Introduction:
Many different materials and products are used to construct edgings, and each will have their own pros and cons. Many edgings are modular, being put together from component parts that may be individual pavings in their own right, such as block paver edge courses, or dedicated elements manufactured specifically for use as an edging. The most well-known is, unsurprisingly, pre-cast concrete edging kerbs, but these have their limitations, moistly to do with mass, the need for large quantities of supporting concrete, and difficulties forming curves, but one of the most versatile manufactured, dedicated edging systems is a steel system, such as those provided by Core Landscaping Products .
This page will look at what such edgings have to offer, what advantages they bring to a hard-landscaping project, and how they should be constructed for a variety of projects.
Why Use Steel?
With so many alternative materials available for the construction of edgings or edge restraints, why should a streel system be considered?
- Flexibility – lovely sweet curves with no ‘threepenny bit’ knuckles
- Durability – tough, resilient and long-lasting. Core LP offer a 25 year guarantee
- Discretion – barely noticeable when installed
- Decorative finishes – for when you do want the edging to be seen
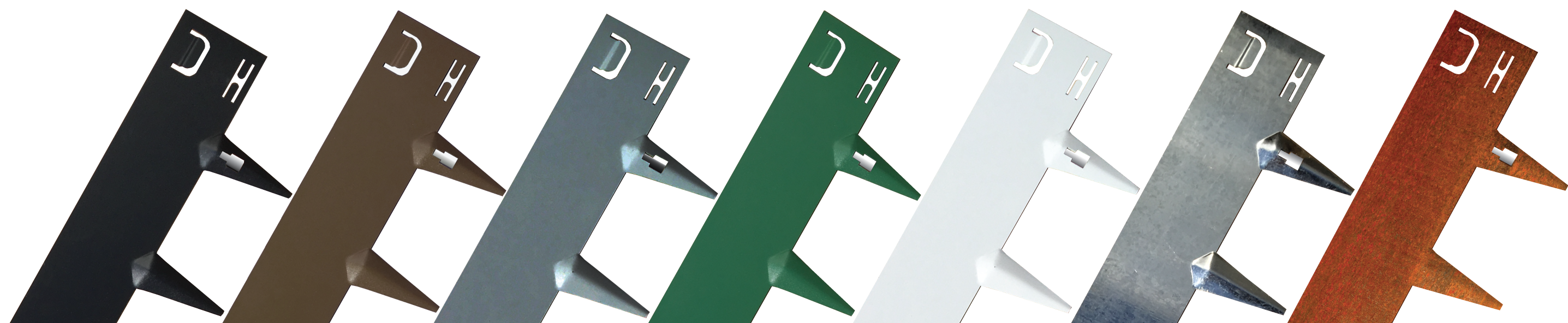
Core Edge colour range
Products Available:
Core LP offer three key ranges of edgings, in a variety of colours and finishes, one of which should be suitable for almost any project. There is also a full range of accessories that will ease installation and enhance performance.
All edgings are manufactured from flexible mild steel
The three ranges are:
Standard Domestic Range
- 1.6mm standard thickness
- 1075mm standard length
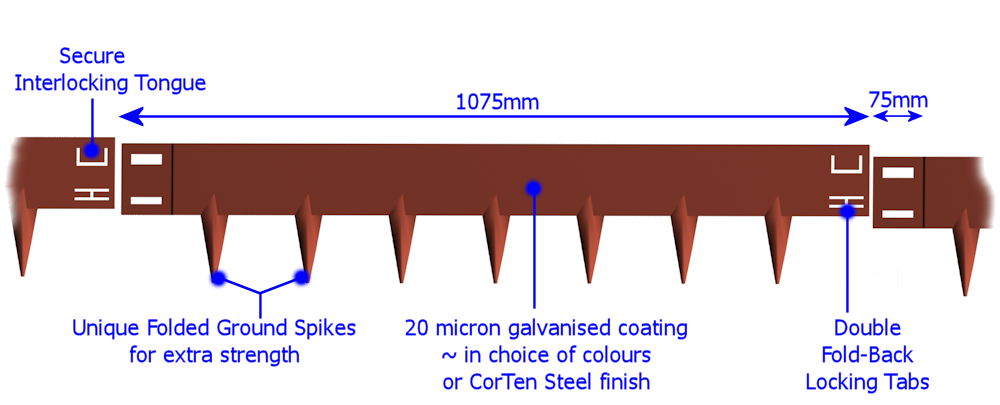
Heavy Duty Trade Range
- 2.5mm heavy duty thickness
- Two standard lengths – 1075mm and 2275mm
Both Standard and HD come in 3 face sizes (65, 100, and 150mm) with complementary spike depths (85, 95 and 115mm)
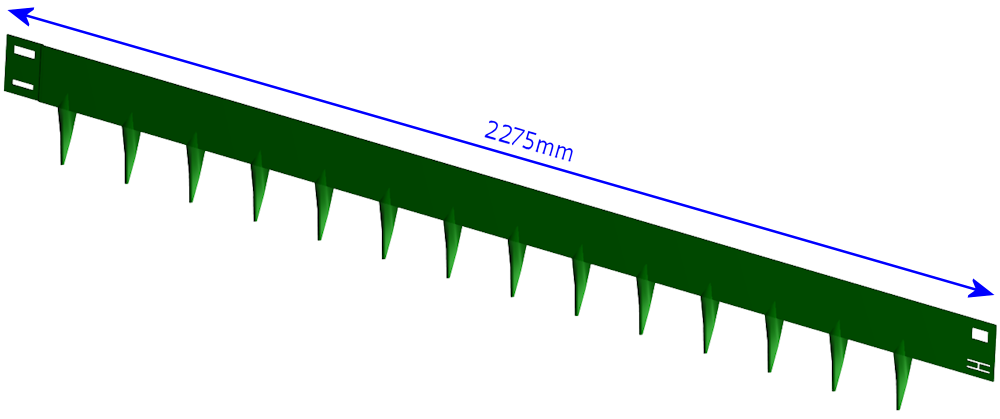
Tree Ring Range (circular)
- Three diameters available – 600/900/1,200mm
- All have 65mm face and 85mm spike
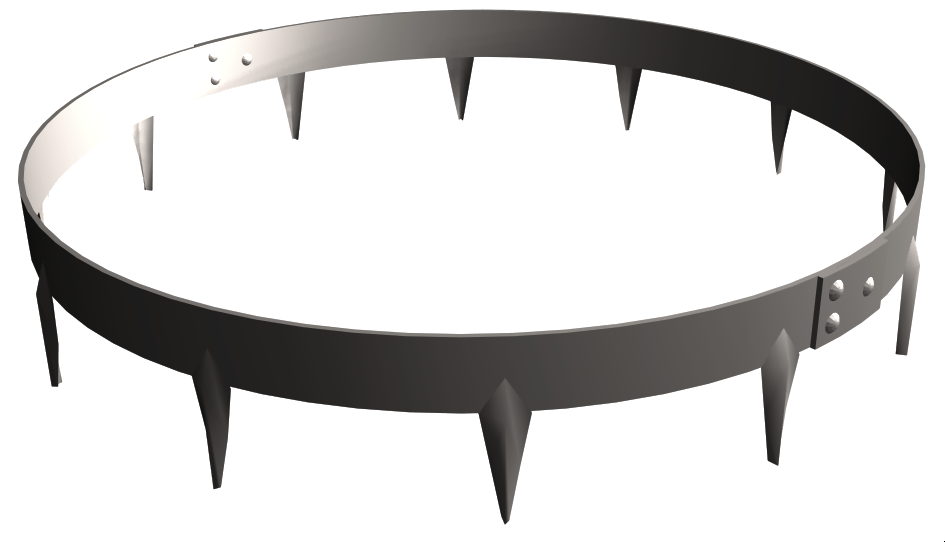
Construction:
There are two principle methods of construction using Core Edge:
- Direct to Ground
- Concrete Bedded
The specific requirements of the site and the proposed usage of the edging will usually determine which method will be more suitable.
