations.
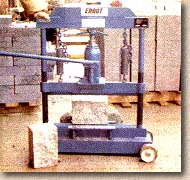
If you elect to hire a splitter, the Hire Centre will give you full instruction on the safe use and operation of the type of splitter appropriate to your requirements.
The principles involved with all splitters are quite simple. Mark the cut with the edge of a small piece of slate, or steel nail, remembering to allow 3-6mm for joint width. Place the paving unit between the jaws of the splitter, in such a position that the top blade of the splitter is on the line of cut.
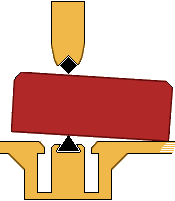
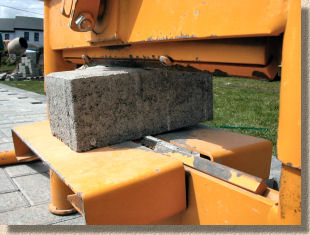
Angling the brick or flag in the splitter will create an undercut, making fitting much easier, and most models feature some form of supporting shelf to help support the paver at a slight angle during the alignment and cutting procedure.
Pull down the operating lever, and the force of the blades should split the unit along the right line. Some pavers are quite tough and may need considerable force to split them. For this reason many manually operated splitters feature a telescopic lever to help generate extra force.
Beware of the offcuts from the splitter dropping heavily to the ground and breaking. Make sure they are supported. An old rug or piece of foam rubber can lessen the impact and reduce breakages. Edges that are slightly oversize can be trimmed with a bolster or a cold chisel.
See also Block Cutting Page
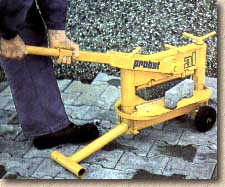
Related Pages:
- Saws used in the Paving industry
- Tools & Suitability
- Using a block splitter
- Cutting Flagstones - The Basics
- - Cutting Curves
- - Inboard Cuts
- - Cutting Notches
- - Cutting a Ring Radius
- - Cutting a Fan Radius
- - Run-outs and Town Corners
- Using Hand Tools
- Diamond Blades
- Cutting-in Block Paving
- Cutting Mitres