Introduction:
Resin mortars are given extensive coverage on other pages within this website, while Polymeric Sand and Modified Mortars are considered below with additional information provided on separate pages linked throughout the text.
The preceding page of this section looks a standard mortar pointing , along with wet grouting , dry grouting and dry sand jointing . The following page looks at some of the other materials that may be used to joint paving.
Polymeric Jointing Compounds
This category of jointing materials has been developed over recent years to satisfy a demand for a fast, clean and simple method of sealing the joints of various types of paving, particulary those types with joints of 10mm or more, such as flags , setts, cubes , cobbles , etc.
They generally work by means of a polymer resin that cures in 2-24 hours when exposed to the atmosphere, binding together the individual grains of sand rather than by bonding to the paving itself, creating a firm, stable joint that is resistant to scour, street-cleaning equipment and general traffic.
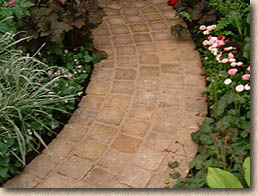
They are supplied as a dry brush-in type product, often vacuum-packed and having the selected sands pre-mixed with the polymer binding agent. The sealing work is best done on a dry day. The surface of the pavement should be swept clean before the product is scattered over the surface and directed into the joints by means of a soft brush. The working life is fairly generous, at 2 hours minimum, but it is essential that the polymer sand is kept free from dust and other detritus during the jointing work.
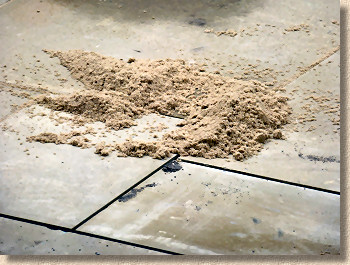
Some unscrupulous contractors or naive diy'ers have been known to 'thin' the polymer sands by mixing in a trowelful or two of kiln dried block jointing sand - this is bad practice and will result in sub-standard joints of inferior strength.
The product can be compressed with the edge of a trowel and topped up before being tooled with a pointing bar, although the manufacturers claim this is not always essential. There is no need to wet the joints once filled, and they can be trafficked more or less immediately.
These products are becoming increasingly popular despite the relatively high purchase cost because they...
- reduce the need for skilled labour to joint/seal a pavement
- reduce the incidence of staining and subsequent time required for cleaning
- can be used to joint/seal a given area of paving in considerably less time than traditional methods
Other benefits include...
- Permeability to water and gases, allowing sub-layers and tree roots etc. to receive adequate water and ventilation
- Resistance to weeds (albeit negligible compared to mortar or pitch)
- Resistant to 'mining' by ants and other invertebrates
- Inert once cured
- Non-polluting once in place (although no information is given about the environmental impact of manufacture and distribution)
The width and depth of the joint will determine the most effective use of these polymeric sands. For joints of 3-8mm, most contractors would opt to fill the entire joint with the polymeric material. However, because of the high cost of these products, joints of 9mm and above will often be partially filled with a cheaper material, such as grit or a small gravel, and then topped with the polymeric sand.
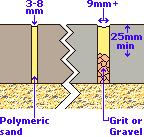
Coverage
Coverage, obviously, varies with joint width and joint depth, but, as a general guide we work with the following coverage rates...
|
Non-bonding Polymerics
Several brands of polymer sand do not bond to the paving, and so remedial works become much simpler because the paving units are comparatively easy to remove and simple to clean. Traditional mortar or pitch jointing often needs to have the jointing material sawn out or broken with a hammer and bolster before the paving units can be lifted, and then it can be all but impossible to clean the jointing material from the base and edges of the units prior to re-laying.
However, this lack of bond between jointing and paving can also mean that smaller units with wide joints (e.g. setts and cubes) that are subjected to significant turning forces and/or shear stresses, can eventually work loose, especially if the joint filling material beneath the polymeric sand is loose or less than perfect. In the photo opposite, the polymer jointing material has been cracked and forced loose by repeated trafficking, and mosses have started to colonise the surface.
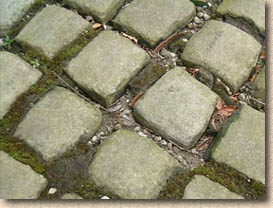
We are reluctant to recommend this non-bonding type of jointing for wide joints subjected to significant shearing forces - we have found that, because there is no bonding to the setts/cubes, the polymeric sand is gradually worked loose and the pavement loses its surface integrity, as can be seen opposite.
If the setts/cubes have their joints packed with a cement-bound material after laying (rather than a grit or gravel), and the non-bonding polymeric product is used simply as a 'topping', then there does seem to be a lesser incidence of joint and pavement failure. We believe this to be because the cement-bound jointing material is providing adequate structural strength, but we have observed that a 20-25mm 'topping' of a polymer sand when used in this sort of construction still has a tendency to work loose, and for this reason we are reluctant to consider its use on any joint greater than 10mm or with setts/cubes other than those with sawn edges.
Polymeric or Pitch?