Direct To Ground
Where the sub-grade is soil or clay, and the intended use is as a retainer for a surface or material that is loose, unbound or self-supporting, then the Core Edge system can be directly fixed into the ground. This is the method typically used when the edging is intended to retain, say, a lawn, a raised bed of topsoil, a loose gravel pathway, or a pedestrian cell paver system. There are many other possible applications where Core Edge would be eminently suitable laid direct to ground, but should there be any uncertainty, Core LP HQ would be more than happy to advise.
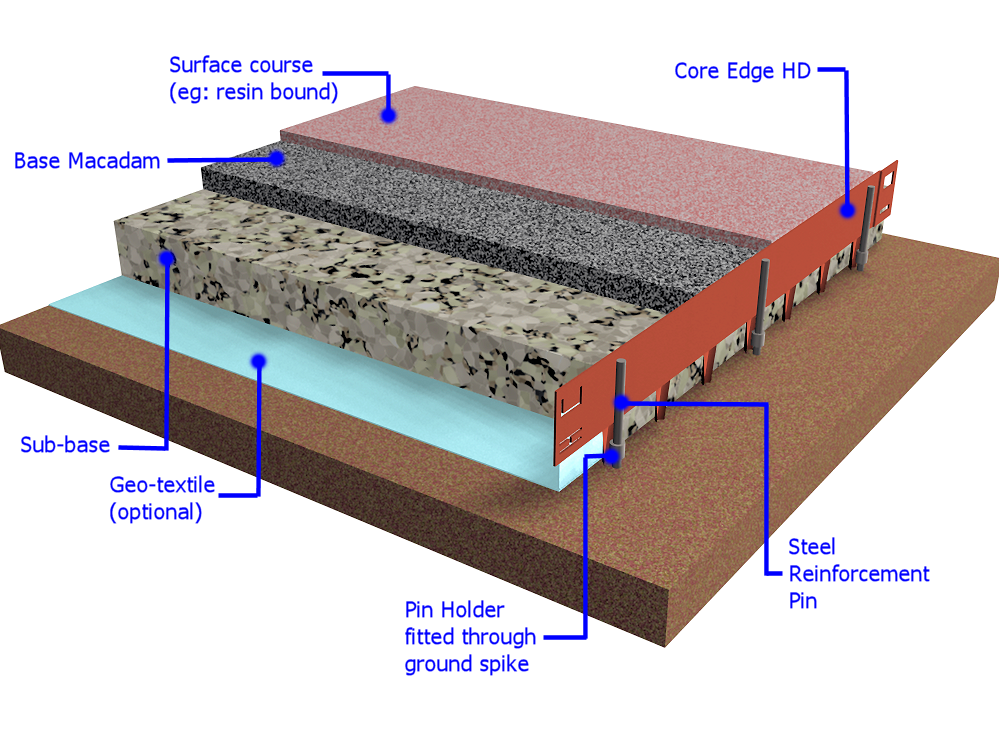
For Direct to Ground installations where additional support may be required, Core Edge can be fitted with supporting pins, 300mm steel stakes that are quickly and easily fitted to the edging using a special clip that attaches to a pre-formed hole that is provided in every third ground spike.
The support pins may also be used with Concrete Bedded installations, if deemed necessary.
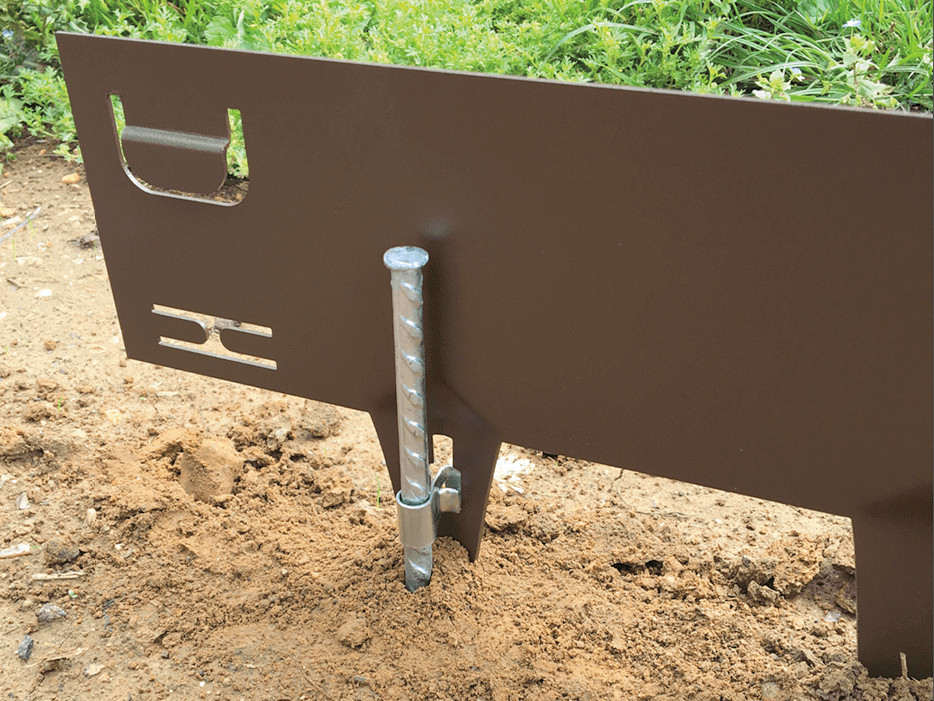
Concrete Bedded
There will be other circumstances where it is advisable to install the Core Edge system into a bed of concrete and haunch with the same.
The most obvious applications are for pavement restraint where the planned surface is heavier than normal, or may carry vehicular traffic. Core Edge used as a very discreet retainer for block paving is a typical example...
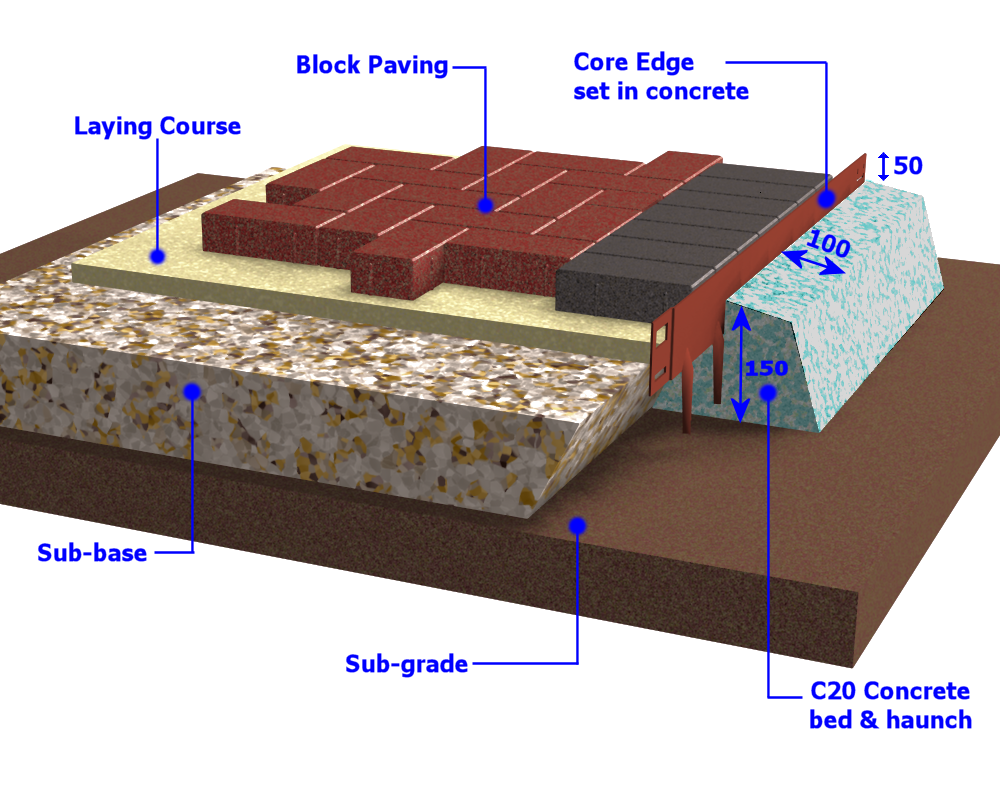
....but another, sometimes overlooked potential use for the concrete-bedded option is where the sub-grade is stony or exceptionally hard, and getting the anchor spikes to penetrate to a secure depth might prove difficult. This is explored further in the Case Study below.
Installation Case Study
This case study follows the installation of Core Edge HD, in 2275mm lengths, as the edge restraint system for an informal path across a grassed area popular with local residents and dog-walkers.
The path lies immediately adjacent to an important historic site and so it was important to the site's managers that any excavation and ground disturbance was to kept to a minimum.
Traditional concrete edgings would have required a relatively deep dig, up to 300mm where a 200mm edging is used with 100mm concrete bed, and this was considered to present too much disturbance. Timber edgings with sharpened timber pegs at regular separations would require much less excavation, but the pegs typically penentrate to 400-450mm, and there is the consideration that timber edgings often have a relatively short service life.
Core Edge HD, the tough 2.5mm thick version, with a 100mm face, manufactured in Britain from quality steel, galvanised and powder coated to add protection, offers a much longer service life than timber and requires a dig depth of only 50-60mm, just enough to skim-off the turf and vegetation. The path was designed to lie roughly 40-50mm above the existing ground level and to rely on banking-up additional topsoil to accommodate the minor height difference between the new path and the surrounding grassland.
The path itself was to be a shallow construction using Core Tree Root Protection (TRP) System, which incorporates Gravel Stabiliser panels with a Geo-Web sub-base reinforcement, plus a tough Geo-Grid to improve the load-bearing capability of the completed pathway.
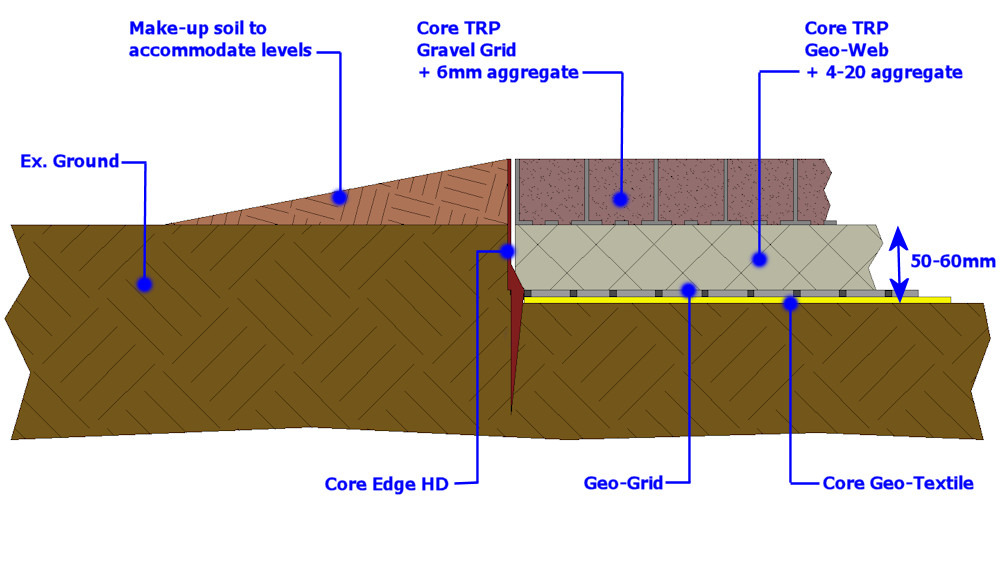

Installation:
The first task is to mark out the pathway, allowing 100mm or so ‘spread’ at each side, and then excavate to remove the surface vegetation and the uppermost level of topsoil.
As described above, this particular site requires minimal excavation as there may be buried items of archaeological interest therefore excavation depth is limited to 50-60mm.
The simple site scrape reveals the sub-grade varies from a clayey topsoil at the higher end (farthest from the camera in the photograph below) to an area of crushed aggregate at the lower end, where a long-abandoned field entrance had become overgrown.
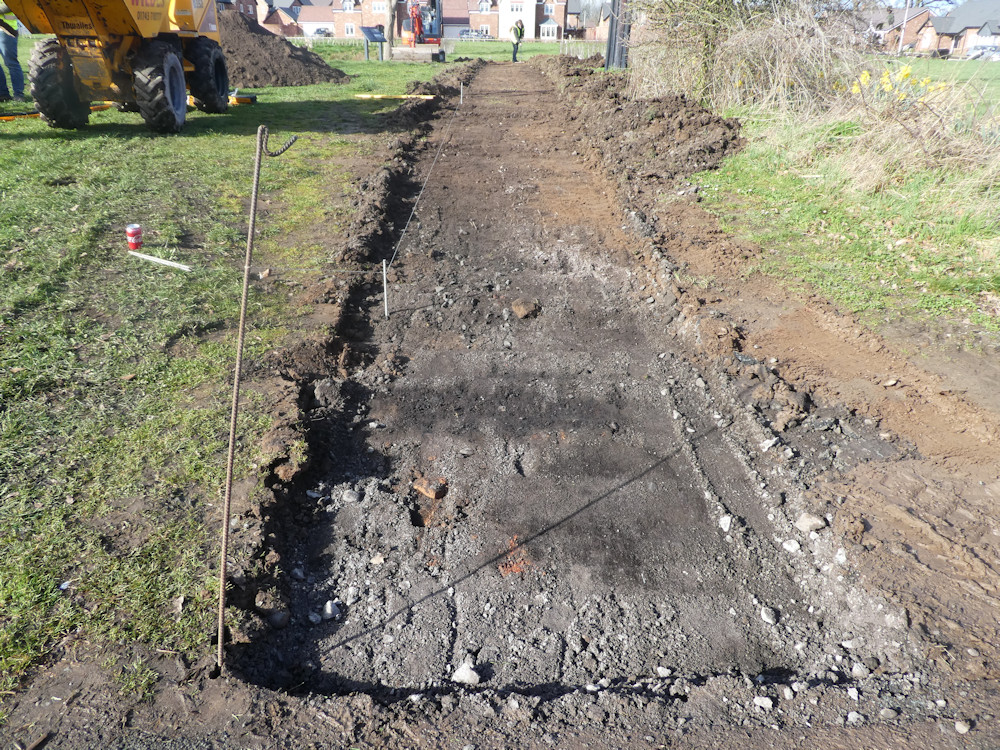
A series of line pins are established on the left-hand side of the path. A string line will be stretched taut between the pins to act as a guide to level and alignment,
The chosen edging for this project is Core Edge HD , which comes in two length options: 1075mm and 20175mm. For speed of installation, the contractor has selected the 2275mm lengths, and these are laid out close to where they will be installed.