In the photos below, a step had been built using reclaimed sandstone setts and then had its joints sealed with a non-bonding polymeric sand. As can be seen, where the porch above the main doorway shelters the step, the jointing remains light-coloured, clean and weed-free, but near the front edge of the step, where it is more exposed to the elements, the mosses have managed to establish a presence, and the jointing is considerably darker. This work, done by an unknown contractor is just two years old.
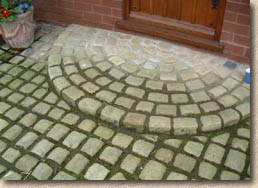
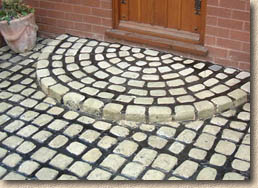
Compare with the second photo, which shows the step after the non-bonding polymeric jointing was removed and replaced with traditional pitch. The colour is uniform, and will remain so, regardless of weather and degree of shelter. The contrast between the jet-black pitch and the light colouring of the stone setts, ensure that the nature of the stone is emphasised.
For more about sealing with pitch, refer to the Sett Jointing page.
Full-bonding Polymerics
A second class of polymeric jointing compounds has emerged, and the key difference with these products is that they do actually bond to the paving and so effect a much more competent joint that becomes an integral part of the pavement structure. These products offer all the benefits of their non-bonding cousins, such as ease of use and cleanliness of installation, but the very best of them are also suitable for use on commercial projects as the strength of the jointing material, and that of the bond between jointing and paving, is sufficiently strong to withstand and support vehicles of varying sizes and volumes.
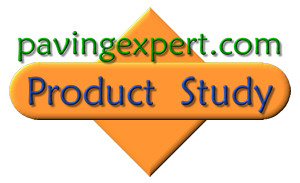
Economies of scale and technological developments have now made it possible for these fully-bonding polymeric products to be available at the same (or very similar) prices as those for the inferior non-bonding products. Pavingexpert Product Studies of some the leading products in this group can be read by following these links....
Conclusions
Polymeric sands have their uses within the paving industry, but, because of their relatively high cost in the Britain and Ireland, they have usually been difficult to justify on 'typical' projects unless there was a specific reason for using them, such as scour, or mining by ants. They are useful for diy'ers looking to joint a patio in a simple, straightforward, low-skill manner, while avoiding the problems of mortar staining or wash-out/scour of dry sand joints.
The manufacturers claim that the high cost of the material (around £2+VAT per Kg in 2016) is often offset by the reduction in labour required to joint a given area.
They are a handy addition to the armoury of jointing products available to the paving contractor, but the cost factor means they will probably maintain a small market share for some years to come. If costs could be significantly reduced, and their existence was more widely known amongst the Trade, then they could (and possibly should ) become much more widely used.
Modified Mortars
A further specialist mortar for paving are the Modified Mortars that can be pumped or poured into the paving joints. Modified mortars are those products which incorporate small amounts of special additives to improve the workability or performance of the mortar compared to a standard Sand and Cement type mortar.
The Modified Mortars for Jointing Paving are generally a standard mortar (ie, sand and cement) with special thixotropic additives that make the mortar more workable and increase compressive and/or flexural strength. The mortar is prepared to a suitable consistency that enables it to be applied via a pump, much like a mastic gun, or to be poured into wider joints.
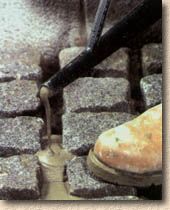
Easipoint Ltd.
The pourable mortars are great for wide joints of 10mm or more on reasonably level sites and on the right jobs, they can be a real godsend, but we find that the pumped mortars are less useful to us, mainly because of the relatively slow speed of application and the time spent recharging the pump cartridge with fresh mortar.
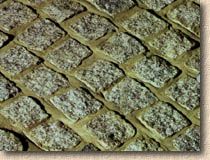
They are very useful products for those projects that need to be opened to the public as soon as possible, as the rapid curing means the pavement can be firm enough to take foot traffic in as little as two hours. They help ensure that a mortar is of a minimum strength, something that is not always the case with site-mixed mortars, and they are available in a limited range of basic colours such as brown, browny buff, browny black, and browny red.
Naturally, this fast setting and workability doesn't come particularly cheap and so it's important to weigh up whether the ease of use, high strength, and fast setting are worth the extra cost.
There's much more information regarding modified and proprietary cement mortars on the following pages....
Associated Pages
Jointing Stone Pavements
- Introduction
- Terms & definitions
- Pointing Styles
- Spacers for Paving
- Cement Mortars
- - Hand Pointing
- - Pointing Riven Flagstones Using Coloured Mortar: A Case Study
- - Wet Grouting
- - Dry Grouting
- - Slurry Grouting
- - Gun Grouting
- - Poured Grouting
- Resin Mortars
- - Polymerics
- - GftK Polymerics: A Product Study - VDW 840+
- - Romex Polymeric Mortars: A Product Study
- - Jointex Polymeric Mortar: A Product Study
- - Slurries
- - GftK Slurry Mortars: A Product Study - VDW 800 Permeable
- - GftK Slurry Mortars: A Product Study - VDW 850
- Re-jointing paving
- Pitch Jointing
- Loose Fill Jointing
- - Stabilisation
- Alternative Jointing Materials