Note that each length has a definite ‘male’ and ‘female’ end, where the ‘locking tabs’ of the male end latch into the pre-formed holes of the female end, so it is important to ensure that the edgings are laid out in the correct sequence.
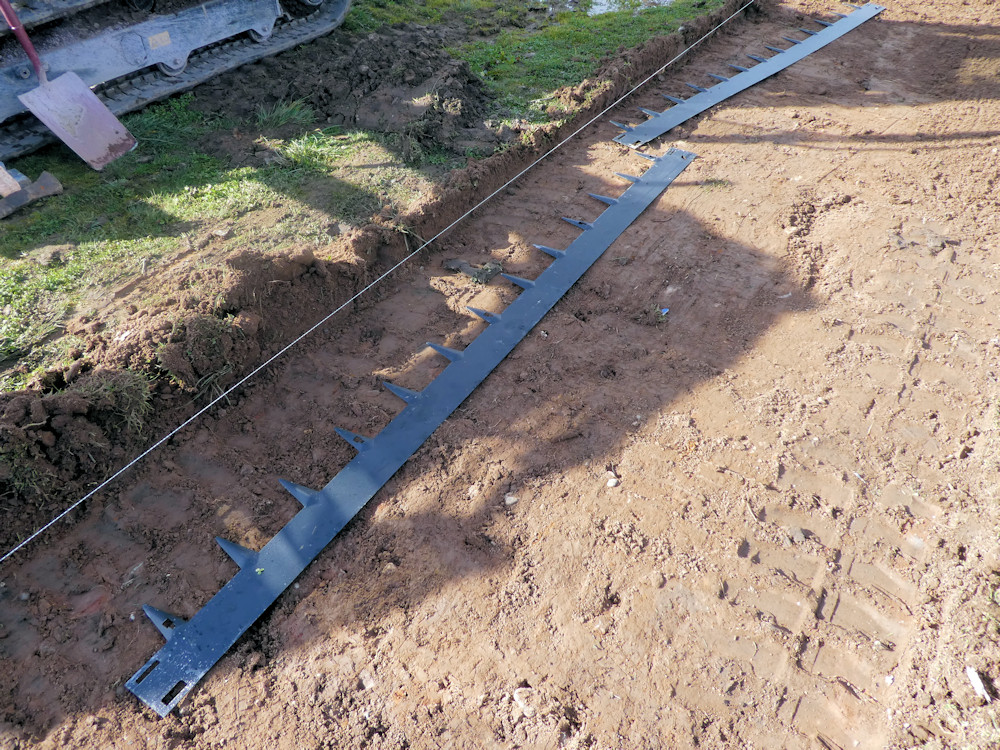
The first edging section is positioned on the excavated sub-grade and aligned with the taut string line. Once the installer is confident with the alignment, the ground spikes of the edging section can be driven into the sub-grade by forcefully hitting the top of the edging with a hammer at various points along its length.
To prevent damage or distortion of the steel edging, it’s best practice to use a block or wood or similar to act as a ‘cushion’ between the hammer and the edging section.
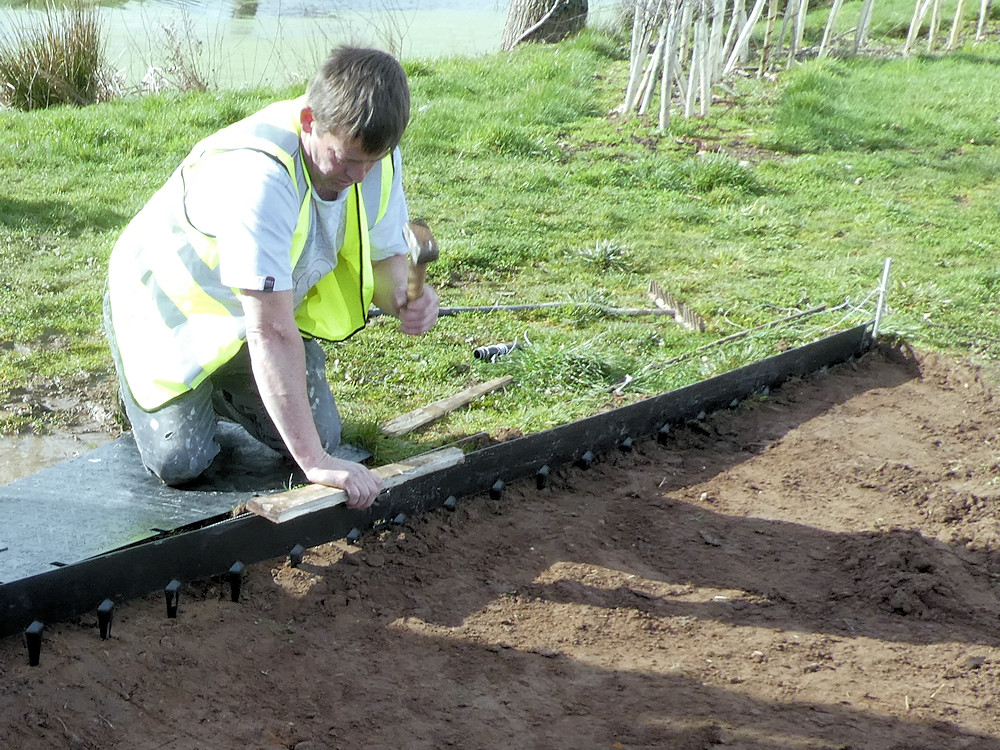
The key aim at this stage is to ensure the Core Edge HD section is accurately aligned. It will not be hammered down to final level just yet as attaching the subsequent sections may affect the resting height of that installed section. The final level of the edgings will be set once a significant run of the edgings is in place.
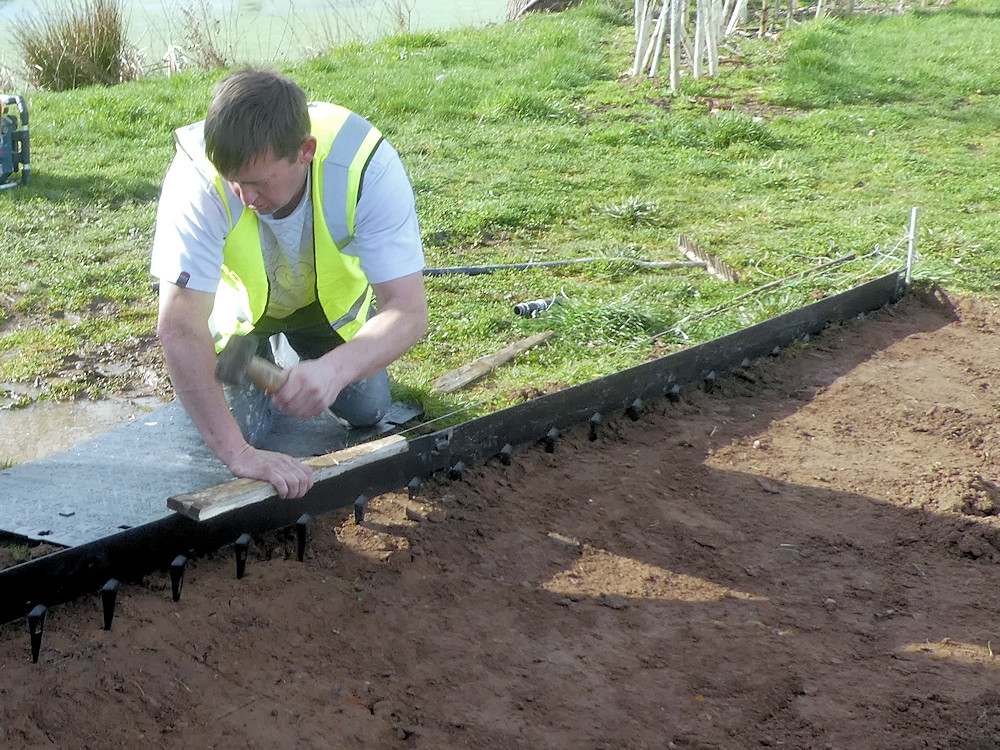
Once the first section of Core Edge HD is in position the next section can be attached, aligned, and tapped into place.
Core Edge has a unique ‘double lock’ attachment system. The main ‘tongue’ nearest the top of the section locks into the pre-formed hole in the adjacent edging section and holds the new section loosely in place, while the secure locking tabs, near the base of the section, are pulled through the matching hole of the preceding section using long-nosed pliers and bent back to securely fasten the two section together.

Once the main tongue of one section is in place through the complementary hole in the next section and holding the two sections together, the smaller locking tabs are pulled through using the pliers.
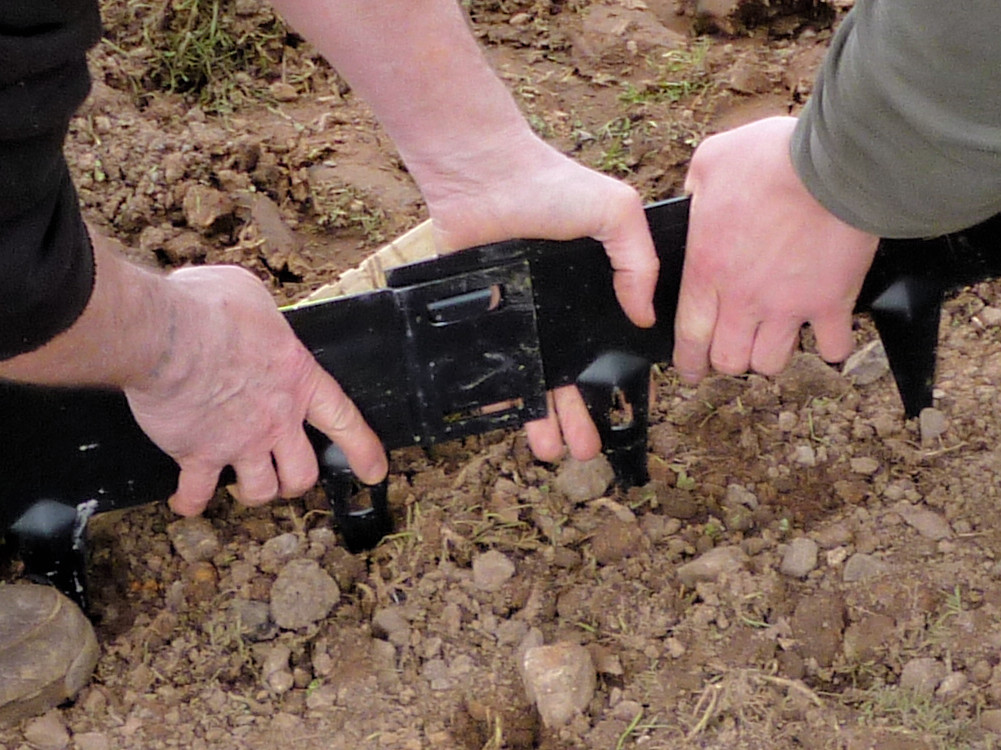
This is task best undertaken by two operatives, one holding the new section in position while the second aligns the tongue and tabs, and then uses the piers to pull through the two locking tabs.
With the Core Edge HD , the locking tabs are a full 2.5mm thick, so quite tough and it can take considerable force to bend them through the hole and fold them back to lock the two section in place.
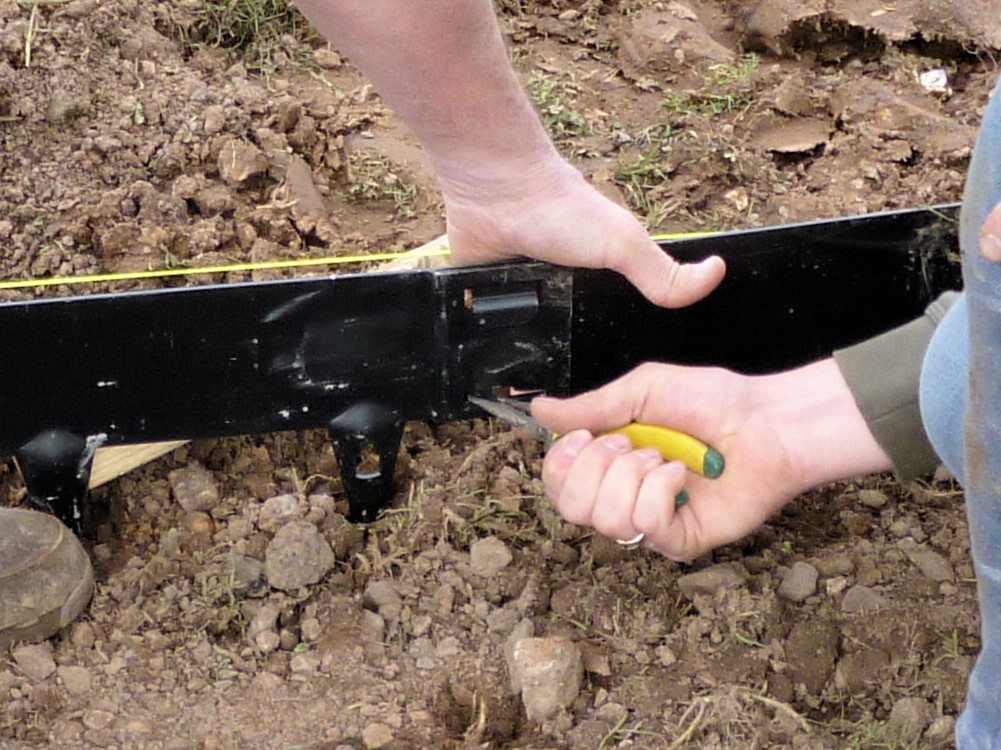
One tip these experienced installers use is to lever the locking tabs using the pliers until they poke through and stick out perpendicular to the Core Edge section, and then use a hammer to bend them back and flat, locking the sections together. Place a sledge hammer to the rear of the joint to absorb the blow as the hammer bends the locking tabs flat.
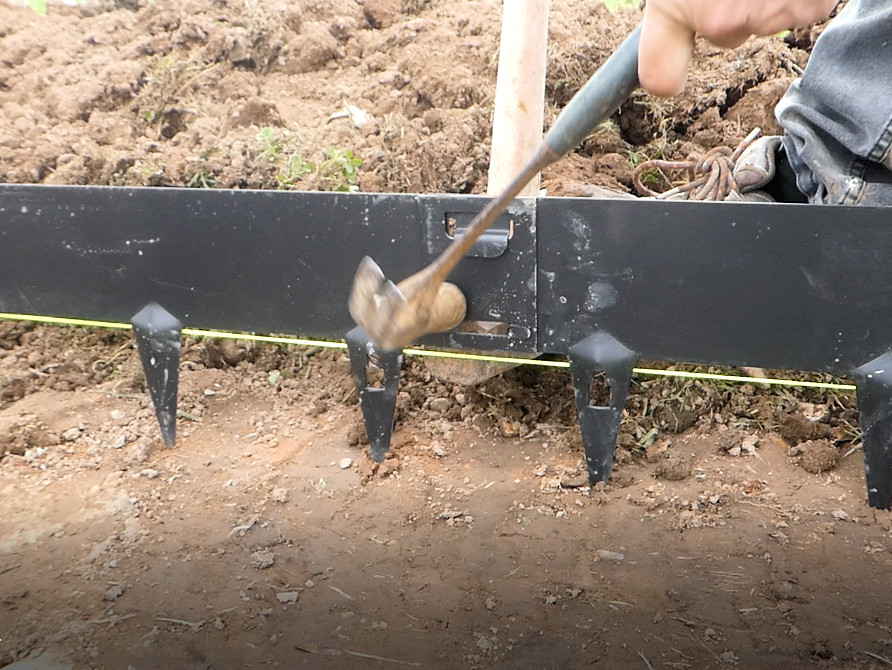
Another handy tip from the installers is that the locking mechanism of Core Edge HD is so reliable and sturdy that they can 'pre-assemble' two or three sections at a time and lift them into position with no fear of the individual sections coming apart when hoisted up and carried.
That’s all there is to it. The same process is repeated, placing the Core Edge section, lightly tapping it into position, attach to the neighbouring section, knock flat the locking tabs, and on it goes.
Once a run of edgings is in place and correctly aligned, the operatives will return and complete the tapping down, using a hammer and the wooden block to settle each section to the correct height. On this project, there is a gentle roll-over as the path descends the gradient, so precise position regarding level is left more to the judgement of the eye than the exactness of the taut string line.
And yet another useful tip from these installers is especially handy when installing the Core Edge system to rollovers such as this. They only fasten one of the two locking tabs when initially installing the edgings. This allows adjacent sections to be ‘dipped’ as necessary to create the rollover.
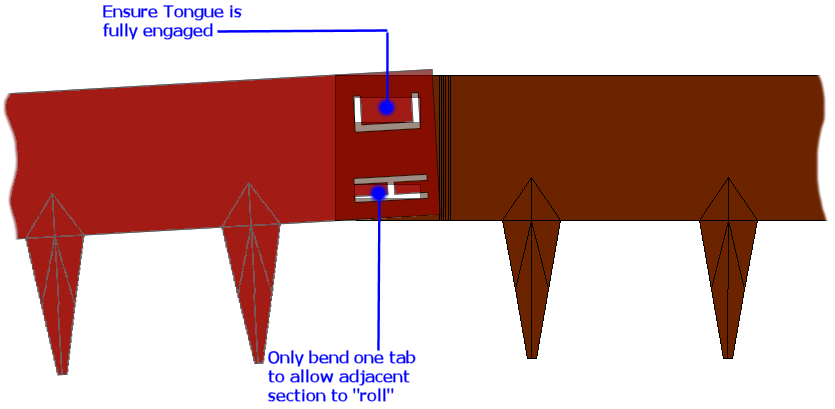
When the sub-grade is stony or otherwise difficult to penetrate with the Core Edge HD ground spikes, it’s easier to cut a shallow trench through the sub-grade, deep enough to accommodate the edging section, fill it with lean-mix concrete, and then lay the edging sections directly into that.
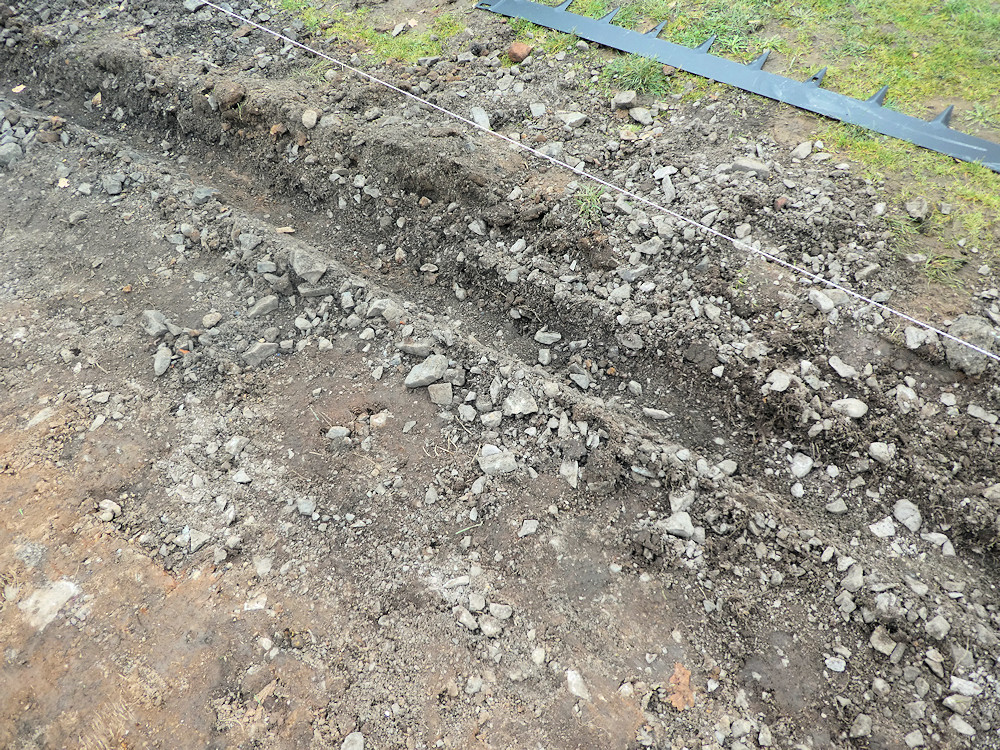
There’s no great need to use a higher-strength concrete as would normally be used with concrete bedded kerbs, as the specification is for a ground-bedded edging. The purpose of the concrete is merely to act as ‘replacement sub-grade’ which is more easily penetrated by the ground spikes but will provide adequate support once hardened.
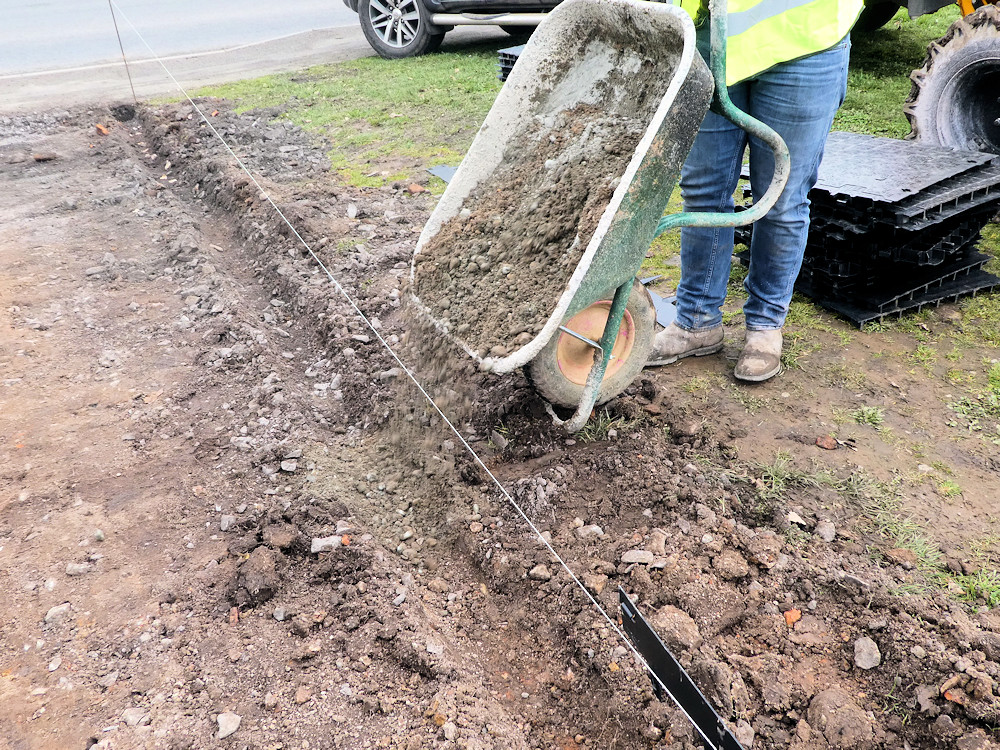
The Core Edge sections are laid in precisely the same manner when installed onto a concrete bed. The tongue and tabs are locked together and the edging is tapped down to level using a hammer with a block of wood. The only real difference is that, once the alignment and level are set, the sections can be lightly haunched with additional concrete.
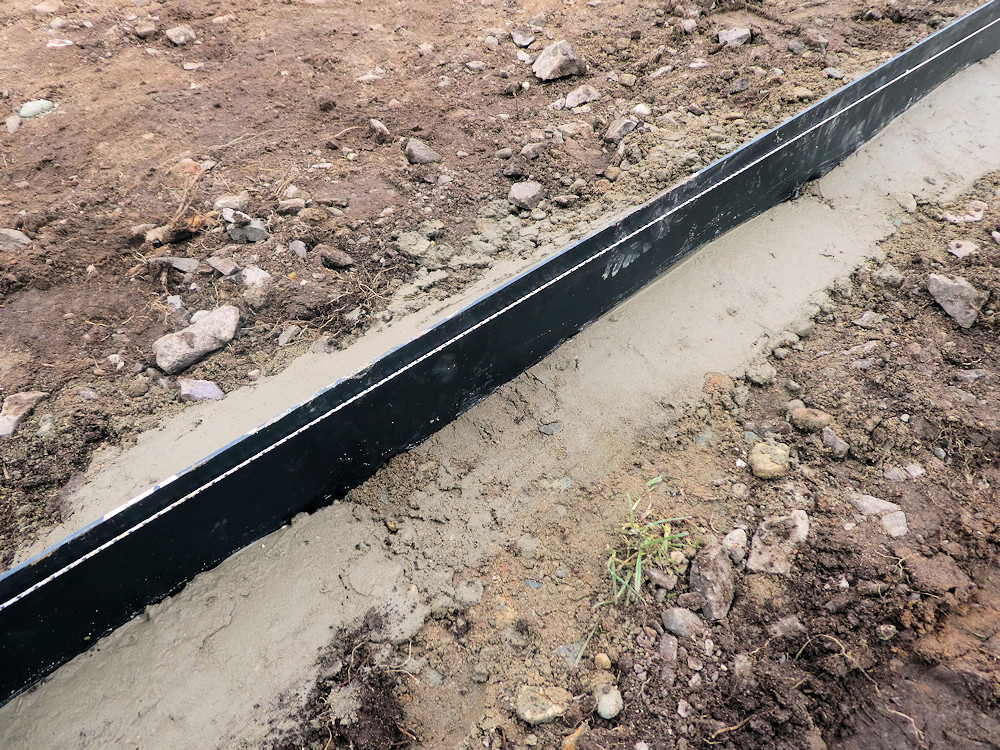
It really is that simple! Where sections require cutting, this is easily achieved using a angle-grinder or cut-off saw fitted with a suitable metal cutting blade. The flexibility of the Core Edge sections enables curves and arcs to be formed with ease, and it can even be bent-to-shape as required to form basic corners and returns.
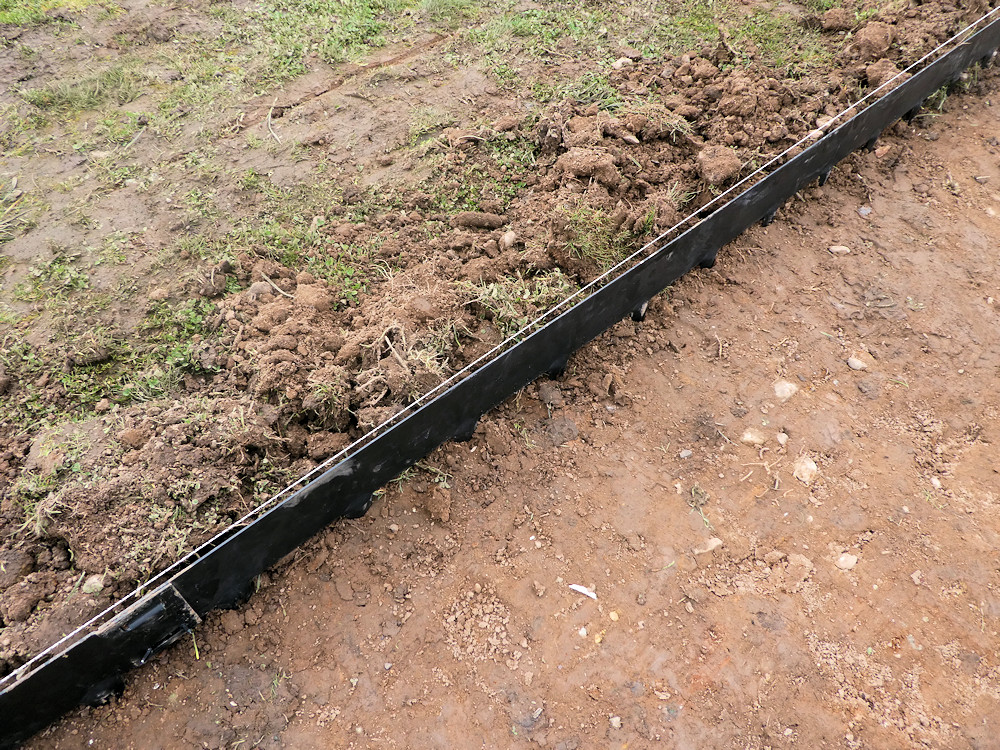
As soon as the installer is satisfied with alignment and level, the edging can be backfilled as required. On this project, it is backfilled on the outside edge as the pathway will be constructed against the inside edge.
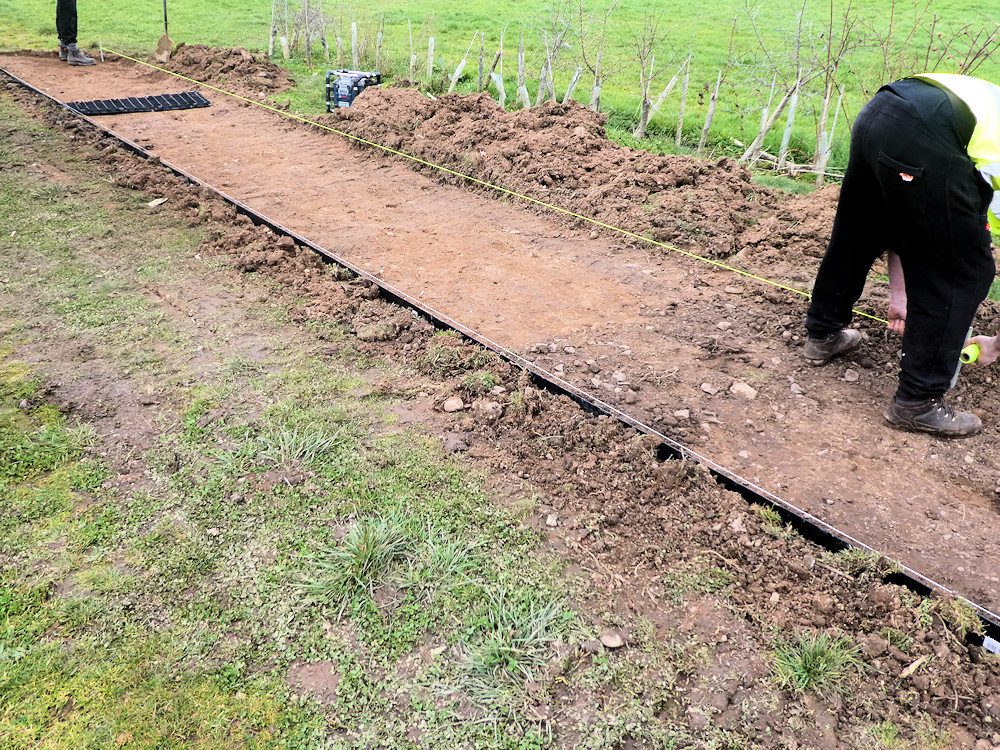
To install the edging on the opposite side of the pathway, a parallel taut string line is established at the required path width, and the whole process is repeated. 60 metres of edgings installed in just a couple of hours!
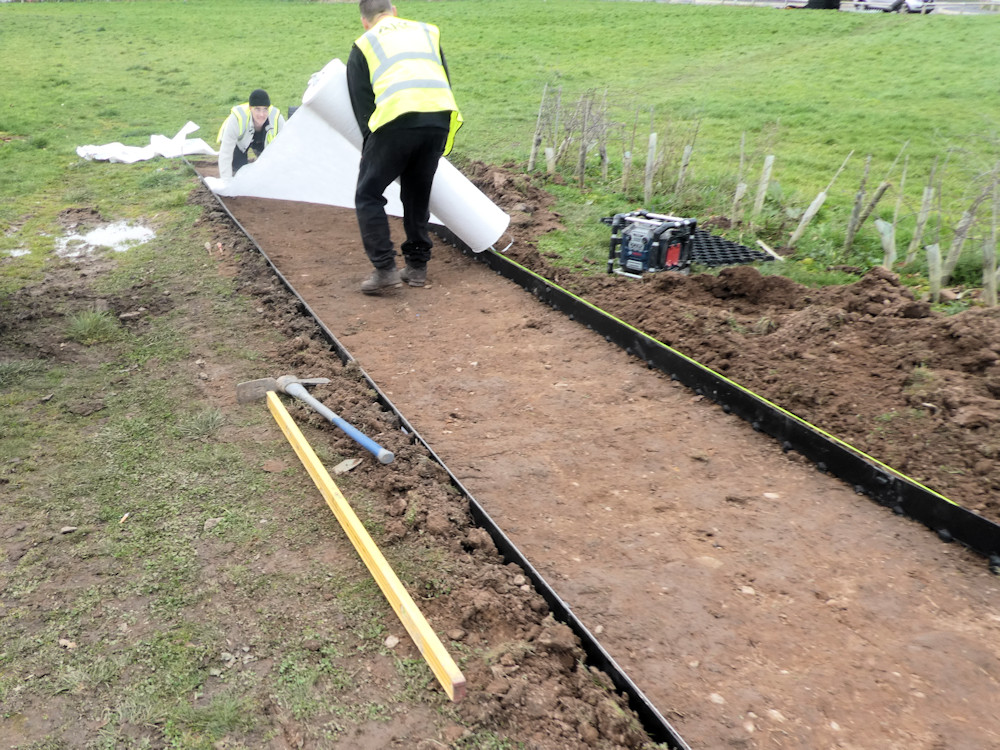
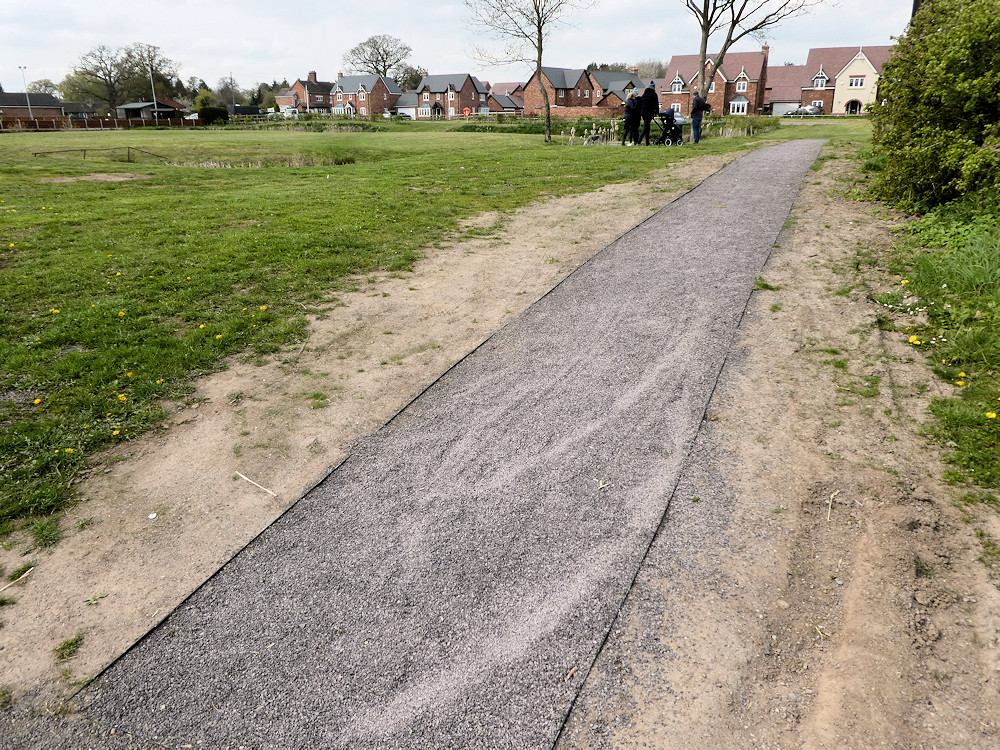
Video:
Contact Info:

Core Landscape Products
Core Gravel UK Ltd.
Units 1 – 3 Calves Lane Yard
Bellswood Lane
Iver
SL0 0LU

Tel: 01753 652 555
FreePhone: 0800 118 2278